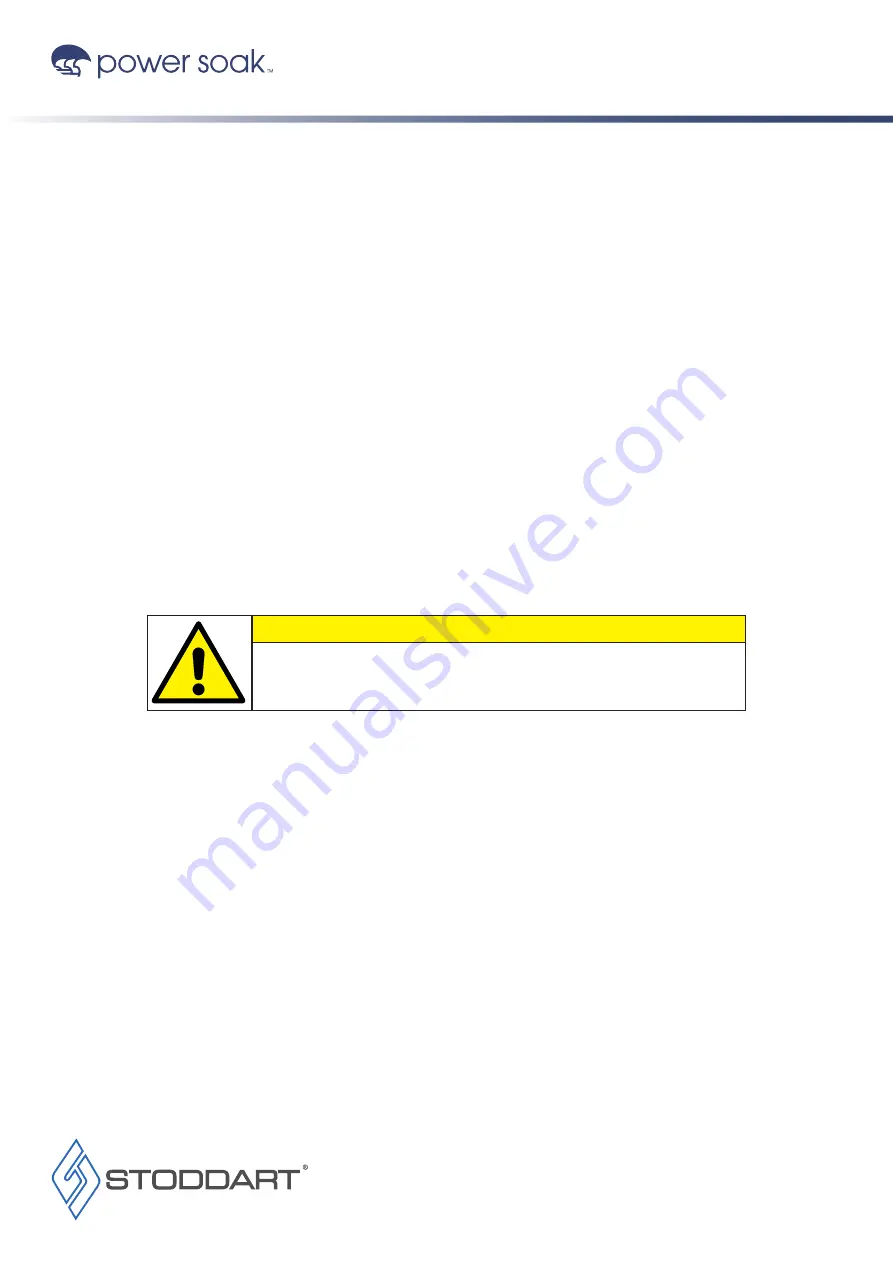
Due to continuous product research and development,
the information contained herein is subject to change without notice.
Page 17
www.stoddart.com.au
Seal around the Splashback and Screws
Final Installation Steps
Machine Placement
Position the Power Soak so that the back splash rests against the wall and is placed according to the floor plan or customer’s selected
location� Examine the drain and water supply lines to determine that the plumbing can be completed when the Power Soak is in the final
location� Verify that the plumbing from the faucet can be reached with the sink against the wall�
Examine the installation to see that the wall and splashback are clean and free of dust and oils� Seal the top and sides of the splashback to the
wall using the clear NSF approved sealant provided with the Power Soak� Seal around the screw heads to be sure they do not allow water to
leak behind the splashback� Wipe off all excess sealant leaving a smooth, clean and sanitary bead of sealant on all the edges�
Downturned-Splashback Z-Clip Installation
If the Power Soak system has a splashback that is downturned, attach the provided Z-Clips to the wall using the following procedure� Using
a level, adjust the feet on the Power Soak until the front rim and the rear rim of the sink are level� The sink must also be level front to back�
Measure from the floor to the top edge of the splashback, and then move the sink away from the wall� Locate Z-Clips by marking a level line
on the wall approximately 1/16” to 3/32” below the height of the splashback top edge� Locate the wall studs and mark the locations� Align top
edge of Z-Clip(s) to the marked line and securely fasten the Z-Clips to the wall, using fasteners provided� Install screws directly to the walls’
studs whenever possible� The Z-Clips should be space as evenly as possible� Move the sink to the wall and lift the back edge over the Z-Clips�
If the Power Soak system has an upturned splashback, skip this step�
Upturned-Splashback Level Attach to the Wall
Using a level, adjust the feet on the Power Soak until the front rim and the rear rim of the sink are level� The sink must also be level front to
back� Locate the wall studs and mark their location on the top edge of the back splash� Measure down ¾” from the top of the splashback and
then drill ¼” diameter holes through the back splash in line with the center of the studs� Use the #10 stainless steel screws (included with the
Power Soak) to attach the Power soak directly to the wall�
If the Power Soak® system has a downturned splashback, skip this step�
Installation
The Power Soak sink assembly must be level from side to side and front
to rear with all the feet making firm contact with the floor.
IMPORTANT