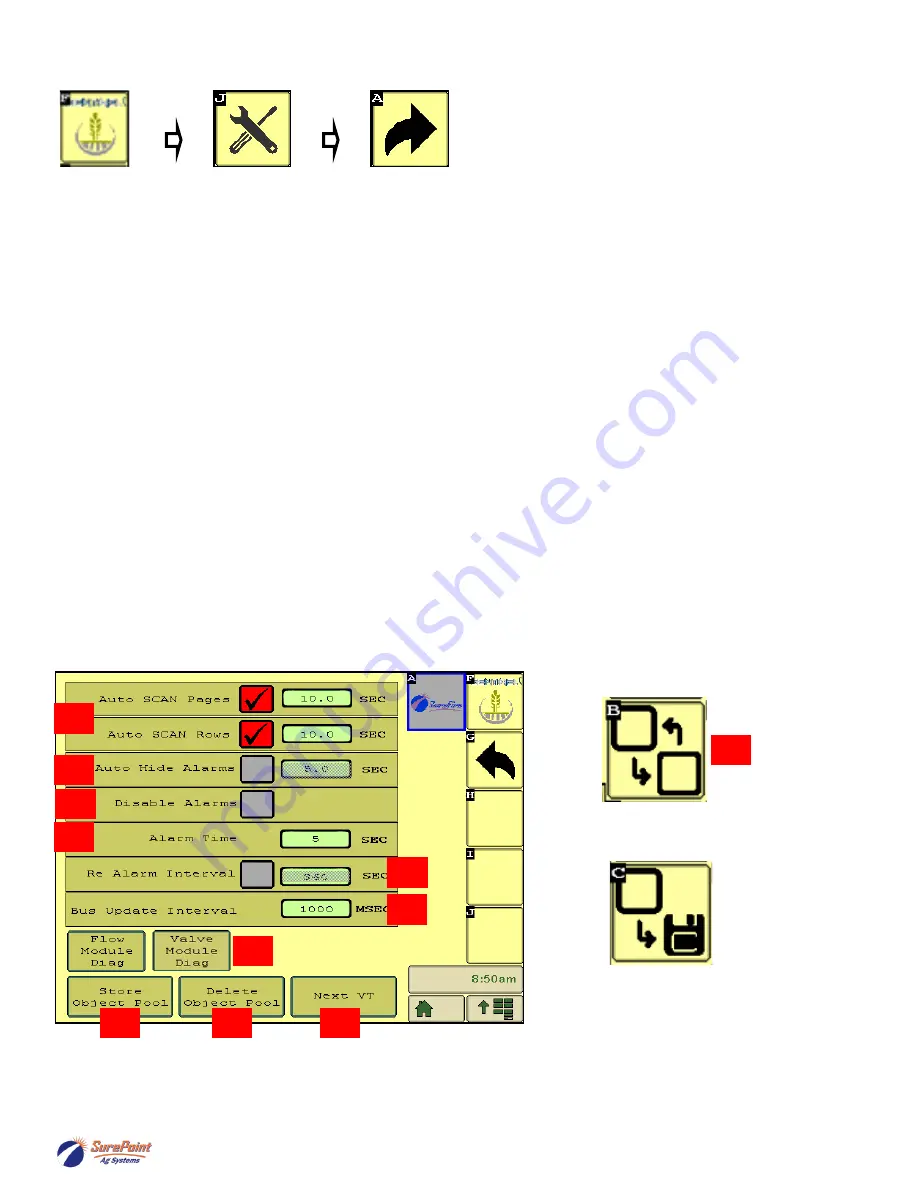
396
-
5477Y1 Sentinel Row Control Manual
©2022 SurePoint Ag Systems 41
4/29/2022
Customizing Scans & Alarms, etc
This screen allows the user to change how row information is displayed on the HOME screen.
35.) When checked, the
Auto Scan
feature will scan through the product pages and/or rows on the HOME
screen. You can change the length of time it stays on each page or row before advancing.
36.)
Auto Hide Alarms (if checked)
sets how long full
-
page alarms are displayed before they go away (see
pg. 20)
37.)
Disable Alarms
-
Check this to turn off alarms. May want to do this for testing or troubleshooting.
38.)
Alarm Time
-
how long a row must be outside of the specified tolerance before the alarm sounds
.
39. Re Alarm Interval
-
The time before the Alarm alarms again after being acknowledged. If the issue that
triggered the alarm is not resolved, it will keep alarming at this interval until resolved (if the box is
checked).
40.
Bus Update Interval
-
Use this to slow down ISOBUS traffic if the BUS load is too high.
Reset only after
talking to a SurePoint representative.
41.)
Flow Module Diagnostics
and
Valve Module Diagnostics
-
These are addressed on previous page.
Press one of these to go the Module Addressing screen.
42.)
Store Object Pool
-
Stores the current ISOBUS layout on the VT.
43.)
Delete Object Pool
-
Deletes the current object pool on the VT and forces the monitor to regenerate the
display when it is rebooted. This may be necessary after a software update or feature unlock or if some
screens or features do not appear correct.
44.)
Next VT
-
press to push Sentinel to another virtual terminal. This may be necessary if there is more
than one monitor or display in the cab.
35
37
36
40
39
38
44
43
42
41
Next VT
icon from v.1.3.0
Save to this VT
from v.1.3.0
44
SurePoint
Ag
Systems