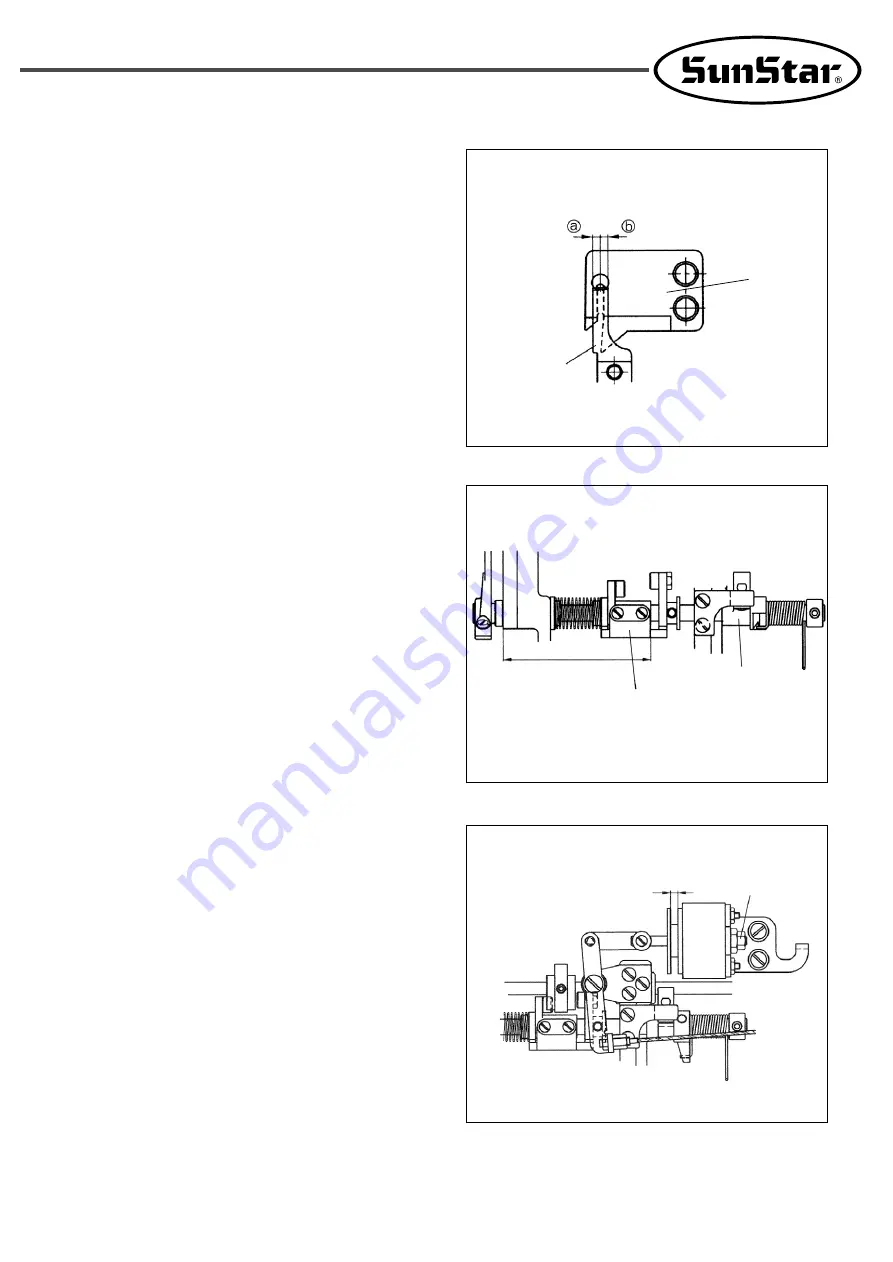
31
B. Adjusting fixing blade and movable knife
a) Like in Figure 8-14, the standard position is where
the cut part of the movable knife is aligned with the
center of the fixed blade.
b) When part
ⓐ
becomes bigger in Figure 8-14, three
pieces of threads are to be produced, causing the
thread missing after the trimming. If part
ⓑ
becomes
bigger, it can cause a trimming miss. So be cautious
in adjusting the right position.
[Fig. 8-14]
[Fig. 8-15]
[Fig. 8-16]
C. Adjusting the trimmer driving part
a) The standard assembly position is shown in Figure 8-15.
b) Fix the thread trimming following crank to the
trimming shaft as shown in the figure.
c) Fix the stopper lever to the bed so that the lever can
smoothly rotate in a range where the gap of the
trimming shaft does not occur.
D. Adjusting the thread trimmer solenoid
a) Working amount of the thread trimming solenoid
①
The standard working amount of the thread
trimming solenoid is 4.6mm as shown in
Figure 8-16.
②
Use the thread trimming solenoid stopper nut to
control the working amount.
movabl
e knife
fixed
blade
thread trimming cam following crank
stopper lever
4.6mm
stopper nut
91.2mm
Summary of Contents for KM-1640BL-7
Page 2: ......