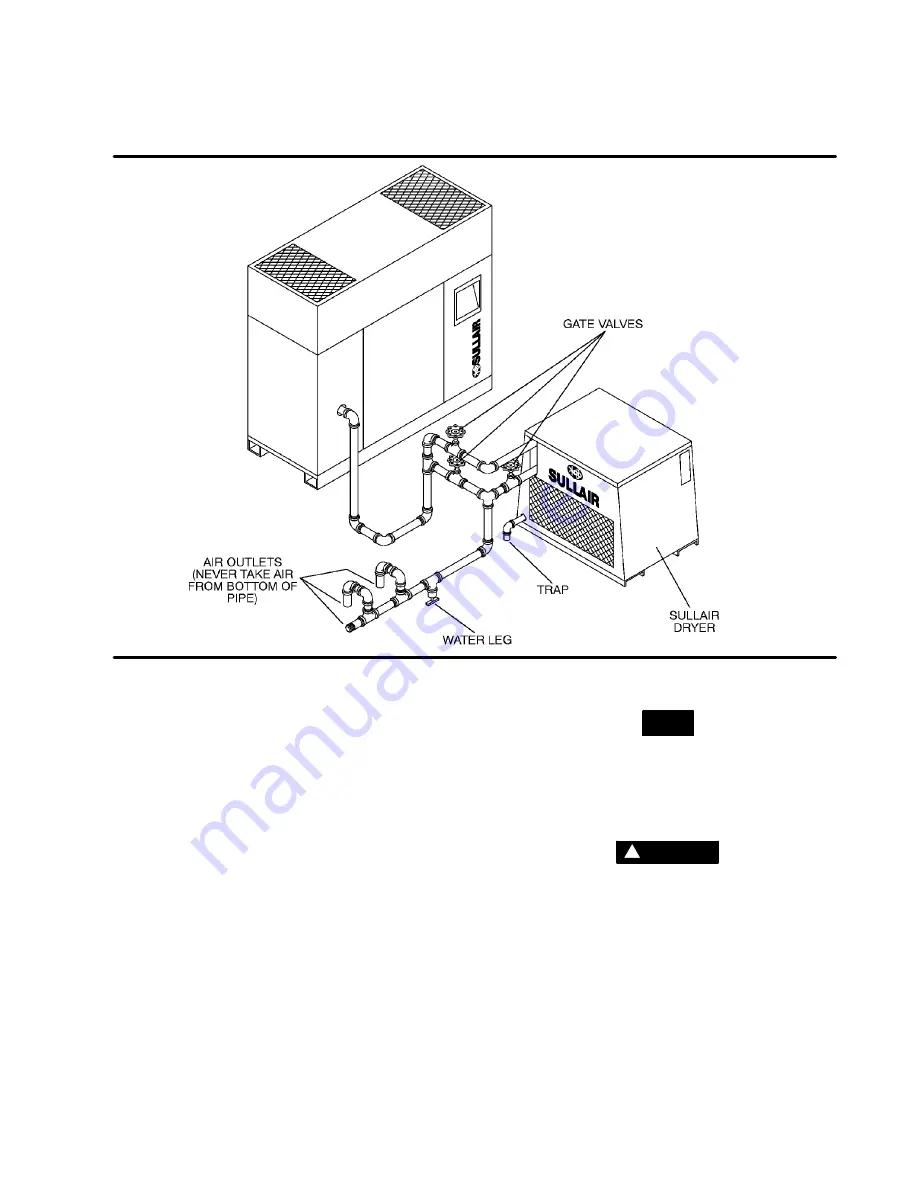
Section 4
INSTALLATION
18
Figure 4---1 Service Air Piping with Aftercooler and Optional Air Dryer (Typical)
4.4 COUPLING ALIGNMENT CHECK
No coupling alignment is required.
4.5 FLUID LEVEL CHECK
The air compressor is also supplied with the proper
amount of fluid. However, it is necessary to check
the fluid level at installation. The level is checked by
looking at the sight glass located near the sump. If
the sump is properly filled, fluid should be visible in
the sight glass. The maximum fluid level is the level
of the filler port.
