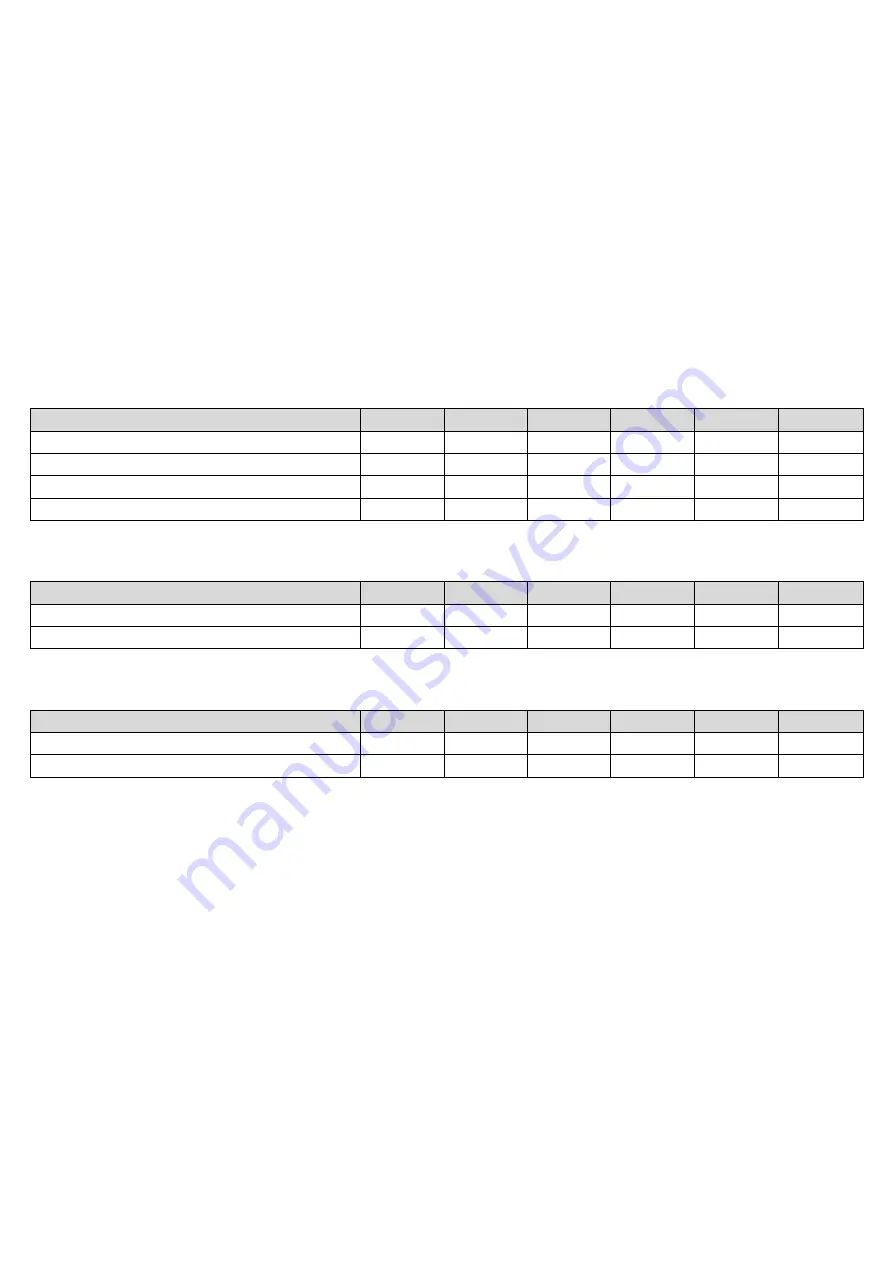
30
14 ELECTRICAL INSTALLATION
14.1
General
All S-ASX 30
– 50 air source heat pumps are shipped with all internal components within the casing factory wired up to
the main heat pump controller ready for the mains power supply to be connected.
The mains power supply cables must enter the heat pump through the holes on the lateral support and must be
connected to the power supply terminals of the unit.
•
For operation, the heat pump needs a power supply of 400 (+/- 10%) Vac, 3 phase & 50Hz.
•
Working on the heat pump should only be done by a qualified service engineer that is skilled in working on
electrical installations.
•
Electrical wiring should be installed according to all applicable standards and regulations.
14.2
Electrical Data
14.2.1
H
EAT
P
UMP
E
XCLUDING
S
YSTEM
P
UMP
O
PTIONS
Model:
S-ASX 30
S-ASX 35
S-ASX 40
S-ASX 45
S-ASX 50
Unit
Power Supply:
400-3-50
400-3-50
400-3-50
400-3-50
400-3-50
V/Ph/Hz
Maximum Start Current (Includes Soft Start):
94
102
111
131
151
Amps
Nominal Run Current Input:
22.0
24.5
27.0
34.7
39.2
Amps
Maximum Power Input:
13.9
15.5
17.1
21.6
24.5
kW
14.2.2
S
YSTEM
P
UMP
–
M
ODULATING
Model:
S-ASX 30
S-ASX 35
S-ASX 40
S-ASX 45
S-ASX 50
Unit
Nominal Run Current Input:
1.6
1.6
1.6
1.6
1.6
Amps
Maximum Power Input:
0.31
0.31
0.31
0.31
0.31
kW
14.2.3
S
YSTEM
P
UMP
–
H
IGH
H
EAD
(A
DDITIONAL
O
PTION
)
Model:
S-ASX 30
S-ASX 35
S-ASX 40
S-ASX 45
S-ASX 50
Unit
Nominal Run Current Input:
6.1
6.1
6.1
8.2
8.2
Amps
Maximum Power Input:
1.2
1.2
1.2
1.6
1.6
kW
Summary of Contents for S-ASX 30
Page 2: ...2 ...
Page 24: ...24 10 CORRECTIVE FACTORS 10 1 Heating Performances ...