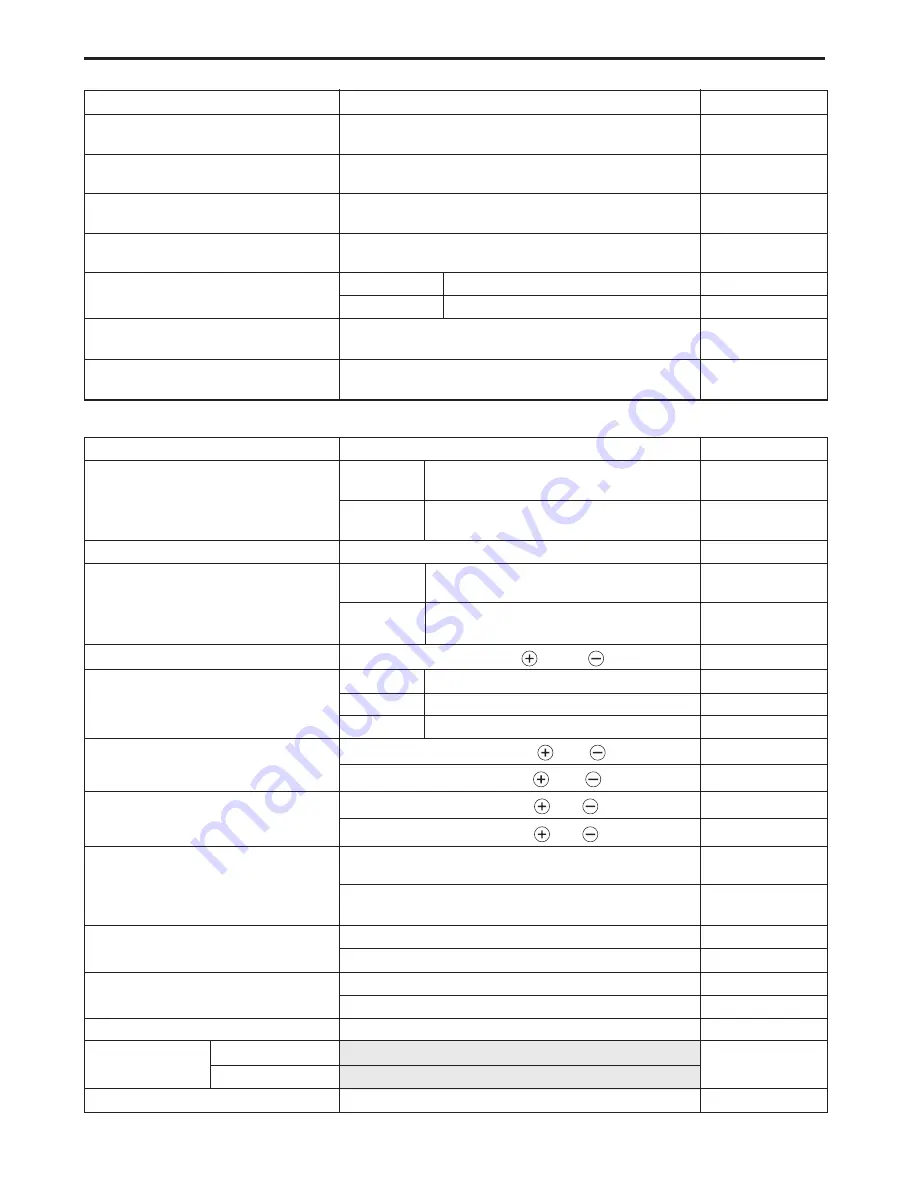
10-12
DR-Z400/EK1 (’01-MODEL)
ITEM
STANDARD/SPECIFICATION
LIMIT
Rear shock absorber gas
900 kPa
pressure
(9.0 kgf/cm
2
, 128 psi)
———
Rear shock absorber oil type
SUZUKI REAR SUSPENSION OIL SS-25
or an equivalent suspension oil
———
Rear shock absorber oil capacity
380 ml
(12.8/13.4 US/Imp oz)
———
Rear shock absorber spring
258.0
pre-set length
(10.2)
———
Rear shock absorber damping
Rebound
13th clicks turn back
———
force adjuster
Compression
12th clicks turn back
———
Rear wheel travel
295
(11.6)
———
Swingarm pivot shaft runout
0.3
———
(0.01)
ELECTRICAL
ITEM
SPECIFICATION
NOTE
Spark plug
Type
DENSO: U24ESR-N
NGK: CR8E
Gap
0.7 – 0.8 mm
(0.028 – 0.031 mm)
Spark performance
Over 8 mm (0.3 in) at 1 atm.
Ignition coil resistance
Primary
0.1 – 1.0
Ω
Terminal –
Ground
Secondary
12 – 20 k
Ω
Plug cap –
Terminal
Ignition coil primary peak voltage
More than 150 V (
: B/W,
: B/Y)
Generator coil resistance
Charging
0.50 – 1.25
Ω
Y – Y
Signal coil
0.05 – 0.20
Ω
B – W
Pick-up coil
390 – 600
Ω
G – Bl
Pick-up coil peak voltage
More than 10.0 V (
: Bl,
: G)
DR-Z400
More than 5.0 V (
: Bl,
: G)
DR-Z400E
Signal coil peak voltage
More than 1.0 V (
: B,
: W)
DR-Z400
More than 1.4 V (
: B,
: W)
DR-Z400E
Generator no-load voltage
More than 55 V (AC) at 5 000 r/min.
(when engine is cold)
(Y – Y)
DR-Z400
More than 75 V (AC) at 5 000 r/min.
(Y – Y)
DR-Z400E
Regulated voltage
12.5 – 14.0 V at 5 000 r/min.
DR-Z400
13.5 – 15.0 V at 5 000 r/min.
DR-Z400E
Generator Max. output
150 W at 5 000 r/min.
DR-Z400
200 W at 5 000 r/min.
DR-Z400E
Starter relay resistance
3 – 5
Ω
DR-Z400E
Battery
Type designation
* YT7B-BS
DR-Z400E
Capacity
* 12 V 21.6 kC (6 Ah)/10 HR
Fuse size
10 A
DR-Z400E
Summary of Contents for drz 400E
Page 1: ...DR Z400 E 9 9 5 0 0 4 3 0 2 2 0 1 E...
Page 49: ...ENGINE 3 7 Remove the engine from the frame...
Page 83: ...ENGINE 3 41 1 Countershaft 2 Driveshaft 2 1 A...
Page 135: ...6 4 CHASSIS Left Right Left Right Left Right Spacer Clearance...
Page 157: ...6 26 CHASSIS Left Right Except E 03 28 Spacer Left Right Right Left Clearance...
Page 236: ...8 12 SERVICING INFORMATION WIRE HARNESS CABLE AND HOSE ROUTING WIRE ROUTING...
Page 239: ...SERVICING INFORMATION 8 15 FUEL HOSE AND FUEL TANK MOUNTING...
Page 242: ...8 18 SERVICING INFORMATION FRONT BRAKE HOSE ROUTING REAR BRAKE HOSE ROUTING...
Page 334: ...Printed in Japan Y K1 K2 TK...