4.6
ELECTRICAL
PREPARATION--STANDARD
ELECTRO/MECHANICAL
Interior electrical wiring is performed at the factory.
Required customer wiring is minimal, but should
be done by a qualified electrician in compliance
with OSHA, National Electrical Code, and/or any
other applicable State, Federal and local electrical
codes concerning isolation switches, fused dis-
connects, etc. Sullair provides a wiring diagram for
use by the installer.
NOTE
Customer must provide electrical supply power
disconnect within sight of machine.
A few electrical checks should be made to help as-
sure that the first start---up will be trouble---free.
WARNING
!
Lethal shock hazard inside. Disconnect all power
at source before opening or servicing.
1. Check incoming voltage. Be sure that compres-
sor is wired for the correct incoming voltage.
2. Check starter for correct size, proper overload
relay, and heaters.
3. Check all electrical connections for tightness.
4. “DRY RUN” the electrical controls by discon-
necting the three (3) motor leads from the start-
er. Energize the control circuits by turning the
“O/I” STOP/START
switch to
“I” START
and
check all protective devices to be sure that they
will de---energize the starter coil when tripped.
Summary of Contents for LS-10 18KW 24KT
Page 6: ...NOTES...
Page 15: ...Section 2 DESCRIPTION 9 Figure 2 3 Control System...
Page 18: ...12 NOTES...
Page 22: ...16 NOTES...
Page 26: ...20 NOTES...
Page 34: ...28 NOTES...
Page 38: ...32 NOTES...
Page 48: ...Section 7 MAINTENANCE 42 Figure 7 7 Piping and Instrumentation Diagram Standard...
Page 49: ...Section 7 MAINTENANCE 43 Figure 7 8 Piping and Instrumentation Diagram Supervisor II...
Page 50: ...44 NOTES...
Page 52: ...Section 8 ILLUSTRATIONS AND PARTS LIST 46 8 3 MOTOR COMPRESSOR FRAME AND PARTS...
Page 54: ...Section 8 ILLUSTRATIONS AND PARTS LIST 48 8 3 MOTOR COMPRESSOR FRAME AND PARTS...
Page 56: ...Section 8 ILLUSTRATIONS AND PARTS LIST 50 8 4 COOLER ASSEMBLY...
Page 58: ...Section 8 ILLUSTRATIONS AND PARTS LIST 52 8 5 AIR INLET SYSTEM...
Page 60: ...Section 8 ILLUSTRATIONS AND PARTS LIST 54 8 6 COOLING AND LUBRICATION SYSTEM...
Page 62: ...Section 8 ILLUSTRATIONS AND PARTS LIST 56 8 6 COOLING AND LUBRICATION SYSTEM...
Page 68: ...Section 8 ILLUSTRATIONS AND PARTS LIST 62 8 8 CONTROL SYSTEM AND ELECTRICAL PARTS...
Page 70: ...Section 8 ILLUSTRATIONS AND PARTS LIST 64 8 8 CONTROL SYSTEM AND ELECTRICAL PARTS...
Page 72: ...Section 8 ILLUSTRATIONS AND PARTS LIST 66 8 9 INSTRUMENT PANEL...
Page 76: ...Section 8 ILLUSTRATIONS AND PARTS LIST 70 8 11 DECAL GROUP 1 2 3 4 5 6 7 8 9 10 11...
Page 78: ...Section 8 ILLUSTRATIONS AND PARTS LIST 72 8 11 DECAL GROUP 12 13 14 15 16 17 18 19 20...
Page 80: ...Section 8 ILLUSTRATIONS AND PARTS LIST 74 8 11 DECAL GROUP 21 22 23 24 25 26 27...
Page 82: ...Section 8 ILLUSTRATIONS AND PARTS LIST 76 8 11 DECAL GROUP ADD FULL 29 28 30 31...
Page 88: ...NOTES...
Page 89: ...NOTES...