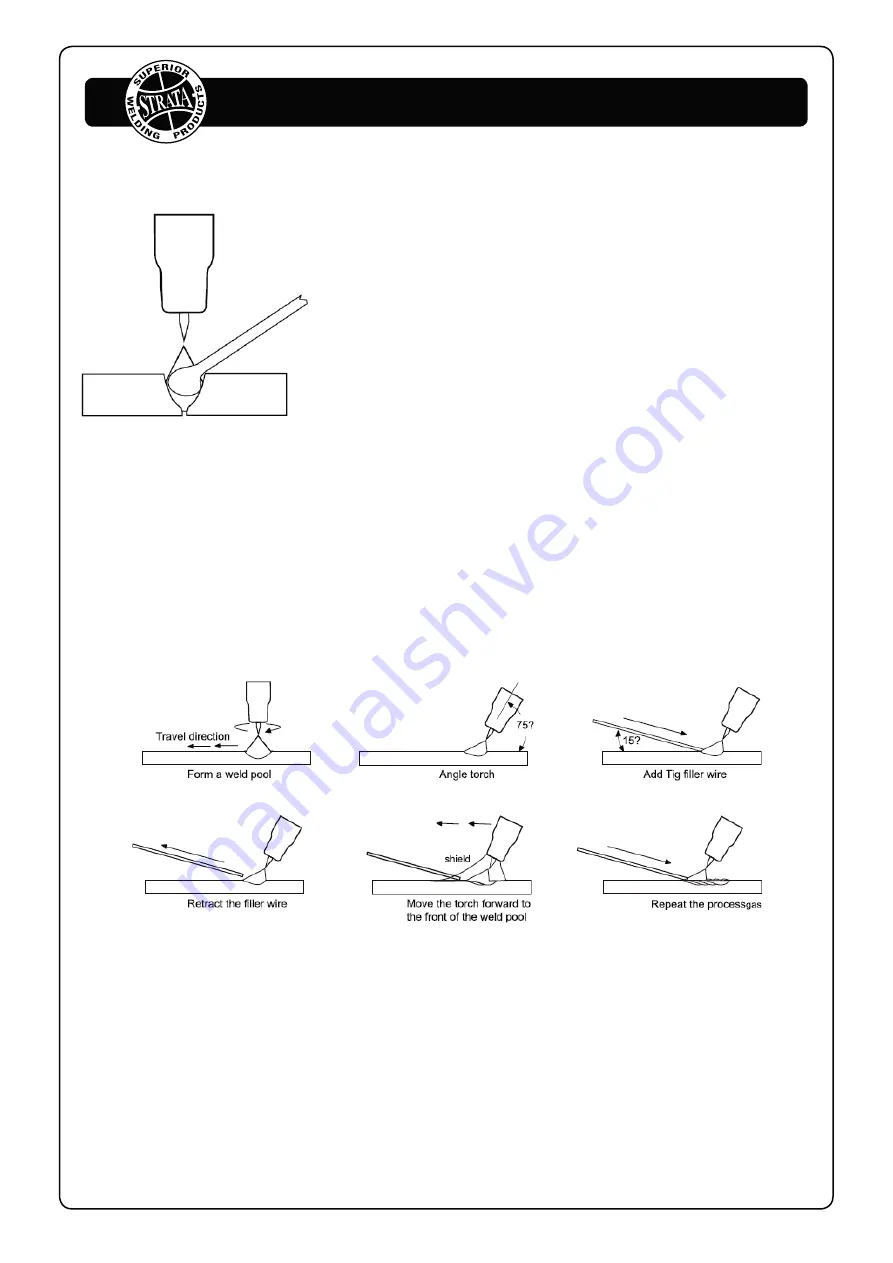
TIG Welding with Filler Wire Technique
It is necessary in many situations with TIG welding to add a
filler wire into the weld pool to build up weld reinforcement
and create a strong weld. Once the arc is started the torch
tungsten is held in place until a weld pool is created, a circular
movement of the tungsten will assist is creating a weld pool of
the desired size. Once the weld pool is established tilt the torch
at about a 75° angle and move smoothly and evenly along the
joint. The filler metal is introduced to the leading edge of the weld pool. The filler wire is
usually held at about a 15° angle and fed into the leading edge of the molten pool, the arc will
melt the filler wire into the weld pool as the torch is moved forward. Also a dabbing technique
can be used to control the amount of filler wire added, the wire is fed into the molten pool and
retracted in a repeating sequence as the torch is moved slowly and evenly forward. It is
important during the welding to keep the molten end of the filler wire inside the gas shield as this
protects the end of the wire from being oxidised and contaminating the weld pool.
3.4.5 Electrodes
Tungsten Electrodes
Tungsten is a rare metallic element used for manufacturing TIG welding electrodes. The TIG
process relies on tungsten’s hardness and high-temperature resistance to carry the welding current to
the arc. Tungsten has the highest melting point of any metal, 3,410 degrees Celsius. Tungsten
electrodes are non-consumable and come in a variety of sizes, they are made from pure tungsten or
an alloy of tungsten and other rare earth elements. Choosing the correct tungsten depends on the
29
www.strata.co.nz
EZITIG 205DC