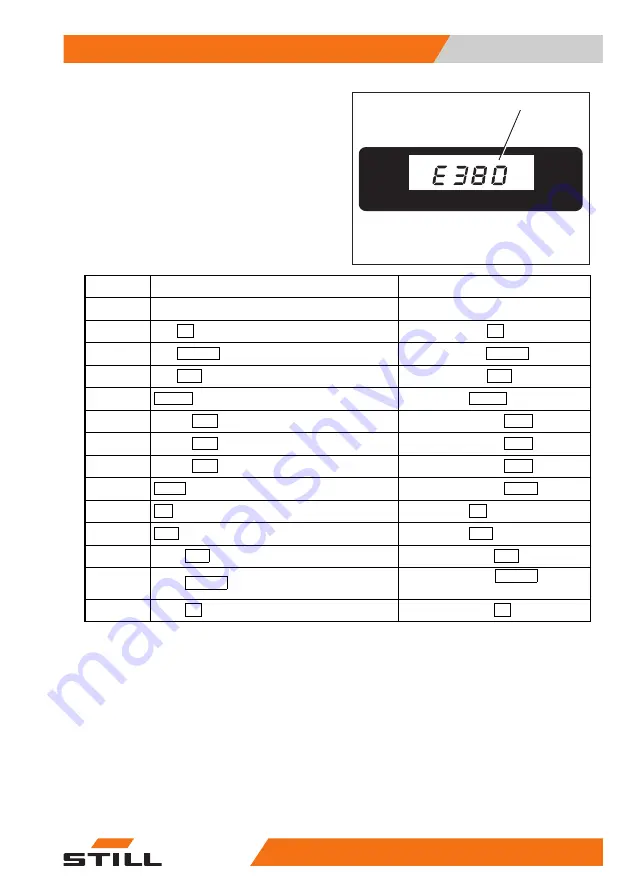
Operation
5
Fault displays
1044_505-019
15
Error code Description
Action
E350
Travel control operated at power-up.
Release the travel control (1).
E370
Left
Lift
button operated at power-up.
Release the left
Lift
button (2).
E371
Left
Lowering
button operated at power-up.
Release the left
Lowering
button (3).
E372
Left
Horn
button operated at power-up.
Release the left
Horn
button (4).
E373
Tortoise
button operated at power-up.
Release the
Tortoise
button (5).
E374
Button
1-2-3
operated at power-up.
Release the button
1-2-3
(6).
E375
Button
4-5-6
operated at power-up.
Release the button
4-5-6
(7).
E376
Button
7-8-9
operated at power-up.
Release the button
7-8-9
(8).
E377
PROG
button operated at power-up.
Release the button
PROG
(9).
E378
ON
button operated at power-up.
Release the
ON
button (10).
E379
Hare
button operated at power-up.
Release the
Hare
button (11).
E380
Right
Horn
button operated at power-up.
Release the right
Horn
button (12).
E381
Right
Lowering
button operated at power-up.
Release the right
Lowering
button
(13).
E382
Right
Lift
button operated at power-up.
Release the right
Lift
button (14).
.
50108043405 [EN]
93
Summary of Contents for CX
Page 1: ...Original instructions Low level order picker CX CX D CX H 1063 1069 50108043405 EN 02 04 2014 ...
Page 2: ......
Page 9: ...1 Foreword ...
Page 18: ...1 Foreword Environmental considerations 10 50108043405 EN ...
Page 19: ...2 Introduction ...
Page 30: ...2 Introduction Residual risks 22 50108043405 EN ...
Page 31: ...3 Safety ...
Page 46: ...3 Safety Battery connection cables 38 50108043405 EN ...
Page 47: ...4 Overview ...
Page 63: ...5 Operation ...
Page 113: ...6 Maintenance ...
Page 138: ...6 Maintenance Maintenance every 500 hours 130 50108043405 EN ...
Page 146: ...6 Maintenance Maintenance every 5000 hours 138 50108043405 EN ...
Page 147: ...7 Technical characteristics ...
Page 148: ...7 Technical characteristics Dimensions Dimensions 140 50108043405 EN ...
Page 152: ...7 Technical characteristics Fork dimensions 144 50108043405 EN ...
Page 155: ......
Page 156: ...STILL GmbH Berzeliusstrasse 10 D 22113 Hamburg Ident no 50108043405 EN ...