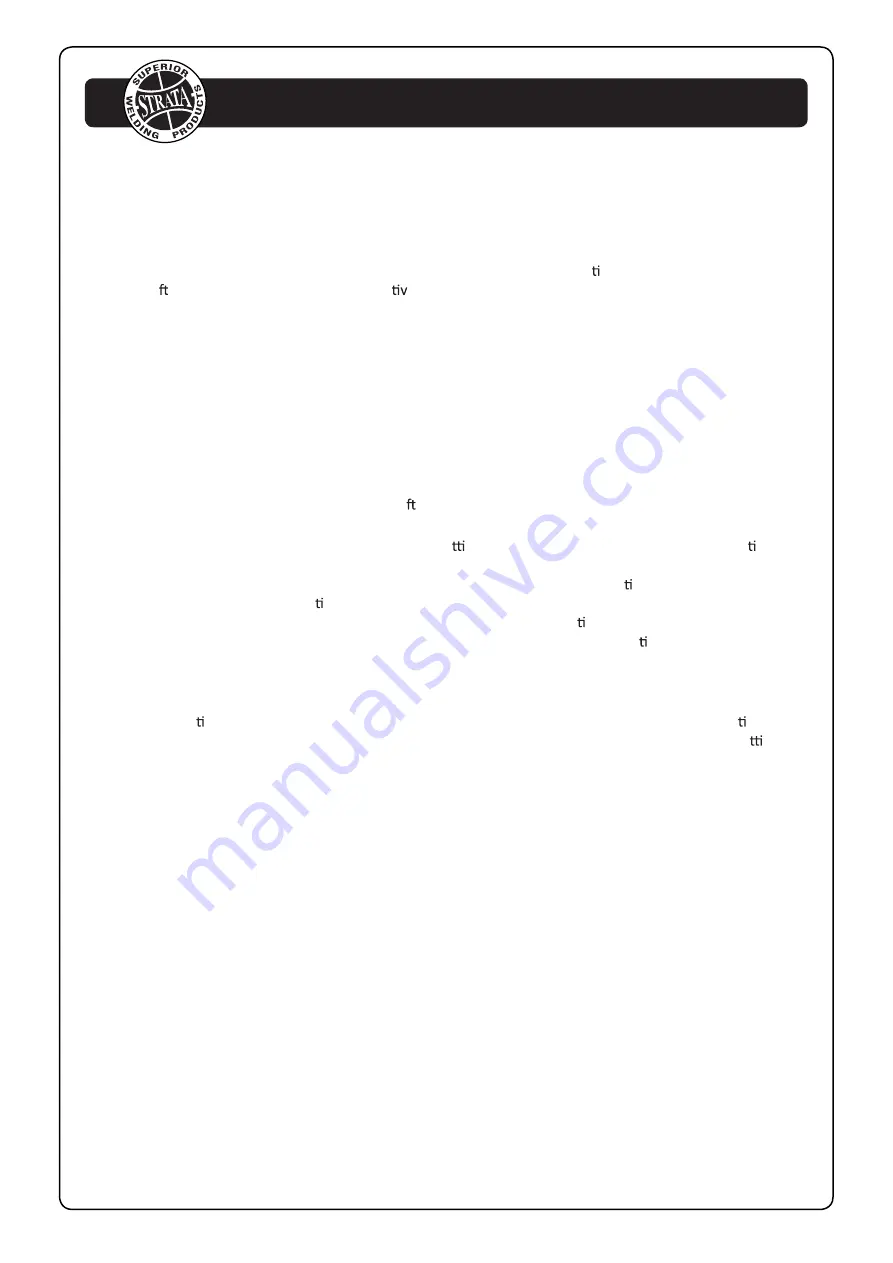
The acronym MIG stands for Metal Inert Gas. Metal’ refers to the fact that the filler metal itself (the
MIG wire) is used to conduct the welding current to the job and create the arc. Inert Gas refers to
the fact that the process relies on an inert gas to prevent weld oxidisa on. The acronym MAG is also
o en used which stands for Metal Ac e Gas. MAG is fundamentally the same as MIG except that
MAG technically refers to when Carbon Dioxide (CO2) is used as a shielding gas (instead of an inert
gas of argon, helium or a mixed gas with these as a base).
The process is also referred to as Gas Metal Arc Welding (GMAW) when gas is used or Flux-Cored Arc
Welding (FCAW) when flux-cored or gasless/self-shielded wire is used.
The MIG welding process involves the filler wire being fed through a torch/gun to the job. The filler
wire carries the welding current to the job. The weld pool is generally covered by an inert gas
supplied from the torch which shields the weld and prevents it from oxidising. However, gasless
welding wire can be used without any shielding gas. This gasless wire has a hollow core filled with
flux which shields the weld and prevents it from oxidising. During welding this flux forms into a slag
covering the weld which is chipped off a er the weld has formed.
MIG welding is both easy and fast. Once weld se ngs are adjusted, the filler wire is fed automa cally
into the weld at the correct rate. It does not rely on the operator to feed in filler wire like TIG welding.
Also because the filler wire is on a roll it lasts significantly longer than a S ck welding electrode so
4.2.2 The MIG Process
4.2.2.1 Description
4.2.2.2 Process
4.2.2.3 Advantages
4.2.2.4 Limitations
4.2.2.5 Materials
there is much less down me in replacing filler wire. MIG can also weld with thin wires at low
amperages achieving great results on thin materials. At the same me, bigger diameter wires and
higher amperages can be used to weld thicker materials with good penetra on. When a shielding
gas is used there is no flux formed on the weld so clean up is minimal.
MIG welding with shielding gas cannot be done in windy environments. However, in many
applica ons gasless/self-shielding wires are available that don’t require gas. MIG tradi onally
requires a higher level of skill and experience to be able to balance voltage and wire speed se ngs
well to achieve a quality result. However, the Synergic programs on this machine make this this very
easy and much more foolproof.
MIG welding can be used with a wide variety of wires including steel, stainless steel, gasless wires,
aluminium, silicone bronze & hard facing just to name a few.
9
www.strata.co.nz
EZIMIG185C
Summary of Contents for EZIMIG185C
Page 12: ...Figure 33 Figure 34 Figure 35 Figure 36 11 www strata co nz EZIMIG185C ...
Page 43: ...9 3 Electrical schematic drawing 42 www strata co nz EZIMIG185C ...
Page 45: ...44 www strata co nz EZIMIG185C ...
Page 46: ...45 www strata co nz EZIMIG185C ...