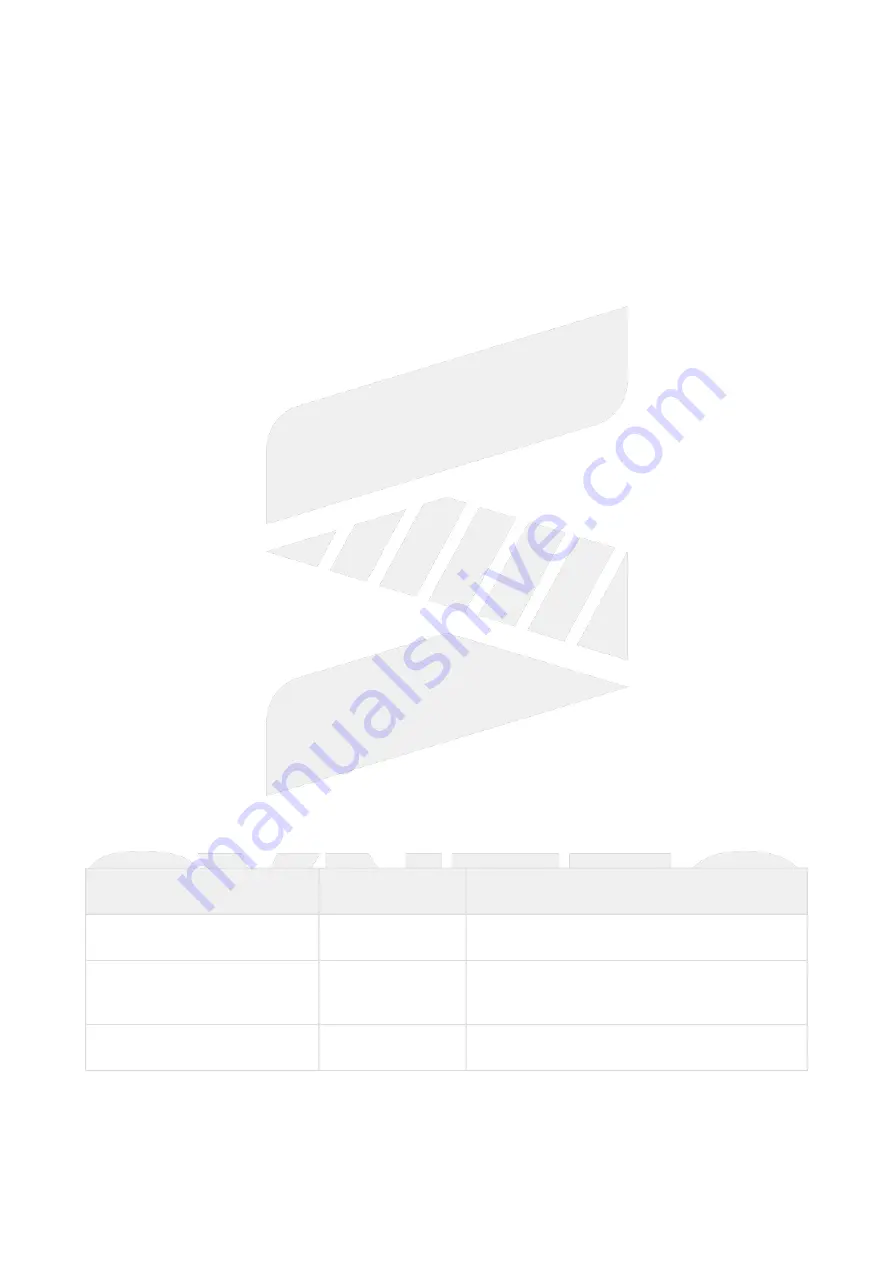
伺服產品
/Servo Products
–
Hardware Manual of 380V 7.5kW Servo Drive II (SPD-32C1-075)
Wiring and Signal (SPD-32C1-075)
–
39
1.
2.
3.
4.
1.
2.
1.
2.
3.
4.
1.
2.
1.
1.
The single-axis axial type (SVD) has 1 set of encoder feedback (6PIN), the spindle type (SPD) has 2 sets of
encoder feedback (6PIN), and each encoder interface has a 5V power output (maximum 150mA).
Support Tamagawa, SYNTEC, NIKON encoder interface
Support optional expansion modules to receive other encoder interfaces (refer to
the operation document
of servo 10PX1/10PX3 expansion modules)
Absolute encoder battery voltage detection function
Host control serial communication:
Mechatrolink-III serial communication 100Mbps
EtherCAT serial communication 100Mbps (not supported yet)
Universal IO signal:
2 groups of DI input contacts
1 set of DO output contacts
Absolute battery input
Notes
NC: Null contact
I point: I point needs to input the voltage relative to COM24V
Point O: O0+ and O0- are internally turned on
STO input/output:
2 groups of safety inputs (STO-A, STO-B)
1 group of safety function feedback (STO-FB)
USB communication:
Can be connected with PC to set the internal parameters of the servo and monitor the running status.
LED display:
Operational status and power indication
11.2
Connector and Terminal Definition
Name
Terminal code
Description
Main circuit power input terminal
R
、
S
、
T
Connect three-phase AC power
Control board power
L1, L2
L1, L2 can be connected or not connected,
according to the wiring plan
Motor power input terminal
U
、
V
、
W
Connect the motor