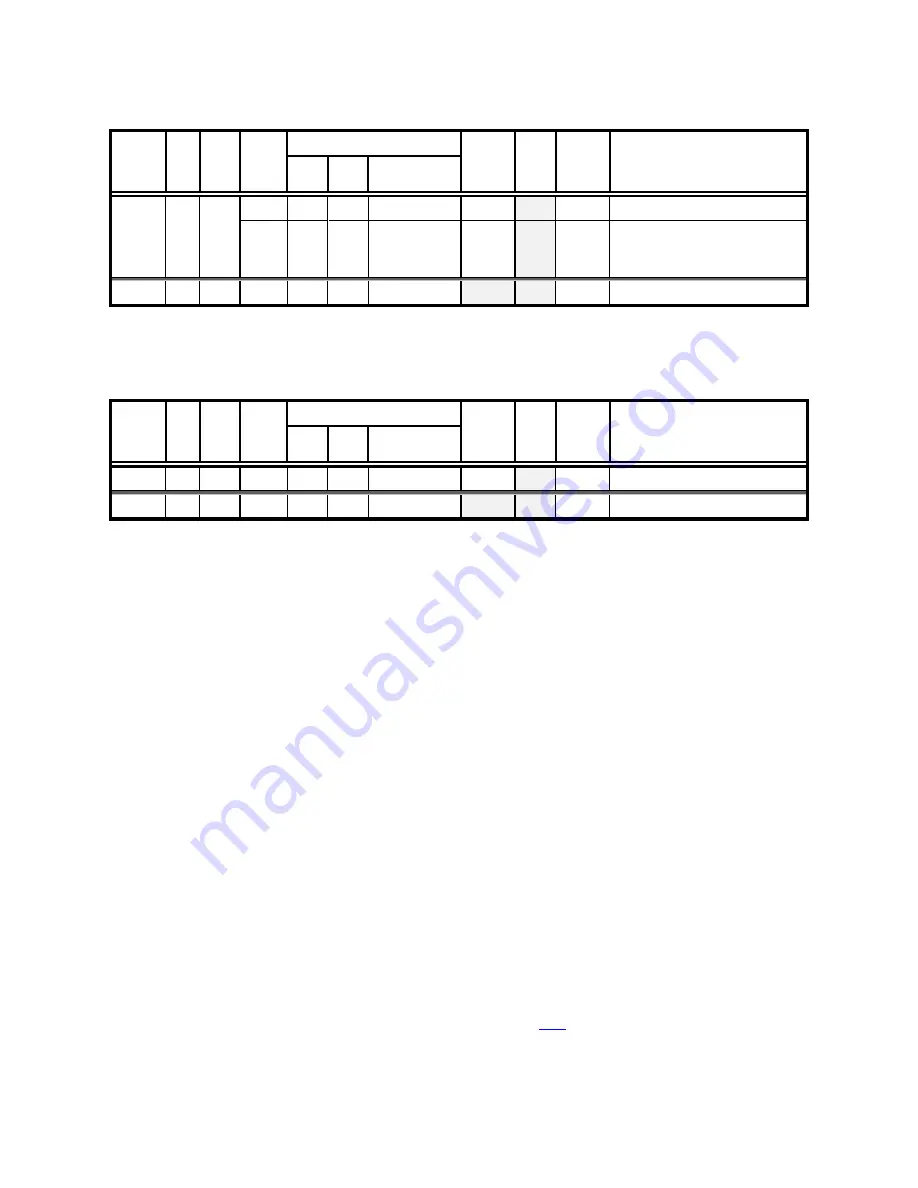
32
TRIO MP-245A FOUR-AXIS MICROMANIPULATOR SYSTEM OPERATION MANUAL – REV. 3.12B (20191001)
Table 4-15. Set the angle (‘A’) command.
Tx/-
Delay/-
Rx
Ver. Total
Bytes
Byte
Offset
(Len.)
Value
Alt-
key-
pad #
Ctrl-
char
ASCII
def./-
char.
Description
Dec. Hex.
Binary
Tx
All 2
0
65 41 1010 1001 0065
‘A’
Command
1
0
-
90
00
-
5A
0000 0000
-
0101 1010
0000
-
0090
<NUL>
-
‘z’
Angle in degrees between 0 and
90. See
Angle Setting &
Movement
note
Rx
1
0
13 0D 0000 1101
<CR>
Completion indicator
4.7.12
Recalibrate (‘R’) Command
Recalibrates the connected micromanipulator/stage to 1,000 microns in each axis.
Table 4-16. Recalibrate (‘R’) command.
Tx/-
Delay/-
Rx
Ver. Total
Bytes
Byte
Offset
(Len.)
Value
Alt-
key-
pad #
Ctrl-
char
ASCII
def./-
char.
Description
Dec. Hex.
Binary
Tx
All 1
0
82 62 1000 0010 0082
‘R’
Command
Rx
1
0
13 0D 0000 1101
<CR>
Completion indicator
4.7.13
Notes
1.
Task-Complete Indicator: All commands will send back to the computer the “Task-
Complete Indicator” to signal the command and its associated function in controller is
complete. The indicator consists of one (1) byte containing a value of 13 decimal (0D
hexadecimal), and which represents an ASCII CR (Carriage Return).
2.
Intercommand Delay: A short delay (usually around 2 ms) is recommended between
commands (after sending a command sequence and before sending the next command).
3.
Clearing Send/Receive Buffers: Clearing (purging) the transmit and receive buffers of the
I/O port immediately before sending any command is recommended.
4.
Positions in Microsteps: All positions sent to and received from the controller are in
microsteps (µsteps). See
Microns/-microsteps conversion
table) for conversion between
µsteps and microns (micrometers (µm)).
5.
Ranges and Bounds: See
Ranges and Bounds
table for exact minimum and maximum
values for each axis of each compatible device that can be connected. All move commands
must include positive values only for positions – negative positions must never be
specified. All positions are absolute as measured from the physical beginning of travel of
a device’s axis. In application programming, it is important that positional values be
checked (>= 0 and <= max.) to ensure that a negative absolute position is never sent to
the controller and that end of travel is not exceeded. All computational relative
positioning must always resolve to accurate absolute positions.
6.
Absolute Positioning System Origin: The Origin is set to a physical position of travel to
define absolute position 0. The physical Origin position is fixed at beginning of travel
(BOT). This means that all higher positions (towards end of travel (EOT)) are positive
values; there are no lower positions and therefore no negative values are allowed.
Summary of Contents for TRIO MP-245A
Page 3: ......
Page 4: ......
Page 52: ...50 TRIO MP 245A MICROMANIPULATOR SYSTEM QUICK REFERENCE REV 3 12B 20191001 FW V3 12 NOTES...