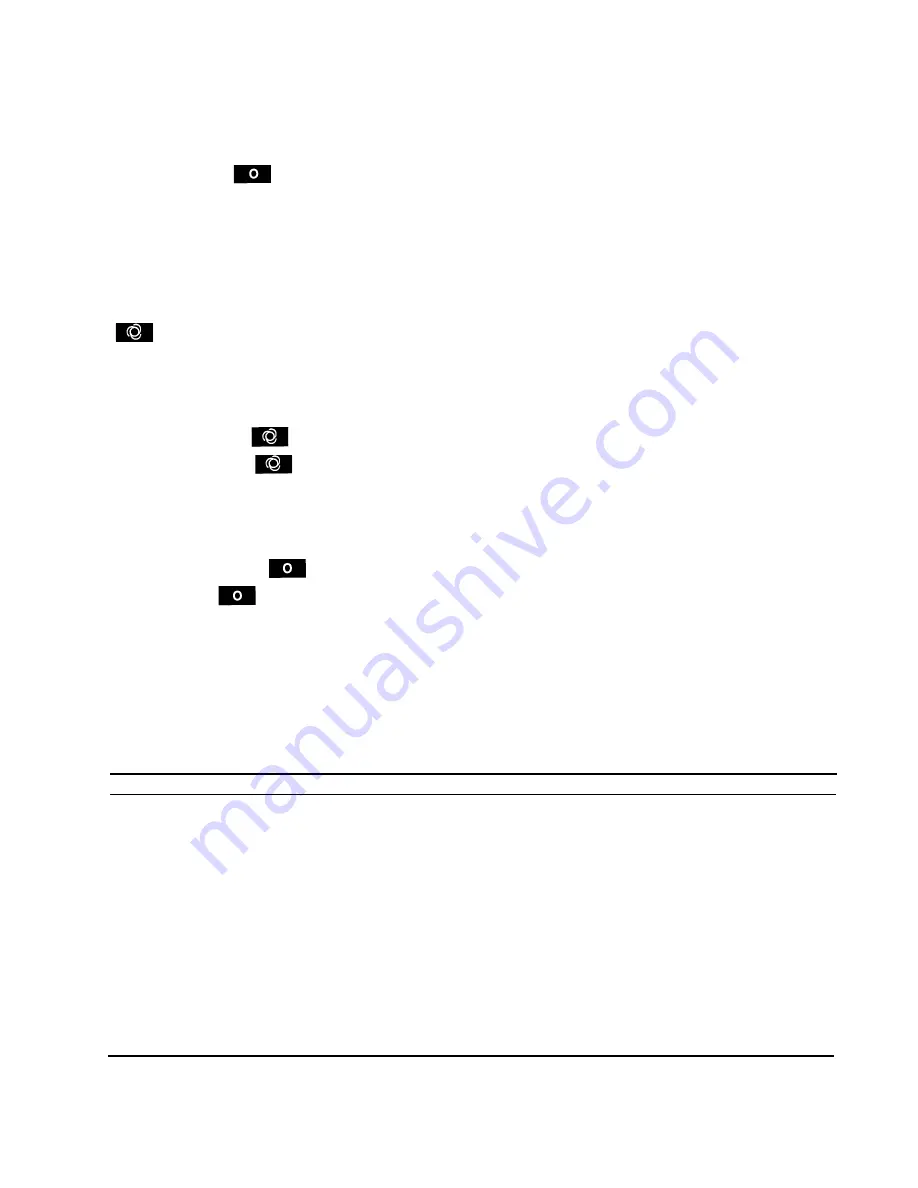
Section 5
OPERATION
36
common fault relay will be turned off, if engaged,
and it will try to clear the alarm and maintenance
indicators. Regardless of what the compressor is
doing, pressing “
” puts the Supervisor in
manual stop mode.
AUTOMATIC OPERATION MODE
In this mode the compressor will start if line pres-
sure (P2) is less than the
LOAD
parameter. It will
stop if the compressor runs unloaded for the num-
ber of minutes indicated by the
UNLD TIM
parame-
ter . To put the compressor in automatic mode press
“
”. If P2 is already less than
LOAD
the com-
pressor will start immediately, otherwise the system
status will indicate
STANDBY
and the LED marked
AUTO
will flash.
If the compressor is already running, but in continu-
ous mode, pressing “
” will switch operation to
automatic. Pressing “
” while already running
in automatic mode will cause the Supervisor to turn
off the common fault relay, if engaged, and clear
any maintenance indicators.
In automatic mode the compressor can be stopped
manually by pressing “
”. Stopping the com-
pressor using “
” will put the Supervisor in
manual stop mode.
Regardless of whether in “automatic” or “manual”
mode, control of the load solenoid will be based on
the parameters
UNLD
and
LOAD
. This operation is
as follows:
P2 > UNLD —> load solenoid turned off
P2 < LOAD —> load solenoid turned on
POWER FAILURE RESTART
If the restart timer (RST TIME parameter) is dis-
abled the compressor will not try to start after a
power up. If this time is set to a value the machine
will go into standby after power up. When the line
pressure drops below the load setpoint, the restart
timer will start timing. When the timer expires the
machine will start.
SEQUENCING MODES
The following is a brief description of sequencing
modes, for details see the Supervisor Sequencing
& Protocol Manual (P/N 02250139-197).
