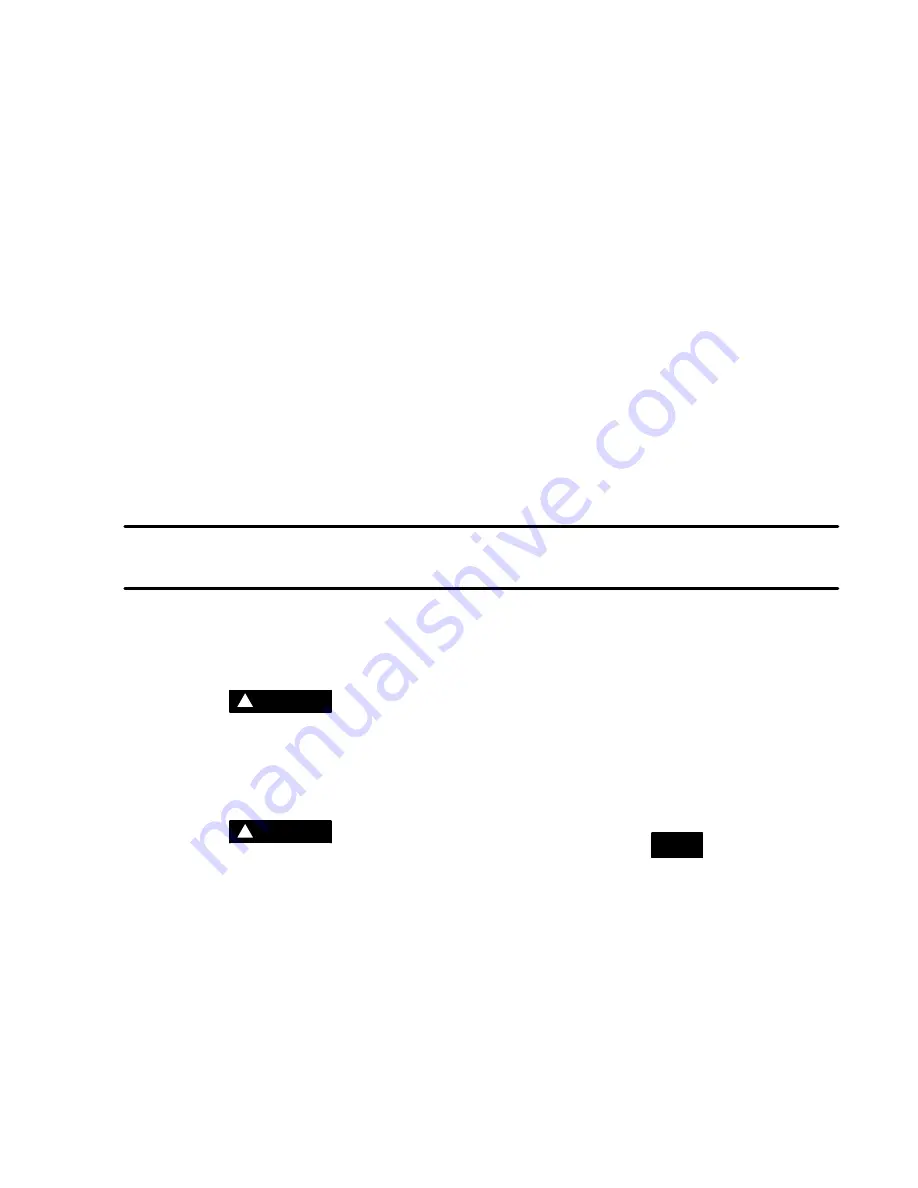
Section 3
SPECIFICATIONS
14
COMPRESSOR:
STANDARD MODELS
Type:
Rotary Screw
Standard Operating Pressure
(IV):
100 psig (6.9bar) (L)
140 psig (9.7 bar) (HH)
115 psig (7.9bar) (H) (XH)
175 psig (12 bar) (XH)
Bearing Type:
Anti---Friction
Ambient Temperature (Max.)
(V):
105
_
F (41
_
C)
Cooling:
Pressurized Fluid
Compressor Fluid:
Sullair Sullube 32
Sump Capacity:
3.5 U.S. gallons (14.8 liters)
Control:
Electro---Pneumatic
Supervisor
II
(optional)
MOTOR
(VI)
:
STANDARD MODELS
Size:
25, 30 and 40HP
Type:
C---Flanged, Open Dripproof, Premium Efficiency
Three Phase, 230/460 60 Hz, 380/415 50 Hz
40
_
C Maximum Ambient Temperature
Options Available: 200V and 575V
T.E.F.C. Also Available: IP54
Starter:
Full Voltage Magnetic or Wye Delta
Options Available: 200V and 575V
Speed:
60 Hz: 1770 RPM
50 Hz: 1475 RPM
40HP: 3000 RPM
(IV)
Special compressors are available for operation at higher pressures.
