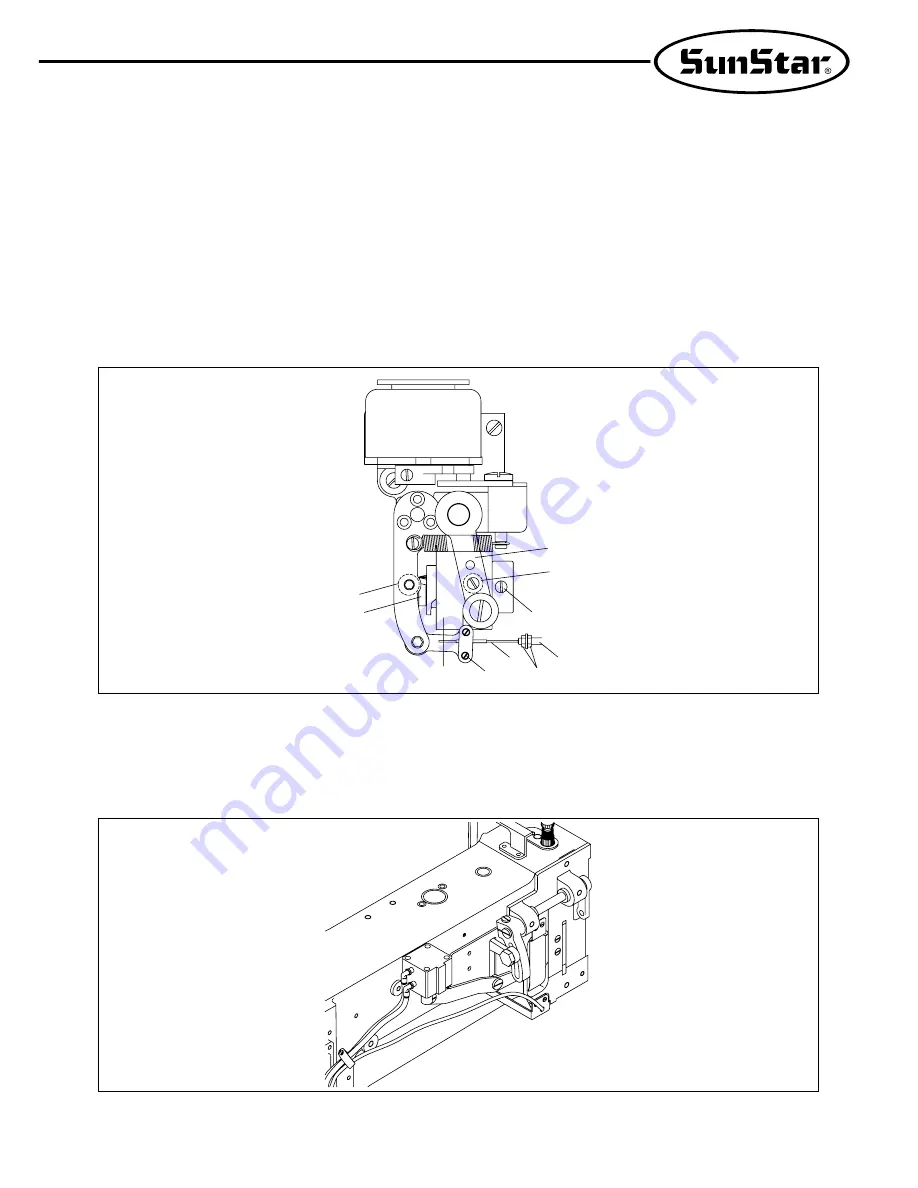
25
16) Adjustment of Thread Release
(1) Turn the pulley by hand to place the needle bar at the lowest position.
(2) Press the trimmer driving link
①
to insert the trimmer cam roller
②
into the groove of the trimmer cam
③
.
(3) Turn the pulley by hand to place the thread take-up lever at the highest position. Loosen the tightening screw
④
and adjust
the thread release collar
⑤
to make the thread tension dish closed when the thread take-up lever is located at the highest
position. When adjustment completes, fasten the screw.
(4) The tension thread opening is adjusted by the thread release roller
⑥
, which is installed at the protruded part of the thread
release collar
⑤
. Loosen the screw
⑦
. Fasten the screw after tightening the thread release cable
⑧
.
(5) Loosen the nut
⑨
to make the fine adjustment. When the cable cap
⑩
is moved to the right side, the opening will become
bigger.
[Figure 41]
17) Installation of Automatic Lap Lifting Device (optional)
(1) First of all, remove the manual lap lifting device before installing the automatic lap lifting device (see figure).
Loosen the screw to remove the installed parts. Then install the automatic lap lifting device as in Figure 42.
Connect the two pneumatic tubes in order as in the figure, and tie the tubes with other lead lines with band clips.
[Figure 42]
①
②
④
⑩
⑨
⑧
⑦
⑥
⑤
③
Summary of Contents for KM-570BL
Page 29: ...29 5 Table Drawing ...