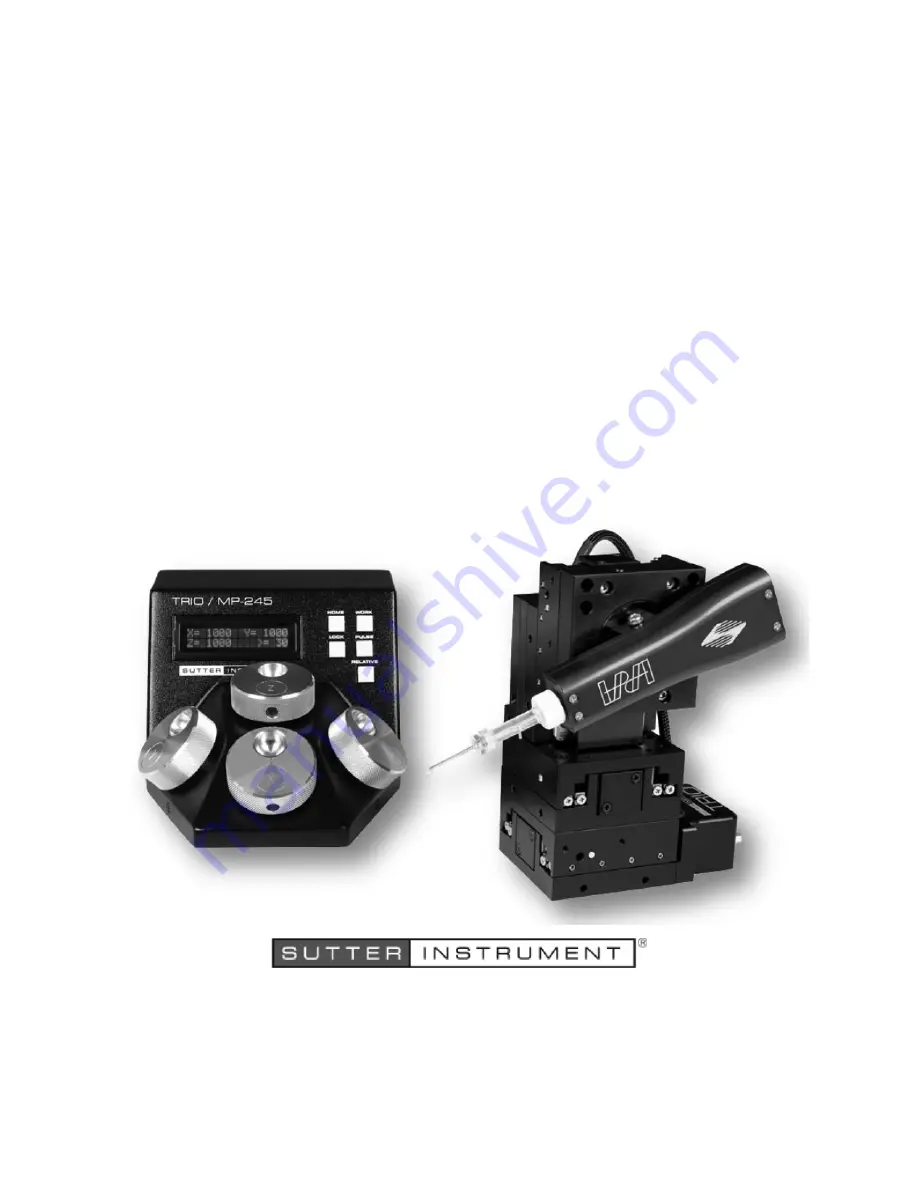
One Digital Drive
Novato, CA 94949
Voice: 415-883-0128 Web: www.sutter.com
Fax:
415-883-0572 Email: [email protected]
TRIO
™
MP-245A
Three-Axis Motorized
Micromanipulator System
With Synthetic Fourth “D” Axis and
USB Interface for External Control
Operation Manual
Rev. 3.12b (20191001)
Summary of Contents for TRIO MP-245A
Page 3: ......
Page 4: ......
Page 52: ...50 TRIO MP 245A MICROMANIPULATOR SYSTEM QUICK REFERENCE REV 3 12B 20191001 FW V3 12 NOTES...