(V)
Special compressors are available for operation in higher ambient temperature.
(VI)
Multi--frequency and voltage motors are used. The compressors must be used only with the specified electrical frequency and voltage.
3.2 LUBRICATION GUIDE
For best value and longest uninterrupted ser-
vice, the LS---10 Series compressors are factory
filled and tested with a long life lubricant.
WARNING
!
Mixing of other lubricants within the compres-
sor unit will void all warranties!
If, due to availability or other reasons, other fluids
are required, follow Lubrication Guide 3.4 below.
WARNING
!
“The Plastic Pipe Institute recommends
against the use of thermoplastic pipe to trans-
port compressed air or other compressed
gases in exposed above ground locations, e.g.
in exposed plant piping.”
(I)
Sullube 32 should not be used with PVC piping
systems. It may affect the bond at cemented
joints. Certain other plastic materials may also
be affected.
(I)
Plastic Pipe Institute, Recommendation B,
Adopted January 19, 1972.
Maintenance of all other components is still rec-
ommended as indicated in the Operator’s
Manual.
For light---duty high---humidity service where
condensed moisture and emulsification (may-
onnaise) may occur, the fluid change interval
must be reduced to 300 hours maximum. A
non---detergent fluid with rust, oxidation and
foam inhibitors and good water separation char-
acteristics should be used.
DO NOT MIX DIFFERENT TYPES OF FLUIDS.
Contamination of non---detergent mineral fluids
with traces of detergent motor fluids may lead to
operational problems such as foaming, filter
plugging, orifice or line plugging.
NOTE
Flush system when switching lubricant
brands.
When ambient conditions exceed those noted
or if conditions warrant use of “extended” life lu-
bricants contact Sullair for recommendation.
3.3 APPLICATION GUIDE
Sullair encourages the user to participate in a
fluid analysis program with the fluid suppliers.
This could result in a fluid change interval differ-
ing from that stated in the manual. Contact your
Sullair dealer for details.
Summary of Contents for LS-10 18KW 24KT
Page 6: ...NOTES...
Page 15: ...Section 2 DESCRIPTION 9 Figure 2 3 Control System...
Page 18: ...12 NOTES...
Page 22: ...16 NOTES...
Page 26: ...20 NOTES...
Page 34: ...28 NOTES...
Page 38: ...32 NOTES...
Page 48: ...Section 7 MAINTENANCE 42 Figure 7 7 Piping and Instrumentation Diagram Standard...
Page 49: ...Section 7 MAINTENANCE 43 Figure 7 8 Piping and Instrumentation Diagram Supervisor II...
Page 50: ...44 NOTES...
Page 52: ...Section 8 ILLUSTRATIONS AND PARTS LIST 46 8 3 MOTOR COMPRESSOR FRAME AND PARTS...
Page 54: ...Section 8 ILLUSTRATIONS AND PARTS LIST 48 8 3 MOTOR COMPRESSOR FRAME AND PARTS...
Page 56: ...Section 8 ILLUSTRATIONS AND PARTS LIST 50 8 4 COOLER ASSEMBLY...
Page 58: ...Section 8 ILLUSTRATIONS AND PARTS LIST 52 8 5 AIR INLET SYSTEM...
Page 60: ...Section 8 ILLUSTRATIONS AND PARTS LIST 54 8 6 COOLING AND LUBRICATION SYSTEM...
Page 62: ...Section 8 ILLUSTRATIONS AND PARTS LIST 56 8 6 COOLING AND LUBRICATION SYSTEM...
Page 68: ...Section 8 ILLUSTRATIONS AND PARTS LIST 62 8 8 CONTROL SYSTEM AND ELECTRICAL PARTS...
Page 70: ...Section 8 ILLUSTRATIONS AND PARTS LIST 64 8 8 CONTROL SYSTEM AND ELECTRICAL PARTS...
Page 72: ...Section 8 ILLUSTRATIONS AND PARTS LIST 66 8 9 INSTRUMENT PANEL...
Page 76: ...Section 8 ILLUSTRATIONS AND PARTS LIST 70 8 11 DECAL GROUP 1 2 3 4 5 6 7 8 9 10 11...
Page 78: ...Section 8 ILLUSTRATIONS AND PARTS LIST 72 8 11 DECAL GROUP 12 13 14 15 16 17 18 19 20...
Page 80: ...Section 8 ILLUSTRATIONS AND PARTS LIST 74 8 11 DECAL GROUP 21 22 23 24 25 26 27...
Page 82: ...Section 8 ILLUSTRATIONS AND PARTS LIST 76 8 11 DECAL GROUP ADD FULL 29 28 30 31...
Page 88: ...NOTES...
Page 89: ...NOTES...