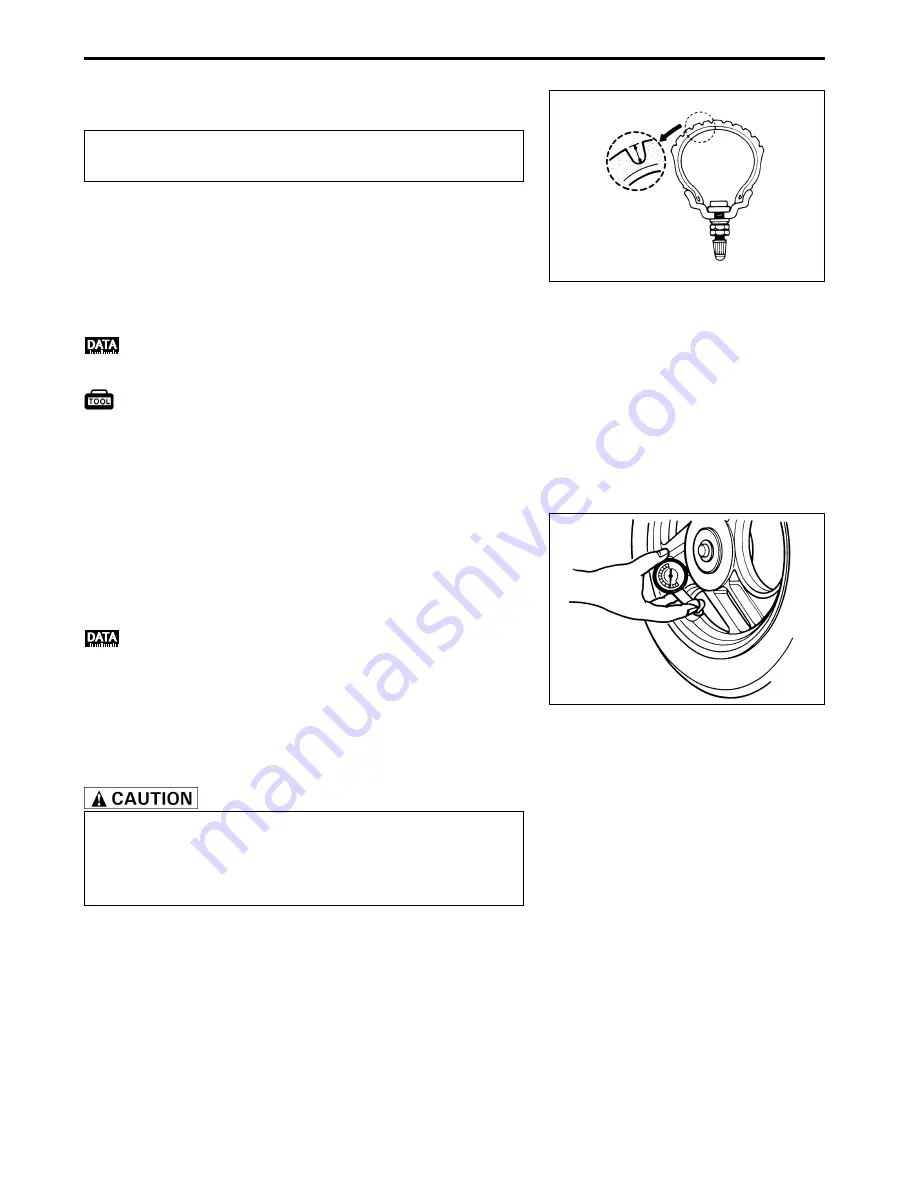
2-12
PERIODIC MAINTENANCE
TIRES
Inspect initially at 1 000 km (2 months) and every
3 000 km (6 months) thereafter.
TIRE TREAD CONDITION
Operating the motorcycle with excessively worn tires will de-
crease riding stability and consequently invite a dangerous situ-
ation. It is highly recommended to replace a tire when the re-
maining depth of the tire tread reaches the following specifica-
tion.
Tire tread depth (front and rear)
Service Limit: 1.6 mm
09900-20805: Tire depth gauge
TIRE PRESSURE
If the tire pressure is too high or too low, steering will be ad-
versely affected and tire wear will increase. Therefore, maintain
the correct tire pressure for good roadability and a longer tire
life. Cold inflation tire pressure is as follows.
Cold inflation tire pressure
Solo riding
Front: 125 kPa (1.25 kgf/cm
2
)
Rear: 175 kPa (1.75 kgf/cm
2
)
Dual riding (except for UF50Z)
Front: 125 kPa (1.25 kgf/cm
2
)
Rear: 230 kPa (2.30 kgf/cm
2
)
The standard tire fitted on this motorcycle is 120/70-12
51L for the front and 130/70-12 56L for the rear. The use
of tires other than those specified may cause instabil-
ity. It is highly recommended to use the specified tires.
Summary of Contents for UF50
Page 1: ...9 9 5 0 0 1 0 4 9 1 0 1 E UF50 ...
Page 26: ...2 14 PERIODIC MAINTENANCE 1 2 3 4 5 6 7 8 6 9 0 A B C ...
Page 162: ...SERVICING INFORMATION 7 11 ...
Page 164: ...SERVICING INFORMATION 7 13 ...
Page 185: ...Printed in Japan Y K1 ...