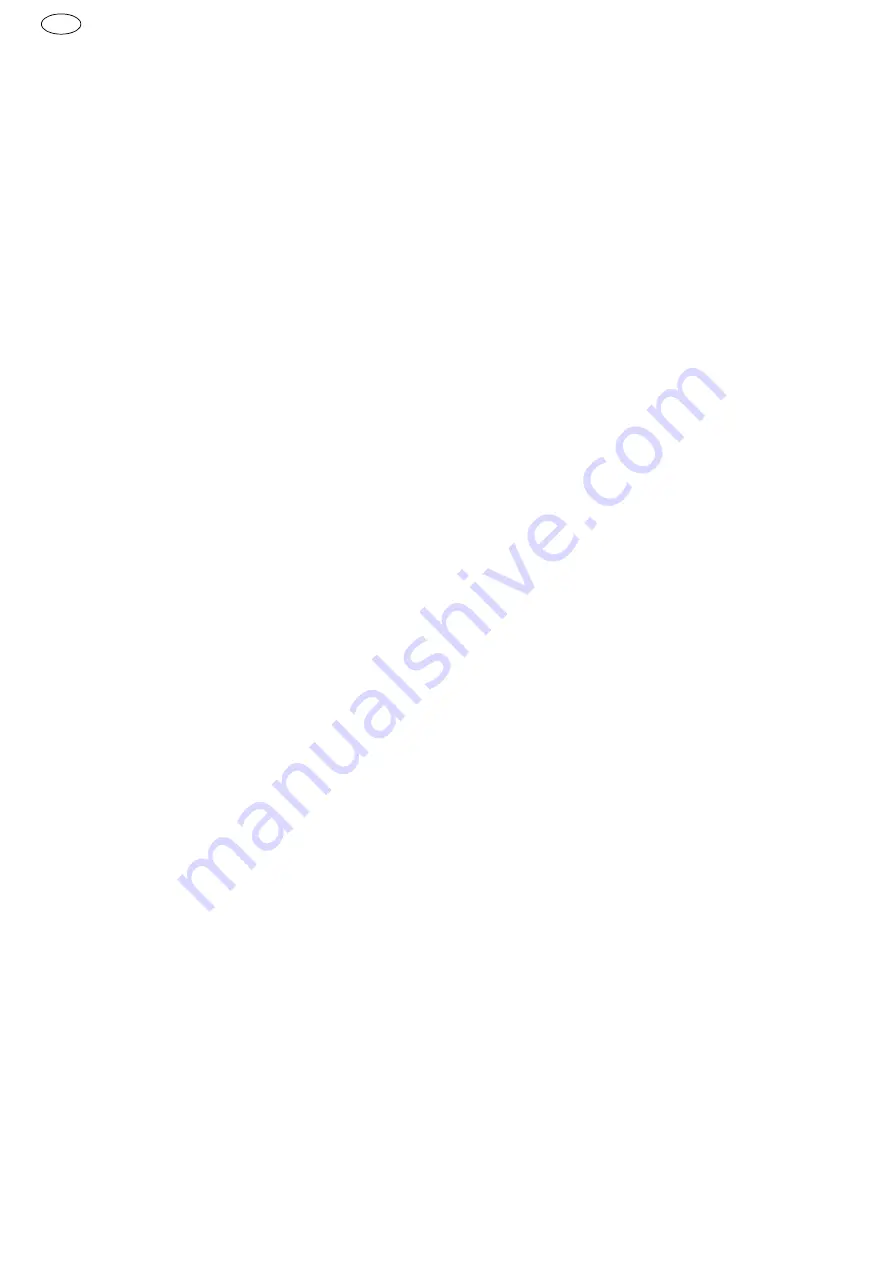
I/4
CPM 400-10-20 W
GB
1.6 Maintenance
1.6.1 Cleaning the intake filter
1. Unscrew the intake filter. (Fig. 5a)
2. Clean the filter insert using the blow gun,
exchange the filter insert if necessary.
3. Screw the intake filter back on.
1.7 Compressor inspections
This compressor is subject to a type approval
inspection. As a result, inspections by an au-
thorised expert prior to commissioning are
no longer necessary
. The prototype identi-
fication code is located on the compressor
specification plate.
We recommend that a "qualified person"
perform a pressure test on the vessel after
10 years, depending on general levels of
wear and tear.
A "qualified person" should be well informed
about Ordinance on Industrial Safety and
Health (formerly authorised expert)
Contact any of our approved service part-
ners. Most of our service partners have em-
ployees with expert qualifications.
L
The papers accompanying the vessel are
approval documents and must be kept
throughout the service life of the vessel.
These specifications only apply in Germa-
ny. Equivalent regulations apply in other
countries.
11 Safety valve
12 Pressure gauge (vessel pressure)
13 Pressure gauge (working pressure)
14 Electric motor
15 External protective motor switch
18 Filter pressure reducer
19 Quick-action coupling (clean, regu-
lated compressed air)
20 Mist oiler
21 Quick-action coupling (oil-mist com-
pressed air)
Summary of Contents for STROCOMP 400
Page 2: ......
Page 3: ......
Page 4: ......
Page 73: ...BAM CPM SUM UNM ZPM II 53 RUS 1 2 3 Schneider Druckluft GmbH 1 X X X X X X X X...
Page 78: ...II 58 BAM CPM SUM UNM ZPM RUS 8 2 7 2 2 8 X B X C X X X A X D X 2 4 4...
Page 79: ...BAM CPM SUM UNM ZPM II 59 RUS E X X X X 2 6 5 X X F X G X 2 6 11 X H X 2 6 5 X E I X X J X X X...