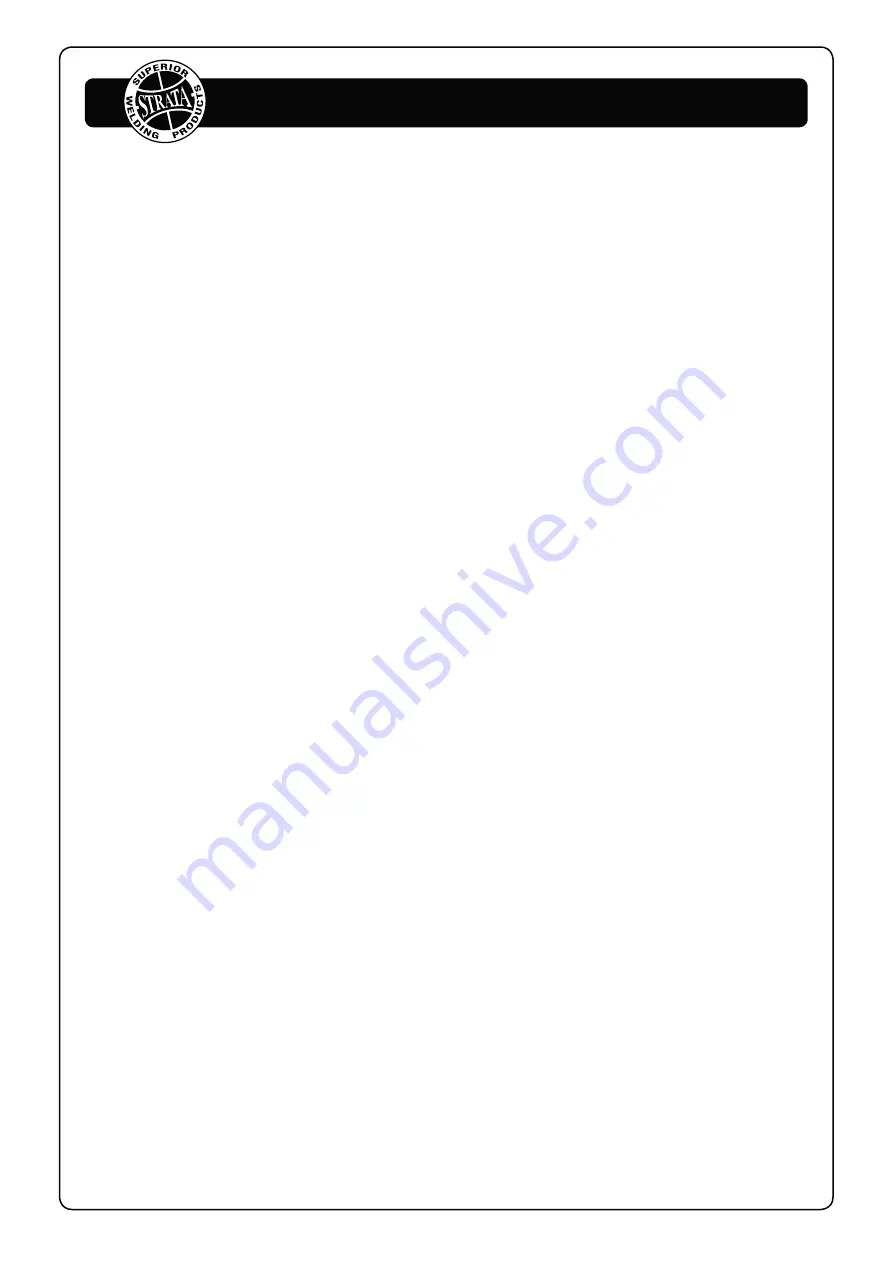
(3) Connect the electrode lead to
“
+
”
,
tighten clockwise;
(4) Each machine is equipped with a power cable should be based on the input voltage welding
power cable connected to the appropriate position, not to pick the wrong voltage;
(5) With the corresponding input power supply terminal or socket good contact and prevent
oxidation;
(6) With a multi meter measure the input voltage is within the fluctuation range;
(7) The power ground is well grounded.
3.3.2 Operation for MMA Welding
(1) According to the above method to install is correct, turn the power switch, so that the power
switch is “ON” position, then the power indicator light, the fan comes on, the device work
properly.
(2) Set the welding mode button to ‘MMA’.
(3) Set the welding parameters as required using the parameters control knob (following the
instructions in the previous section).
(4) Place the electrode into the electrode holder and clamp tight.
(5) Strike the electrode against the work piece to create and arc and hold the electrode steady to
maintain the arc.
(6) Commence welding. If necessary, readjust the Welding parameters control knob to obtain the
welding condition required.
(7) After completion of welding the Power Source should be left turned ON for 2 to 3 minutes.
This allows the fan to run and cool the internal components.
(8) Switch the ON/OFF Switch (located on the rear panel) to the OFF position.
NOTE:
Note the polarity of wiring, the general DC welding wire in two ways. Selected according to
the technical requirements of welding the appropriate connection, if you choose incorrectly
will result in arc instability and spatter large adhesion and other phenomena, such cases can
be quickly reversed to joints.
If the work piece distance from the welding machine, the second line(electrode holder and
ground) is longer, so choose the appropriate conductor cross-sectional area should be larger to
reduce cable voltage drop.
18
www.strata.co.nz
EZITIG 205DC