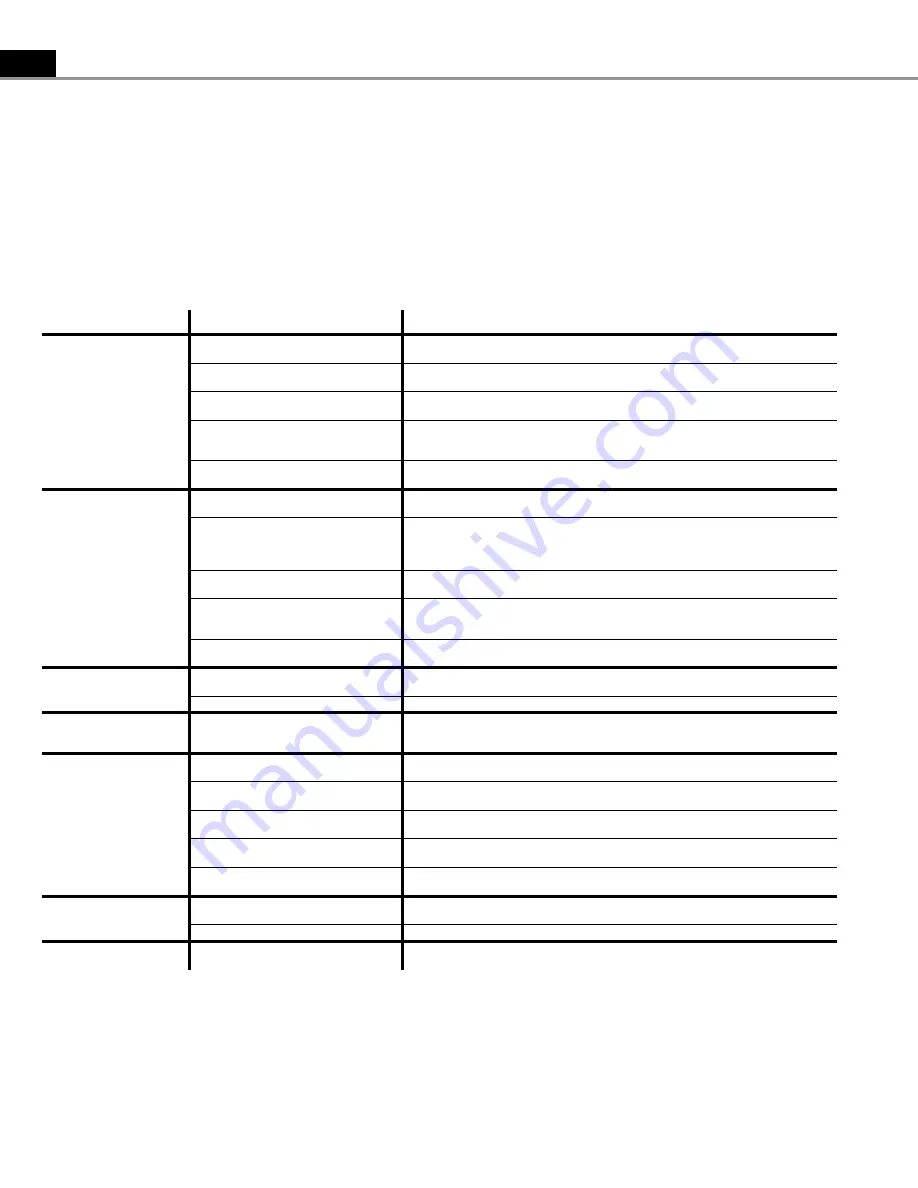
22
SunTouch TapeMat Installation Manual
If problems arise with the SunTouch TapeMat or its related electrical components, please consult this troubleshooting guide. If not
qualified to perform electrical work, it is highly recommended a qualified, licensed electrician be hired.
Any electrical troubleshooting work should be performed with the power removed from the circuit, unless otherwise noted.
