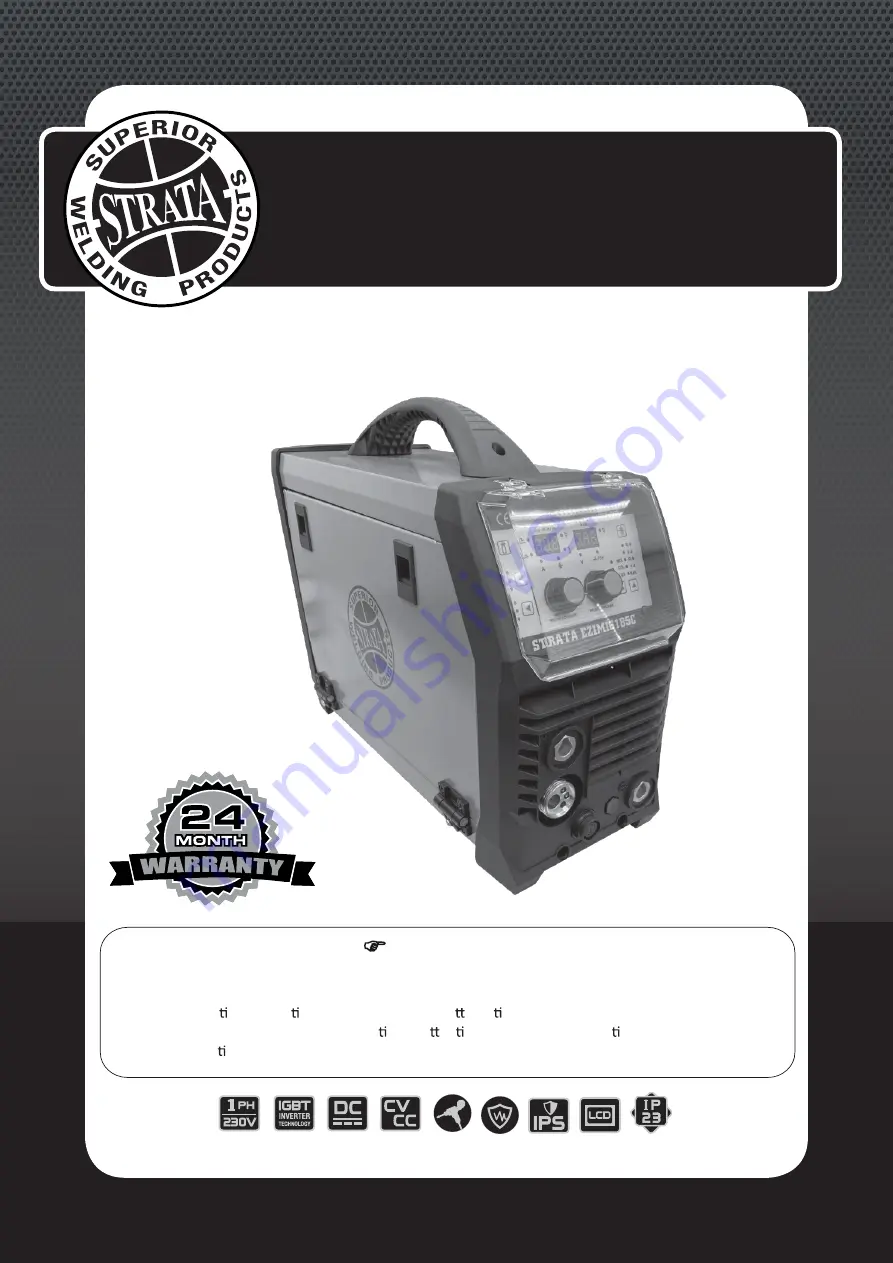
EZIMIG185C
INVERTER WELDER
www.strata.co.nz
230V 50HZ
SINGLE
PHASE
IGBT
INVERTER
TECHNOLOGY
DIRECT
CURRENT
OUTPUT
CONSTANT
CURRENT/
VOLTAGE
SPOOL GUN
CAPABLE
SPIKE/
GENERATOR
SAFE
INTELLIGENT
PROTECTION
SYSTEM
IP23 CORROSION
& SALT SPRAY
RESISTANT
IMPORTANT!
To qualify for full 24 month warranty, you must register within 30 days of purchase. See inside for details.
Read these Opera ng Instruc ons Completely before a emp ng to use this machine. Save this manual and
keep it handy for quick reference. Pay par cular a en on to the safety instruc ons we have provided for
your protec on. Contact your distributor if you do not fully understand anything in this manual.
OPERATING INSTRUCTIONS
LCD
SCREEN
Summary of Contents for EZIMIG185C
Page 12: ...Figure 33 Figure 34 Figure 35 Figure 36 11 www strata co nz EZIMIG185C ...
Page 43: ...9 3 Electrical schematic drawing 42 www strata co nz EZIMIG185C ...
Page 45: ...44 www strata co nz EZIMIG185C ...
Page 46: ...45 www strata co nz EZIMIG185C ...