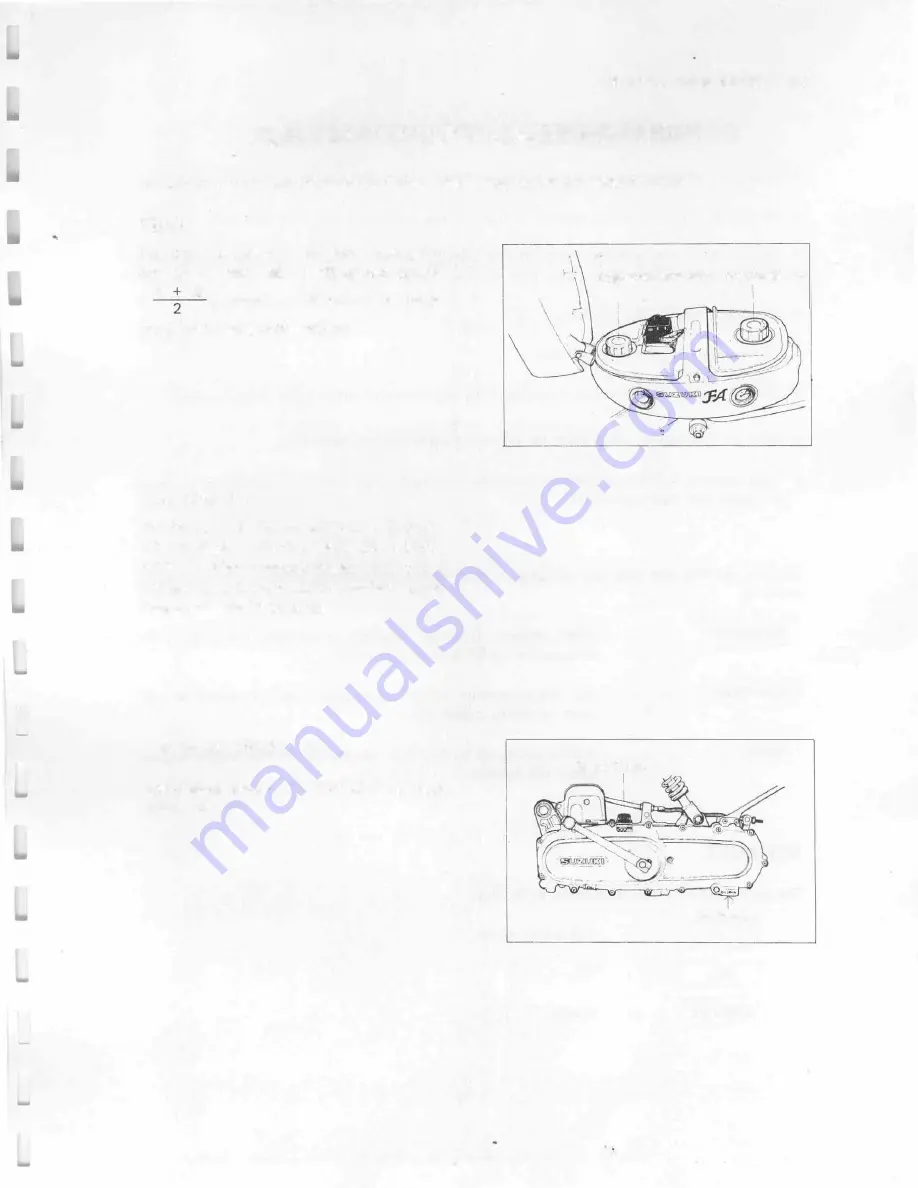
GJ:NER.AL
/,'\'f-'ORAli\
Tf()1\'
1-5
FUEL AND OIL RECOMMENDATION
Be sure to use the specified fuel and oils. The fol lowing are the specifications:
FUEL
Use only un leaded or l ow-lead type· gaso
l i ne of at least
85
-
95 pump octane
( R
M method) or 89 octane or higher
rated by the Research method.
ENGINE OIL
For the SUZUKI CCI system, use of SUZUKI
CCI S U P E R 2-CYCLE MOTOR LUB RI
CANT is highly recommended, but if
it
is
not available, a .good qua l ity synthetic based
2-cycle oil should be used.
TRANSMISSION OIL
Use a good quality SAE 20W/40 multi-grade
motor oil.
Engine o i l tank cap
Fuel tank cap
..
Oil filler cap
Drain plug
Summary of Contents for FA50
Page 1: ......
Page 62: ... I 8 SF R I JCJ IG INFOl M TTON WIRE AND CABLE ROUTING WIRING ROUTING u a I 5 u c 0 e c en ...
Page 74: ......