• DISABLED
- Responds to status and
parameter change messages via the RS485
network but will not respond to start, stop,
load or unload messages.
• REMOTE
- Responds to status and param-
eter change messages but will not respond
to start, stop, load or unload messages. The
remote inputs and outputs are enabled
(start/stop, load/unload, master/local).
• SLAVE
- Will respond to all messages, but
will not start or load unless commanded to
do so by a message. This mode is used to
control the machine from a master comput-
er.
• HOURS
- Sends status message about
once a second, starts, loads and unloads
machines based on sequencing hours.
• COM ID #
- Sends status message about
once a second, starts, loads and unloads
machines based on machine Com ID#.
RUN RELAY (K1)
*-DELTA (K2)
UNLOAD/LOAD (K3)
COMMON FAULT (K4)
DRAIN VALVE (K5)
FULL LOAD/MODULATE (K6)
Contact closure energizes the compressor starter.
A timed contact used to provide wye-delta transition time.
Controls ON LOAD/OFF LOAD operator of the load control
solenoid valve.
May be used to provide remote indication of any pre-alarm,
maintenance or fault shutdown condition.
Controls a solenoid valve to provide automatic condensate
removal.
Used with sequencing feature.
NOTE: All output relays will handle 8 amperes at 120/240 VAC.
5.5 SUPERVISOR II OUTPUT RELAYS
RELAY
OPERATION
Summary of Contents for LS16T
Page 6: ......
Page 23: ...Section 2 DESCRIPTION 17 Figure 2 4A Control System Diagram Functional Components...
Page 24: ...Section 2 DESCRIPTION 18 Figure 2 4B Control System Diagram START...
Page 25: ...Section 2 DESCRIPTION 19 Figure 2 4C Control System Diagram MODULATION...
Page 26: ...Section 2 DESCRIPTION 20 Figure 2 4D Control System Diagram FULL LOAD...
Page 27: ...Section 2 DESCRIPTION 21 Figure 2 4E Control System Diagram UNLOAD...
Page 32: ...NOTES 26...
Page 35: ...Section 3 SPECIFICATIONS 29 Figure 3 2 Identification LS16T 100 125 Air cooled 02250138 172R01...
Page 36: ...Section 3 SPECIFICATIONS 30 Figure 3 3 Identification LS16T 150 200 Air cooled 02250134 200R02...
Page 44: ...NOTES 38...
Page 54: ...NOTES 48...
Page 57: ...NOTES 51...
Page 62: ...Section 8 ILLUSTRATIONS AND PARTS LIST 56 02250134 187R00 8 5 AIR INLET SYSTEM...
Page 72: ...Section 8 ILLUSTRATIONS AND PARTS LIST 66 02250134 191R00 8 9 AIR PIPING SYTEM 150 200HP...
Page 74: ...Section 8 ILLUSTRATIONS AND PARTS LIST 68 02250134 191R00 8 9 AIR PIPING SYTEM 150 200HP...
Page 76: ...Section 8 ILLUSTRATIONS AND PARTS LIST 70 02250138 175R01 8 10 FLUID PIPING SYSTEM 100 125HP...
Page 80: ...Section 8 ILLUSTRATIONS AND PARTS LIST 74 02250134 197R00 8 12 DISCHARGE SYSTEM...
Page 82: ...Section 8 ILLUSTRATIONS AND PARTS LIST 76 02250134 197R00 8 12 DISCHARGE SYSTEM...
Page 84: ...Section 8 ILLUSTRATIONS AND PARTS LIST 78 02250134 197R00 8 12 DISCHARGE SYSTEM...
Page 86: ...Section 8 ILLUSTRATIONS AND PARTS LIST 80 02250134 196R00 8 13 CONTROL START SYSTEM...
Page 88: ...Section 8 ILLUSTRATIONS AND PARTS LIST 82 02250134 196R00 8 13 CONTROL START SYSTEM...
Page 90: ...Section 8 ILLUSTRATIONS AND PARTS LIST 84 02250137 724R02 8 14 CONTROL PANEL...
Page 92: ...Section 8 ILLUSTRATIONS AND PARTS LIST 86 02250138 176R00 8 15 ENCLOSURE 100 125HP...
Page 94: ...Section 8 ILLUSTRATIONS AND PARTS LIST 88 02250134 193R00 8 16 ENCLOSURE 150 200HP...
Page 96: ...Section 8 ILLUSTRATIONS AND PARTS LIST 90 8 17 DECAL GROUP...
Page 98: ...Section 8 ILLUSTRATIONS AND PARTS LIST 92 8 17 DECAL GROUP...
Page 100: ...Section 8 ILLUSTRATIONS AND PARTS LIST 94 8 17 DECAL GROUP...
Page 102: ...Section 8 ILLUSTRATIONS AND PARTS LIST 96 8 18 DECAL LOCATIONS OPEN AIR COOLED...
Page 104: ...Section 8 ILLUSTRATIONS AND PARTS LIST 98 8 19 ENCLOSURE DECALS...
Page 106: ...Section 8 ILLUSTRATIONS AND PARTS LIST 100 8 20 DECAL LOCATIONS CONTROL BOX...
Page 110: ...NOTES 104...
Page 111: ......