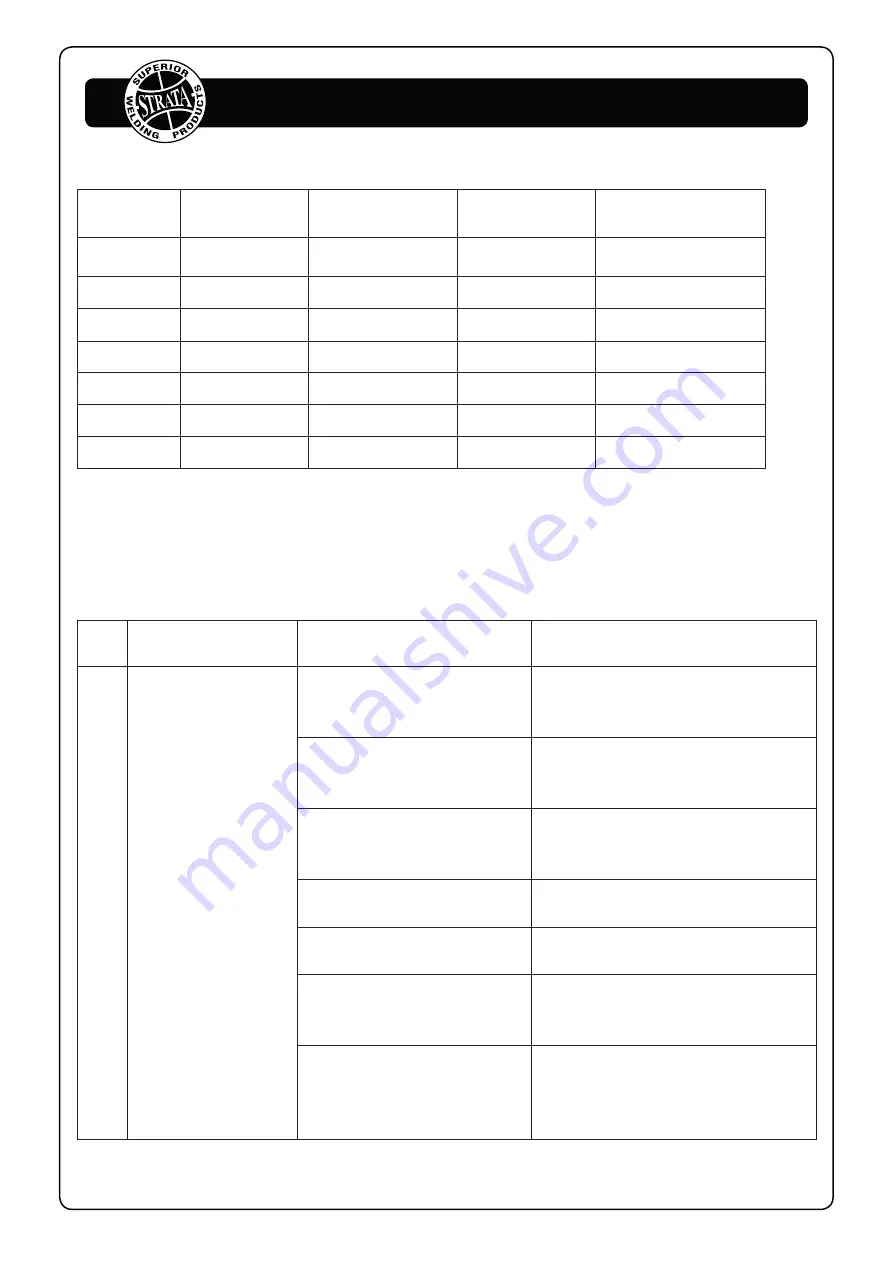
Tungsten Electrode Preparation
Tungsten
Diameter
Diameter at the
Tip - mm
Constant Included
Angle - Degrees
Current Range
Amps
Current Range
Pulsed Amps
1.0mm
.250
20
05 - 30
05 - 60
1.6mm
.500
25
08 - 50
05 - 100
1.6mm
.800
30
10 - 70
10 - 140
2.4mm
.800
35
12 - 90
12 - 180
2.4mm
1.100
45
15 - 150
15 - 250
3.2mm
1.100
60
20 - 200
20 - 300
3.2mm
1.500
90
25 - 250
25 - 350
3.4.6 TIG Welding trouble shooting
The following chart addresses some of the common problems of TIG welding. In all cases of
equipment malfunction, the manufacturer’s recommendations should be strictly adhered to and
followed.
NO. Problem
Possible Reason
Suggested Remedy
1
T
ungsten burning
away quickly
Incorrect Gas or No Gas
Use pure Argon. Check cylinder has
gas, connected, turned on and torch
valve is open
Inadequate gas flow
Check the gas is connected, check
hoses, gas valve and torch are not
restricted.
Back cap not fitted correctly
Make sure the torch back cap is
fitted so that the o-ring is inside the
torch body
Torch connected to DC +
Connect the torch to the DC- output
terminal
Incorrect tungsten being used Check and change the tungsten type
if necessary
Tungsten being oxidised after
weld is finished
Keep shielding gas flowing 10–15
seconds after arc stoppage. 1 second
for each 10amps of weld current.
Tungsten melting back into
the nozzle on AC welding
Check that correct type of tungsten
is being used. Check the balance
control is not set too high on the
balance-reduce to lower setting
34
www.strata.co.nz
EZITIG 205DC