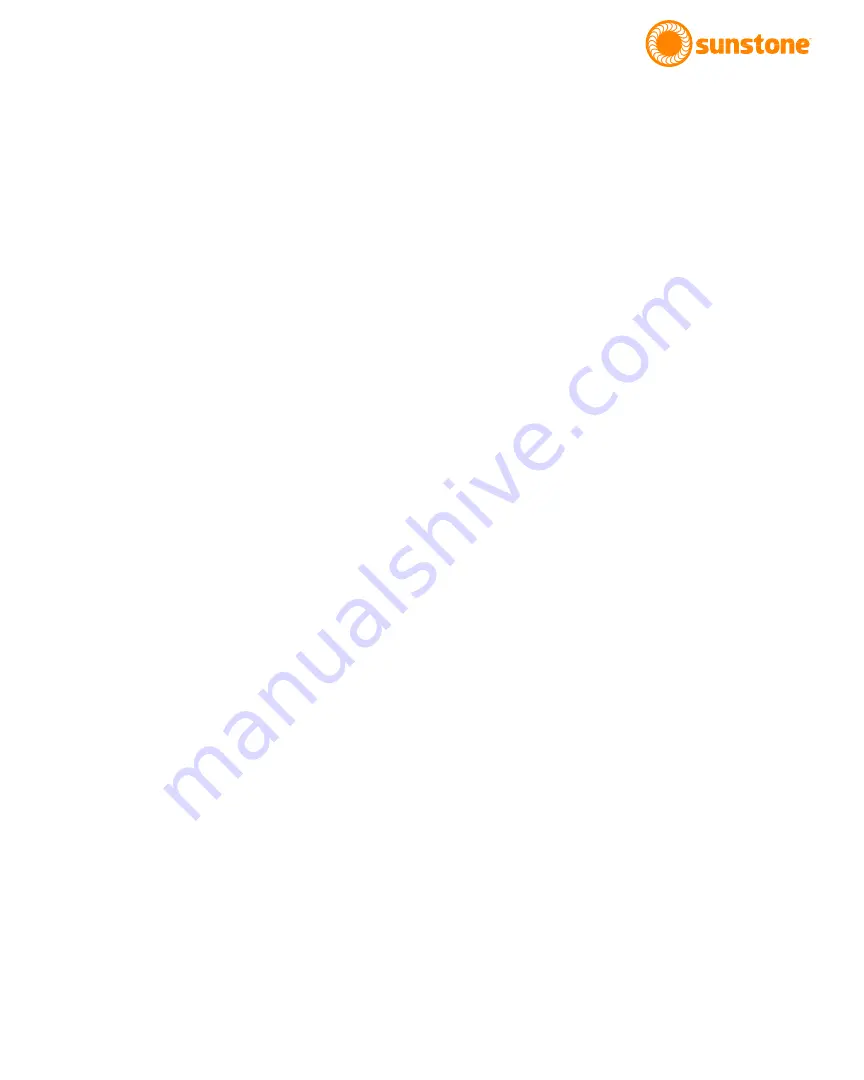
Questions? Call or Text +1-801-658-0015 •
3
The Micro Welder Experts
Bulk Resistance
Once all the bridges have fused, the contact resistance nears zero. At this point the second phase of the
melting process begins and the bulk resistance of the materials plays the final role in weld formation. The “Bulk
Resistance” is the inherent resistive nature of the material and varies depending on the type of material. As
conductivity increases, resistivity decreases. Conductive metals such as copper require much larger amounts
of energy to form a weld compared to more resistive materials such as steel.
What is Thermocompression Welding?
Thermocompression welds utilize the resistive nature of the electrode material to generate the heat for fusion
instead of relying on the resistive nature of the materials being welded. Thermocompression electrodes (gener
-
ally made of tungsten) are specially designed to be fused at the very tip. As current is passed through the resis
-
tive tip of the electrode, heat is generated. Constant contact between the electrode and material being welded
must be maintained with the correct amount of compressive force to create fusion with the substrate material.
Welding Tips and Recommendations
Remember that every weld application is different. Several factors must work together and be balanced to
achieve successful welds. Sometimes experimentation and tweaking is required to get just the right weld. As
previously discussed, the resistivity of the materials and contact resistance play a major role. Other important
factors include the force being applied, the weld discharge energy, the weld discharge length, and the elec-
trodes being used.
WELD FORCE
Since contact resistance plays such an important role in the weld process, the weld force being applied by the
electrodes is critical. The larger the contact resistance, the hotter the resultant weld.
As more force is applied, the contact resistance is reduced due to an increased number of contact points be-
tween the two surfaces at the weld spot (more contact points result in lower contact resistance). More contact
points results in a cooler weld.
Conversely, too little force can lead to arcing between the two surfaces, which causes undesirable weld results.
Too much force can lead to weaker welds and part deformation.
Note: Weld force, as specifically described above, applies to resistance welding only. Thermocompression
welds are not affected by contact resistance and therefore lighter forces do not lead to increased weld heat.
In fact, higher forces are sometimes necessary to create good contact fusion (hence the term “compression”
used in the name).
WELD ENERGY
The weld energy is adjusted using the welding power supply. Sunstone recommends that you first try a weld at
a low energy setting and then increase energy until the desired hold strength is achieved. This tactic helps pre
-
vent destroying the workpiece by having too much energy to start out. With thermocompression welds, when
set too high, energy settings can even lead to electrode tip degradation/failure.
Summary of Contents for PicoDC
Page 1: ...Direct Current Resistance Welder Users Guide 20210615 PART 1230 Pic...
Page 4: ...Users Guide Pic...
Page 41: ...Questions Call or Text 1 801 658 0015 37 The Micro Welder Experts...
Page 42: ...38 Questions Call or Text 1 801 658 0015 Users Guide Pic...
Page 43: ...Questions Call or Text 1 801 658 0015 39 The Micro Welder Experts...