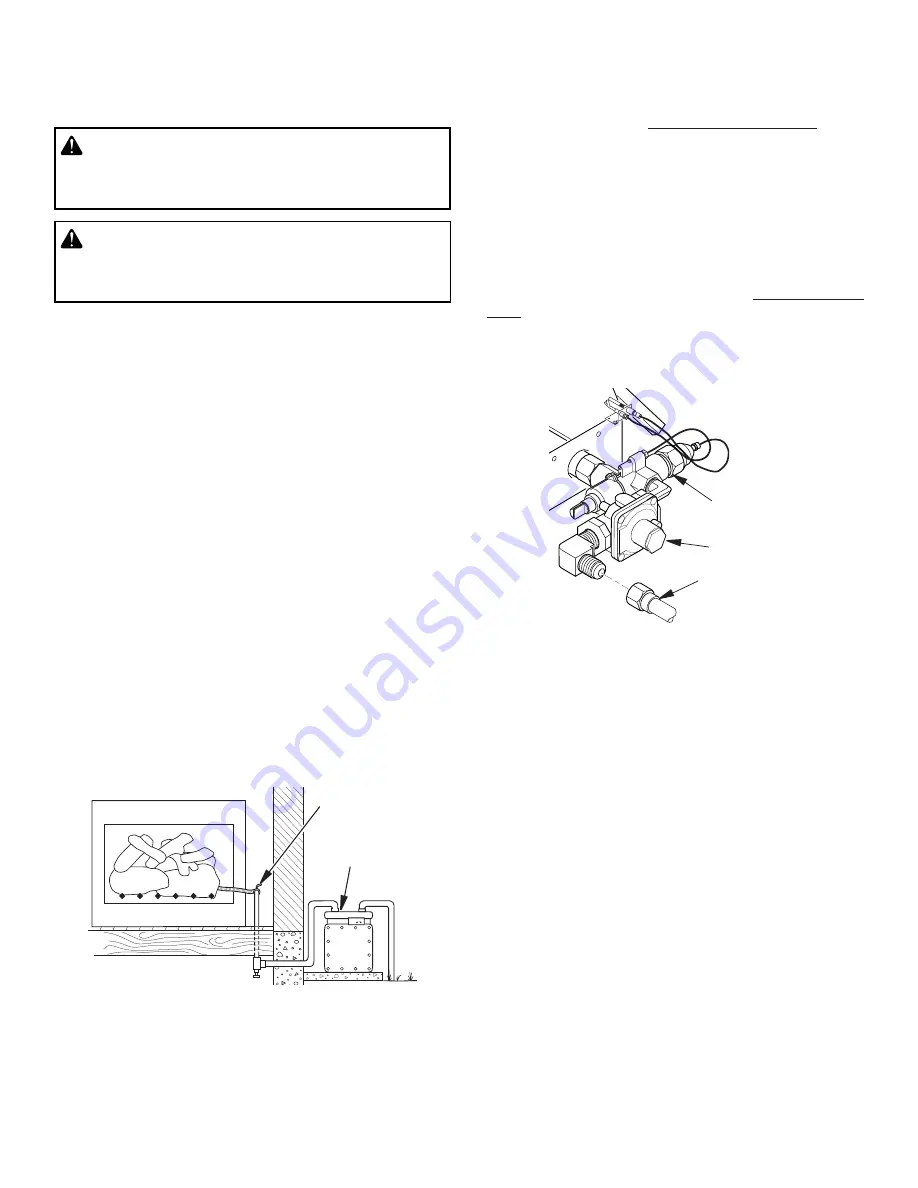
Superiorfireplaces.US.com
126900-01_B
7
CHECKING GAS CONNECTIONS
WARNING: Test all gas piping and connections,
internal and external to unit, for leaks after installing
or servicing. Correct all leaks at once.
WARNING: Never use an open flame to check for a
leak. Apply a noncorrosive leak detection fluid to all joints.
Bubbles forming show a leak. Correct all leaks at once.
PRESSURE TESTING GAS SUPPLY PIPING SYSTEM
Test Pressures In Excess Of 1/2 PSIG (3.5 kPa)
1. Disconnect log set and its individual equipment shutoff valve
from gas supply piping system.
2. Cap off open end of gas pipe where equipment shutoff valve was
connected.
3. Pressurize supply piping system by either using compressed air
or opening main gas valve located on or near gas meter.
4. Check all joints of gas supply piping system. Apply a noncorrosive
leak detection fluid to all joints. Bubbles forming show a leak.
5. Correct all leaks at once.
6. Reconnect log set and equipment shutoff valve to gas supply.
Check reconnected fittings for leaks.
Test Pressures Equal To or Less Than 1/2 PSIG (3.5 kPa)
1. Close equipment shutoff valve (see Figure 5).
2. Pressurize supply piping system by either using compressed air
or opening main gas valve located on or near gas meter.
3. Check all joints from gas meter to equipment shutoff valve (see
Figure 5). Apply a noncorrosive leak detection fluid to all joints.
Bubbles forming show a leak.
4. Correct all leaks at once.
Figure 5 - Checking Gas Joints
Figure 6 - Installing Inlet Fitting and Gas Connector Tube (Valve
Cover Removed for Clarity)
Gas Connector
Tube
Gas Control
Valve
Regulator
INSTALLATION
Continued
HEARTH PAN INSTALLATION
If using propane/LP gas, see
Propane/LP Gas Conversion
, before
installing hearth pan.
1. Place burner pan assembly in center of fireplace floor. Make sure
front of pan faces forward.
2. Thread gas supply fitting to fireplace gas supply pipe. Adjust to
most convenient position.
3. Install gas connector tube to gas supply adapter. Carefully shape
tube and attach to gas inlet fitting (see Figure 6). Be careful not
to cause kinks in tube.
4. Test for leaks following instructions under
Testing Burner for
Leaks
, page 9.
5. Retighten and adjust location of gas control as necessary. Gas
control should be level, with control rod to the front.
Gas Meter
Equipment
Shutoff Valve
Propane/LP Gas Conversion
To convert to propane/LP gas, burner inlet fitting and pilot orifice
must be replaced and regulator pressure must be reset. Propane/LP
burner inlet fitting is supplied with orifice installed. Propane/LP pilot
orifice for converting pilot is supplied and is marked with a red stripe.
1. Remove control rod extension and piezo ignitor by pulling gently.
2. Remove screws that attach pilot assembly to valve cover and
valve cover to burner pan (see Figure 7, page 8).
3. Remove valve cover.
4. Using a wrench, remove gas control valve and burner inlet fitting
by turning counterclockwise (see Figure 8, page 8).
5. Remove burner inlet fitting from gas control assembly (see Figure
8, page 8). DO NOT remove orifice from this fitting. Propane/LP
burner inlet fitting is included in hardware kit (see Figure 9, page
8).
6. Be sure to use correct orifice for your appliance. Orifice kit in-
cluded with this appliance contains an orifice installed in an air
mixer fitting.
7. Using thread sealant (resistant to the action of propane/LP gas)
on smaller end of fitting, screw burner inlet fitting into outlet side
of gas control (see Figure 8, page 8). Tighten using a wrench.