Although this troubleshooting guide is provided to assist with problems experienced with a SunTouch system, results are never guar-
anteed. SunTouch does not assume any liability or responsibility for damage or injury that may occur from using this guide. If prob-
lems with the system persist, call the manufacturer.
Troubleshooting Guide
Problem
Possible Cause
Solution
Mat resistance measurement is
outside the range printed on the
nameplate label.
An analog meter (using a moving needle) was
used to take the reading.
Obtain a digital multi-meter and re-measure the resistance.
If measurement shows an open or short circuit,
the Heating Wire has been damaged.
Record resistance between all wires and contact the manufacturer.
If measurement is just a little low or high, room
temperature has affected the resistance.
Make the room temperature 75°–85°F (24°-30°C), or contact the manufacturer.
The resistance measurement could be from more
than one mat wired in series, or wired in parallel.
Either will provide false resistance readings.
Make sure resistance measurements are for only one mat at a time.
The multi-meter may be set to the wrong scale.
The multi-meter should typically be set to the 200 ohms (200Ω) scale. For mats with resistance range
higher than 200 ohms on the nameplate label, set the meter to the 2000 ohm (2kΩ) scale.
Floor is not getting warm.
Mat has been damaged.
Measure mat resistance. Check for both “open circuit” and “short circuit” as detailed earlier in this manual.
If damaged, record resistances between all wires and contact the manufacturer.
GFCI has tripped, indicated by a light or “GFCI
TRIP” on the control.
Check for loose wire connections. Reset the GFCI on the control or circuit breaker. If it trips again, check
for a short circuit in the mat as detailed earlier in this manual. If mat is damaged, record resistance
between all wires and contact the manufacturer. If mat is not damaged, replace the GFCI control. Also
see “GFCI conflicts” below.
Incorrect voltage supplied, or mismatched
electrical components used.
Measure “line” voltage, then measure “load” voltage. 120 VAC mats have black and white power leads.
240 VAC mats have black and blue power leads.
Uninsulated concrete slab floor.
Surface temperatures rise slowly an uninsulated slab and heat is lost to the ground below.. If, after 5 to 8
hours of heating, the floor is not warmer to the touch, check for mat damage (see “Mat has been dam-
aged” above). A clamp-on ampmeter may be used to verify the amps are correct to each mat.
Mats are wired in “series” or “daisy chained”
(end-to-end).
Multiple mats must be connected in “parallel” (or black-to-black, white-to-white).
Floor heats continuously.
Incorrect wiring. The control was “bypassed”
when it was wired to the power supply.
Make sure wiring connections are correct. Consult the wiring diagram on the back of the control the
instructions that came with the control, or the wiring diagram in this manual.,
Defective control.
Return control to dealer for replacement.
Floor temperature shows “HI”
or may show temperature
over 100°F.
Floor sensor is not wired properly, or is
located incorrectly.
Make sure only one floor sensor is connected to the control.
Control is not working correctly.
If a programmable control, the programming may
be incorrect.
Carefully read and follow control programming instructions.
Incorrect voltage supplied, or mismatched
components used.
Test voltage, verify parts. See “Incorrect voltage supplied” above.
Floor sensor is not wired properly, or is not
working properly.
Make sure only one floor sensor is connected to the control. Also see “Sensor is loose or
broken” above.
Loose connection(s) on line side and/or load side
of control.
Remove and reinstall the wire nuts at each connection. Make sure the wire nuts are tight.
Check all connections back to the breaker.
Defective control.
Return control to dealer for replacement.
Control is not working at all.
No power is supplied.
Check circuit breaker. Measure voltage at the control. Check all connections between breaker
and control.
Defective control.
Return control to dealer for replacement.
GFCI conflicts and false-trips
An electric motor or a ballasted light source is
sharing the circuit with the mat.
Electric motors and other electrical devices can cause a GFCI to false-trip. Run a dedicated circuit
to the floor-warming system or select a different branch circuit..