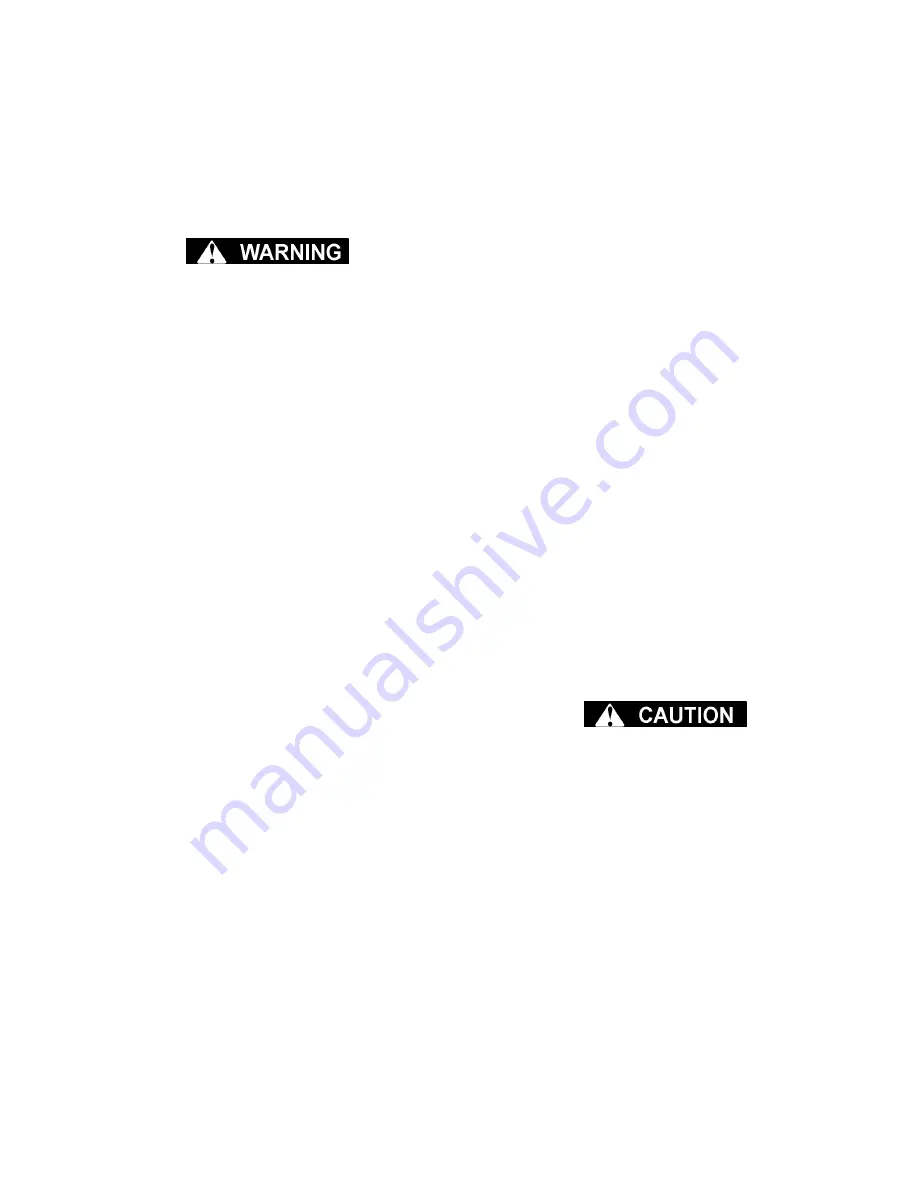
Section 6
MAINTENANCE
35
6.1 MAINTENANCE INTRODUCTION
The Supervisor II monitors the status of the air filter,
fluid filter, and separator elements. When mainte-
nance to these devices is required, the Supervisor
II will display the appropriate maintenance mes-
sage and flash the location LED on the graphics
map as a visual reminder.
DO NOT remove caps, plugs, and/or other compo-
nents when compressor is running or pressur-
ized.
Stop compressor and relieve all internal pressure
before doing so.
6.2 DAILY OPERATION
Following a routine start, observe the various
Supervisor II displays to check that normal readings
are being made - previous records are very helpful
in determining the normalcy of the measurements.
These observations should be made during all
expected modes of operation (i.e. full load, no-load,
different line pressures, cooling water tempera-
tures, etc.).
During the initial start-up or servicing of the pack-
age, fluid may have to be added to the sump ves-
sel to restore an adequate level. Frequent fluid
additions to maintain said level would be indicative
of excessive fluid consumption, and should be
investigated - see the Troubleshooting Section of
this manual for probable cause and remedy.
6.3 MAINTENANCE AFTER INITIAL 50 HOURS OF
OPERATION
After the initial 50 hours of operation, a few mainte-
nance requirements are needed to rid the system of
any foreign materials which may have accumulated
during compressor assembly. Perform the following
maintenance operations to prevent unnecessary
problems.
