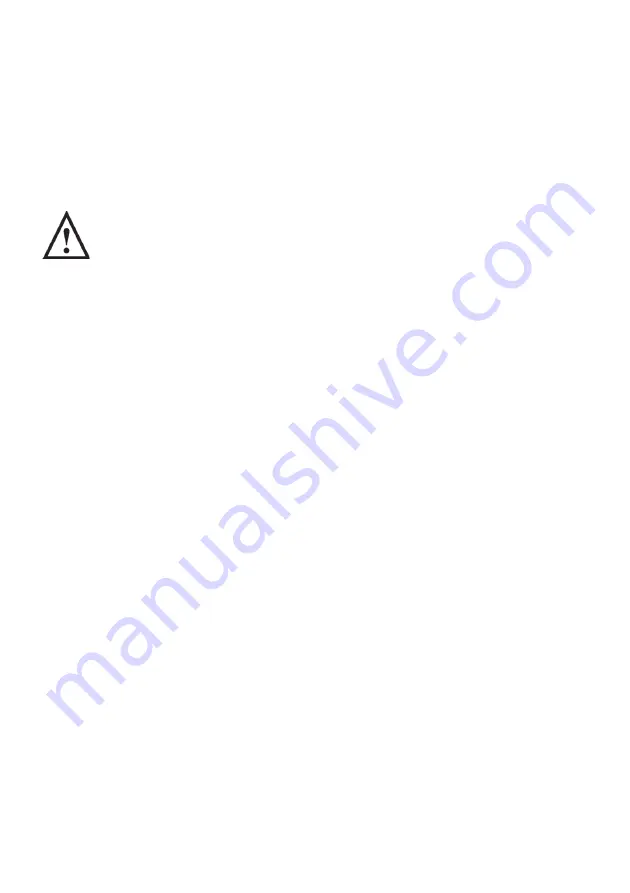
26
10.2
Water Scale
As water is heated scale deposits are released in areas of hard water, scale can
cause the mechanical seal to stick if left without use for long periods. The pump
must be run for at least 5 minutes every four weeks to “exercise” all working parts.
Run on cool water. See Section 11 – Technical Specification for note on water
temperature. This particularly applies to guest bathrooms used infrequently.
10.3
Cleaners, Disinfectants and Descalents
Acid based descalents and aggressive cleaning agents must not come into
contact with the pump. The pump must be removed from the system prior
to the use of these products. The system should be flushed to remove all
chemicals before the pump is re-connected.
If in any doubt as to the suitability of the chemical solutions, please contact
our TechAssist helpline on +44 (0) 800 31 969 80.
No other routine maintenance is required.