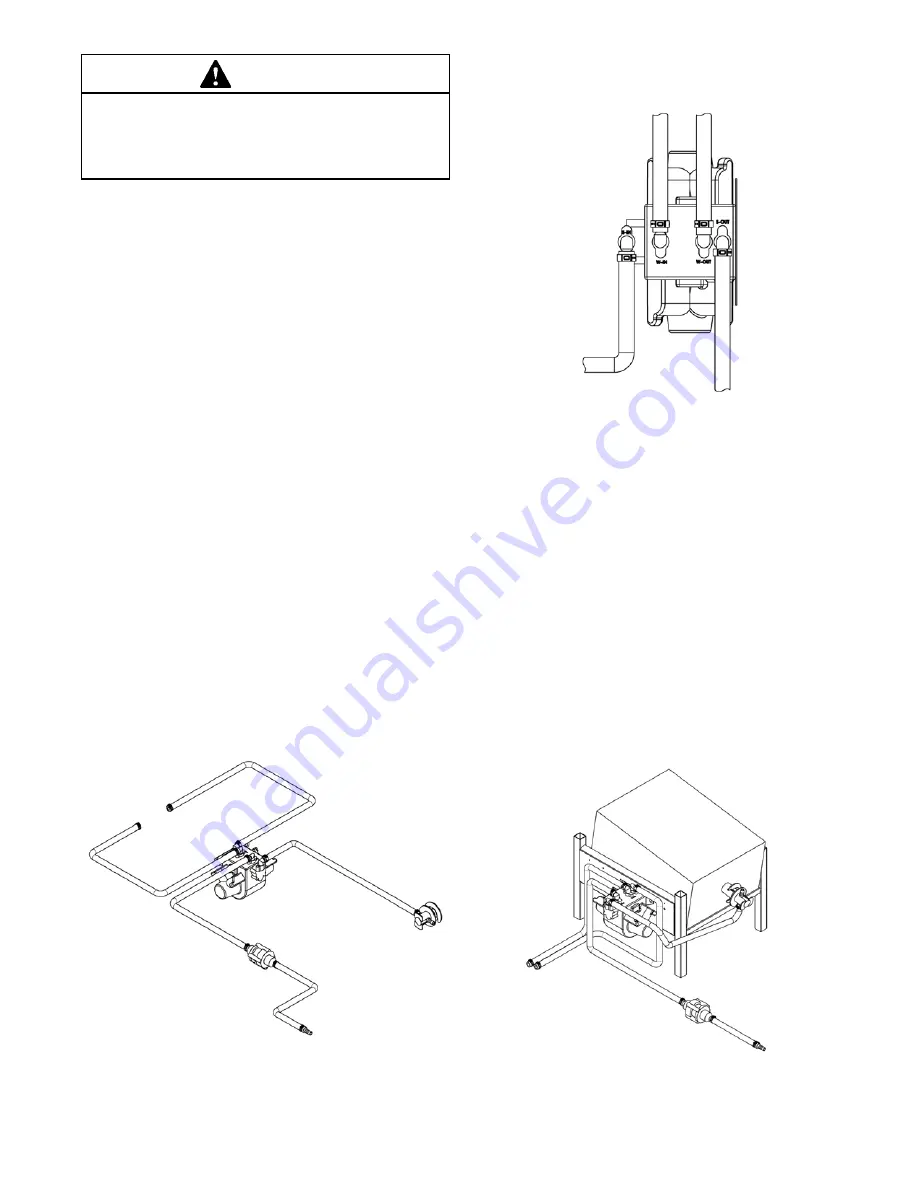
6
WARNING
Do not alter or deform electrical plug in any way.
Altering the plug to fit into an outlet of different con-
figuration may cause fire, risk of electrical shock,
product damage and will void warranty.
H.
Connect the power cord to the proper power
supply. The plug on the E112 is designed for
115VAC / 20 amp duty and the plug on the F112 is
designed for 208-240VAC / 15 amp duty. Check
the nameplate on your machine for proper supply.
The unit must be connected to a properly grounded
receptacle. The electrical cord furnished as part of
the machine has a three prong grounding type
plug. The use of an extension cord is not
recommended, if necessary use one with a size 12
gauge or heavier with ground wire. Do not use an
adapter to get around grounding requirement.
2.4 AUTO FILL PUMP INSTALLATION
The auto fill pump is powered by water and has a fixed orifice
that delivers water and syrup to the machine at an exact
ratio. The auto fill kit is designed for use with Bag In Box
(BIB) concentrated syrup.
Follow these instructions to properly install the brix pump
A.
Route the clear tubing with the BIB connector to
the BIB. If there is excess tubing, trim it and
reconnect it to the BIB connector.
B.
Route the water line tubing to the shutoff valve of the
water supply. Trim excess tubing and connect it to
the shutoff valve.
C.
Route the water line and syrup line tubing (3/8”
braided tubing) from the pump to the machine.
to
machine
water
inlet
to
BIB
Figure 2-4 Auto Fill Pump Tubing Layout
water outlet
to machine
water inlet
from shutoff
valve
syrup outlet
to machine
syrup inlet
from BIB
this side of
pump is
mounted to
the BIB shelf
Figure 2-5 Top View of Pump
Figure 2-6 Auto Fill Pump Kit
D.
Route the water line tubing to the tube exiting the
rear panel. Trim excess tubing and connect.
E.
Route the syrup line to the tubing connected to the
adapter on the hopper cover. Trim excess tubing
and connect.
F.
Check that the clear tubing coming out of the rear
panel is connected to the plug in the hopper cover.
If not, connect it using a clamp in the kit.
G.
Check that all tubing connections are properly
clamped, fittings are tightened and the tubing is not
kinked.
Summary of Contents for E112-LJ
Page 1: ...Model E112 LJ F112 LJ OPERATORS MANUAL Manual No 513643 Feb 2010...
Page 2: ......
Page 6: ......
Page 8: ...2 Figure 1 2 Specifications E112 F112 1 2 SPECIFICATIONS...
Page 10: ...4...
Page 28: ...22...