1. Clean the return line strainers.
2. Clean the return line orifices.
3. Change the fluid filter elements.
4. Clean the control line filters.
6.4 MAINTENANCE AS REQUIRED BY LUBRICA-
TION GUIDE (SECTION 3)
1. Drain the sump and change the compressor fluid.
2. Replace the main fluid filter element.
3. Clean the return line strainers and orifices.
4. Clean or replace the control line filter element.
6.5 FLUID CHANGE
Standard models are filled with Sullube. Sullube
should be changed under the following conditions,
whichever occur first:
1. Every 1800 hours.
2. Once a year.
3. As indicated by fluid analysis.
A fluid sample at every 1000 hours is recommend-
ed. For a free Sullube analysis, send fluid to:
Dow Chemical
Lubricant Technology Center
Building B-1605
Freeport, TX 77541
To facilitate this, a sample bottle is included with the
compressor.
6.6 SEPARATOR MAINTENANCE
Replace the separator elements when the separa-
tor maintenance message is displayed or after one
(1) year, whichever comes first. The separator ele-
ments must be replaced.
DO NOT
clean the sepa-
rator elements.
6.7 PARTS REPLACEMENT AND ADJUSTMENT
PROCEDURES
FLUID FILTER MAINTENANCE
. The fluid filter (P/N 02250111-
592) is located schematically between the thermal
valve on the sump and the oil stop valve on the
compressor-mounting bracket. When servicing this
filter, shut the compressor down, make sure all
pressure has been released, then follow the
instructions below. For element replacement order
kit number 250031-850.
To minimize the possibility of filter element rup-
ture, it is important that ONLY replacement ele-
ments identified with the Sullair name, logo and
appropriate part numbers be used, and that sub-
stitute elements NOT be used, due to the fact that
such filters may have inadequate or questionable
working pressure ratings.
1. Unthread the filter canister from the head. A hex
nut is supplied on the bottom of the canister
along with the bottom portion of the canister has
a rough textured surface. Either can be used to
assist in removal of the canister.
2. Pull the canister away from the filter head. The
filter elements will be attached to the filter head.
3. Separate the element from the filter head.
4. Remove the canister seal.
5. Thoroughly clean the filter head and canister in
solvent.
Summary of Contents for LS20TS
Page 6: ......
Page 20: ...Section 2 DESCRIPTION 14 Figure 2 4A Control System Diagram Functional Components ...
Page 21: ...Section 2 DESCRIPTION 15 Figure 2 4B Control System Diagram START ...
Page 22: ...Section 2 DESCRIPTION 16 Figure 2 4C Control System Diagram MODULATION ...
Page 23: ...Section 2 DESCRIPTION 17 Figure 2 4D Control System Diagram FULL LOAD ...
Page 24: ...Section 2 DESCRIPTION 18 Figure 2 4E Control System Diagram UNLOAD ...
Page 40: ...NOTES 34 ...
Page 50: ...NOTES 44 ...
Page 53: ...NOTES 47 ...
Page 56: ...Section 8 ILLUSTRATIONS AND PARTS LIST 50 02250135 237R01 8 4 AIR INLET SYSTEM ...
Page 58: ...Section 8 ILLUSTRATIONS AND PARTS LIST 52 02250135 237R01 8 4 AIR INLET SYSTEM ...
Page 72: ...Section 8 ILLUSTRATIONS AND PARTS LIST 66 02250138 950R01 8 9 DISCHARGE SYSTEM ...
Page 74: ...Section 8 ILLUSTRATIONS AND PARTS LIST 68 02250138 950R01 8 9 DISCHARGE SYSTEM ...
Page 76: ...Section 8 ILLUSTRATIONS AND PARTS LIST 70 02250138 950R01 8 9 DISCHARGE SYSTEM ...
Page 78: ...Section 8 ILLUSTRATIONS AND PARTS LIST 72 02250139 578R00 8 10 CONTROL START SYSTEM ...
Page 80: ...Section 8 ILLUSTRATIONS AND PARTS LIST 74 02250139 578R00 8 10 CONTROL START SYSTEM ...
Page 82: ...Section 8 ILLUSTRATIONS AND PARTS LIST 76 02250137 724R02 8 11 CONTROL PANEL ...
Page 84: ...Section 8 ILLUSTRATIONS AND PARTS LIST 78 8 12 ENCLOSURE AND ENCLOSURE DECALS ...
Page 86: ...Section 8 ILLUSTRATIONS AND PARTS LIST 80 8 13 DECAL GROUP ...
Page 88: ...Section 8 ILLUSTRATIONS AND PARTS LIST 82 8 13 DECAL GROUP ...
Page 90: ...Section 8 ILLUSTRATIONS AND PARTS LIST 84 8 13 DECAL GROUP ...
Page 92: ...Section 8 ILLUSTRATIONS AND PARTS LIST 86 8 14 DECAL LOCATIONS OPEN WATER COOLED ...
Page 94: ...Section 8 ILLUSTRATIONS AND PARTS LIST 88 8 15 DECAL LOCATIONS CONTROL BOX ...
Page 97: ...NOTES 91 ...