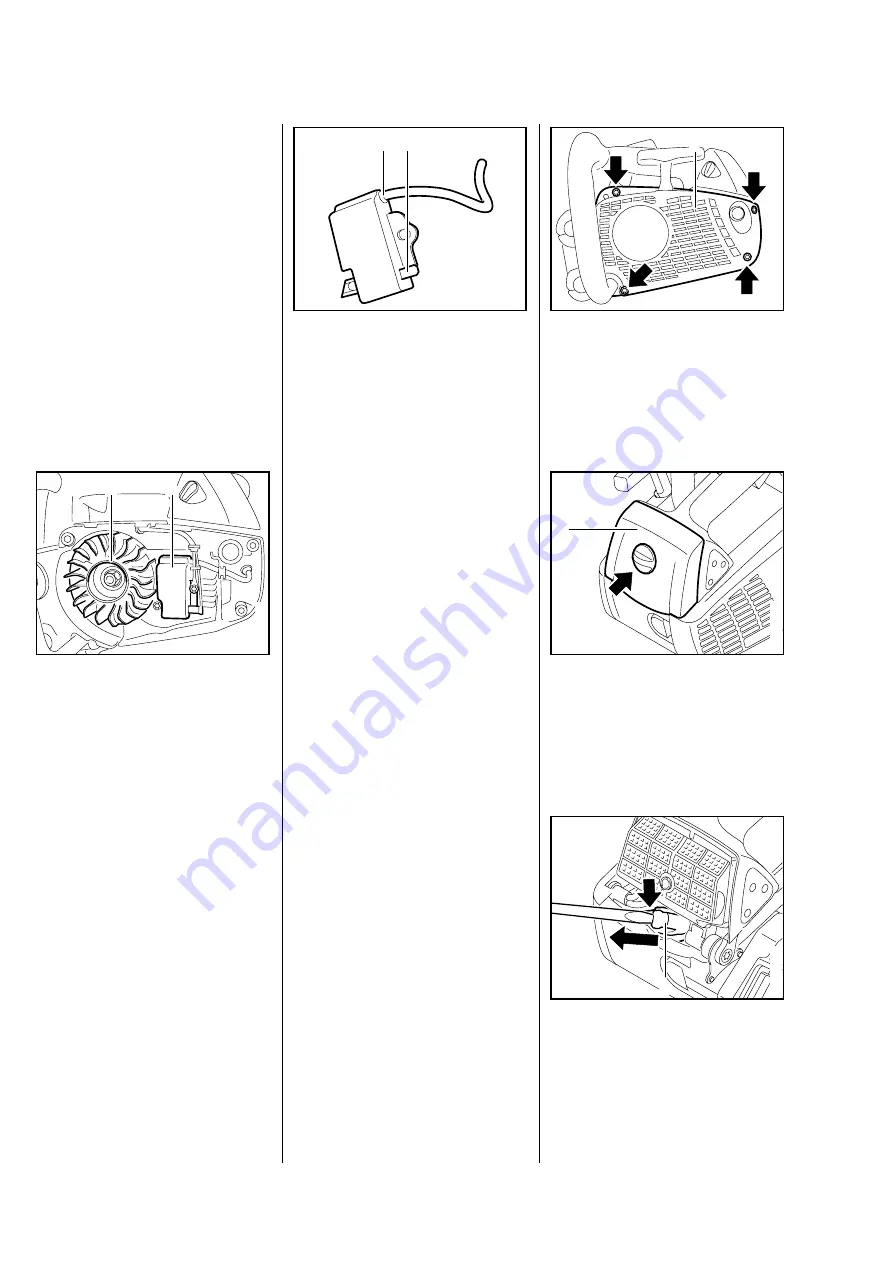
42
MS 192 T
Exercise extreme caution while
carrying out maintenance and repair
work on the ignition system. The
high voltages which occur can
cause serious or fatal accidents.
Troubleshooting on the ignition
system should always start with the
spark plug,
The electronic ignition system
basically consists of an ignition
module (1) and flywheel (2).
2
1
217RA097 TG
The ignition module accommodates
all the components required to
control ignition timing. There are
two electrical connections on the
coil body:
:
High-voltage output (1) with
permanently fitted ignition lead
1 2
217RA325 TG
:
Connector tag (2) for the short
circuit wire.
Testing in the workshop is limited to
a spark test. A new ignition module
with ignition lead must be installed if
no ignition spark is obtained (after
checking that the wiring and stop
switch are in good condition),
Ignition timing is fixed and cannot
be adjusted during repair work.
Since there is no mechanical wear
in these systems, ignition timing
cannot get out of adjustment during
operation.
:
Take out the screws (arrows) and
remove the fan housing (1) with
rewind starter.
217RA087 TG
1
:
Turn the twist lock (arrow)
anticlockwise to release it and
remove the carburetor box
cover (1).
217RA008 TG
1
:
Apply a suitable tool to the tab
(arrow) to prise the boot off the
spark plug (1).
1
217RA009 TG
9.
Ignition System
9.1
Ignition Module
9.1.1
Removing and installing