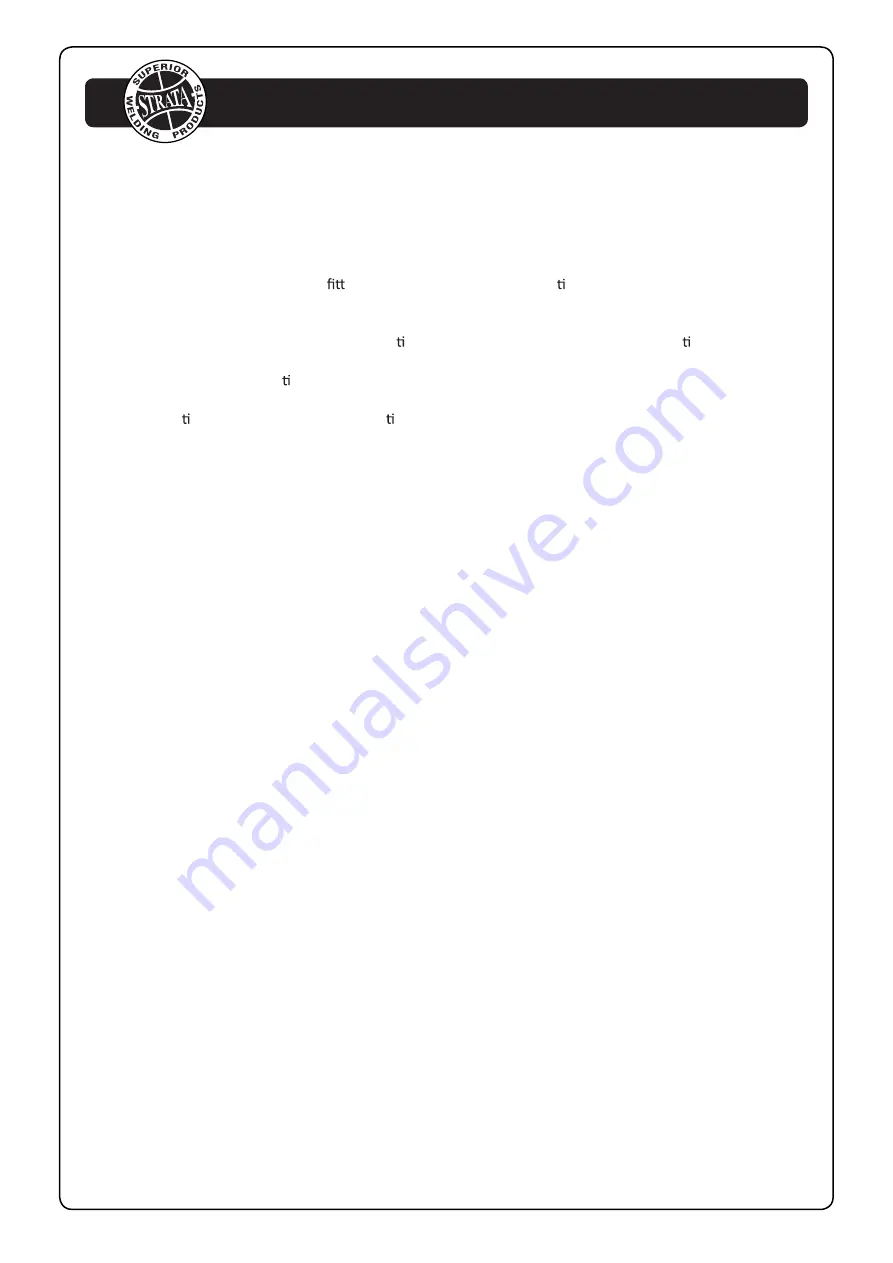
Duty cycle is a measure of the percentage of me a machine will operate within a certain me period at a
given amperage. For example a duty cycle of 160A @ 25% means that a machine will operate at 160A for 2
½ minutes in a 10 minute me period. The machine will have to rest for the remaining 7 ½ minutes to
enable it to cool down.
The interna onal standard for duty cycle ra ng is based on an ambient air temperature of 40°C with 50%
humidity, over a 10 minute period. In an environment with temperatures exceeding 40°C, the duty cycle
will be less than stated. In ambient temperature less than 40°C, duty cycle performance will be higher. There
are numerous other factors that can influence actual duty cycle performance.
4. GENERAL GUIDE TO WELDING
4.1 Duty Cycle Rating
Strata
welding machines are
ed with thermal overload protec
on which means the machine will
cut out when it reaches a certain temperature, to prevent damage to components. The machine will
then re-start when it returns to a safe temperature.
4.2 Choosing a Welding Process – MIG, Stick or TIG?
4.2.1 The Stick (MMA) Process
4.2.1.1 Description
The acronym MMA (or MMAW) stands for Manual Metal Arc Welding. ‘Manual’ refers to the fact
that the MMA process requires the operator to apply filler metal (in contrast to MIG ‘semi-
automa
ti
c’ welding where the machine feeds the filler metal into the weld). ‘Metal’ refers to the
fact that the filler metal itself (the s
ti
ck electrode) is used to conduct the welding current to the
job. MMA welding is commonly known as ‘s
t
ick-electrode’ or ‘arc’ welding.
4.2.1.2 Process
The MMA process involves the electrode being touched on the job to ignite the arc. The electrode
is held in the electrode holder and must be con
ti
nually replaced as it is consumed. The electrode
consists of a metal core, which is the filler metal, covered by a flux coa
tin
g which shields the weld
and prevents it from oxidising. During welding the flux forms into a slag covering the weld which is
chipped off a
er the weld has formed.
4.2.1.3 Advantages
MMA welding offers several advantages over alterna
ti
ve welding processes. Primarily it has a
greater capacity than MIG welding, or in other words it can weld heavier materials with the same
amperage output. For this reason small, portable inverter welders like the
Strata
machines,
have the capacity to weld with up to 3.2mm or 4mm electrodes making it suitable for a
vast range of applica
ti
ons withou
t
the complica
tions
of shielding gas or wire feeding. Moreover,
MMA welding is typically more ‘forgiving’ than MIG or TIG when welding rusty or dirty materials
(which makes it ideal for maintenance applica
tions
ons).
4.2.1.4 Limitations
Tradi
ti
onally, welding thin materials whilst avoiding “blow-through” can be tricky with the MMA
process. This being said, however, welding thin materials with a Strata machine will be
no
ti
ceably easier because the arc is so stable and the output can be very finely adjusted down to
very low amps.
4.2.1.5 Materials
MMA welding can be used with a wide variety of electrodes including general purpose, low
hydrogen, stainless steel, iron powder, hard facing & cast iron just to name a few.
8
www.strata.co.nz
EZIMIG185C
Summary of Contents for EZIMIG185C
Page 12: ...Figure 33 Figure 34 Figure 35 Figure 36 11 www strata co nz EZIMIG185C ...
Page 43: ...9 3 Electrical schematic drawing 42 www strata co nz EZIMIG185C ...
Page 45: ...44 www strata co nz EZIMIG185C ...
Page 46: ...45 www strata co nz EZIMIG185C ...