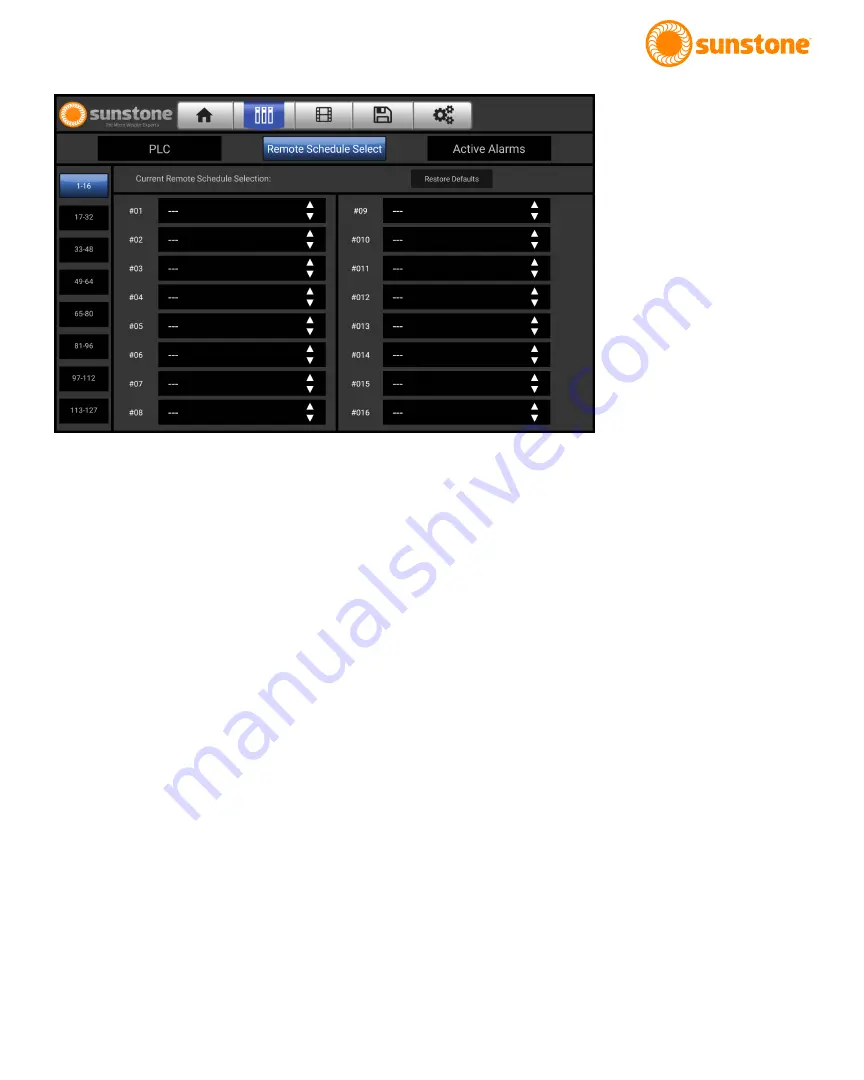
Questions? Call or Text +1-801-658-0015 •
29
The Micro Welder Experts
REMOTE SCHEDULE SELECT
The Sunstone PA250i contains an advanced Remote Schedule Select Screen (see Figure 29.1), allowing you to
assign up to 127 saved welds, and remotely select which one to use. Welds must be saved before they can be
assigned on this screen (see the Save/Load Screen section on page 32 for more information on saving welds).
Assigning Saved Welds
The 127 available slots are broken up into 7 groups of 16, and 1 group of 15. Use the buttons on the left of the
screen to select the various ranges of remote schedules, and the numbered drop downs to the right to select
what saved weld name is assigned to that number.
Selecting Assigned Weld Schedules
Pins 1.2 through 1.8 (refer to the Connector Pinout on page 27 for more information on pin locations) are all
used for Remote Schedule Select. Like the PLC inputs, they too operate in active-low configurations, where a
low value (0V) is used for selecting. These pins also have an internal limiting pull up resister to limit current.
These seven pins are bit mapped into a number between 0 and 127, with RSS 6 (pin 1.8) being the most sig-
nificant bit. The bit-mapped number will then load the corresponding Remote Schedule Select (RSS) slot. For
example, if RSS0 (pin 1.2) and RSS1 (pin 1.3) are driven low while the rest remain high, read in as a number
1111100, because the unit operates in an active-low configuration, and is therefore interpreted by the unit to be
0b0000011, or slot number 3. If the RSS tries selecting a slot that does not have a weld assigned, the following
message will appear: “Error: Invalid Remote Schedule Selection”.
When the RSS loads any numbered slot, the user interface (or UI) is locked, preventing you from changing set-
tings away from what the RSS loaded. If no pins are being driven low, the RSS is disabled, and the UI is unlocked
so settings can be changed.
Figure 29.1. The Remote Schedule
Select Screen allows you to save
up to 127 different welds and select
any one of them remotely.