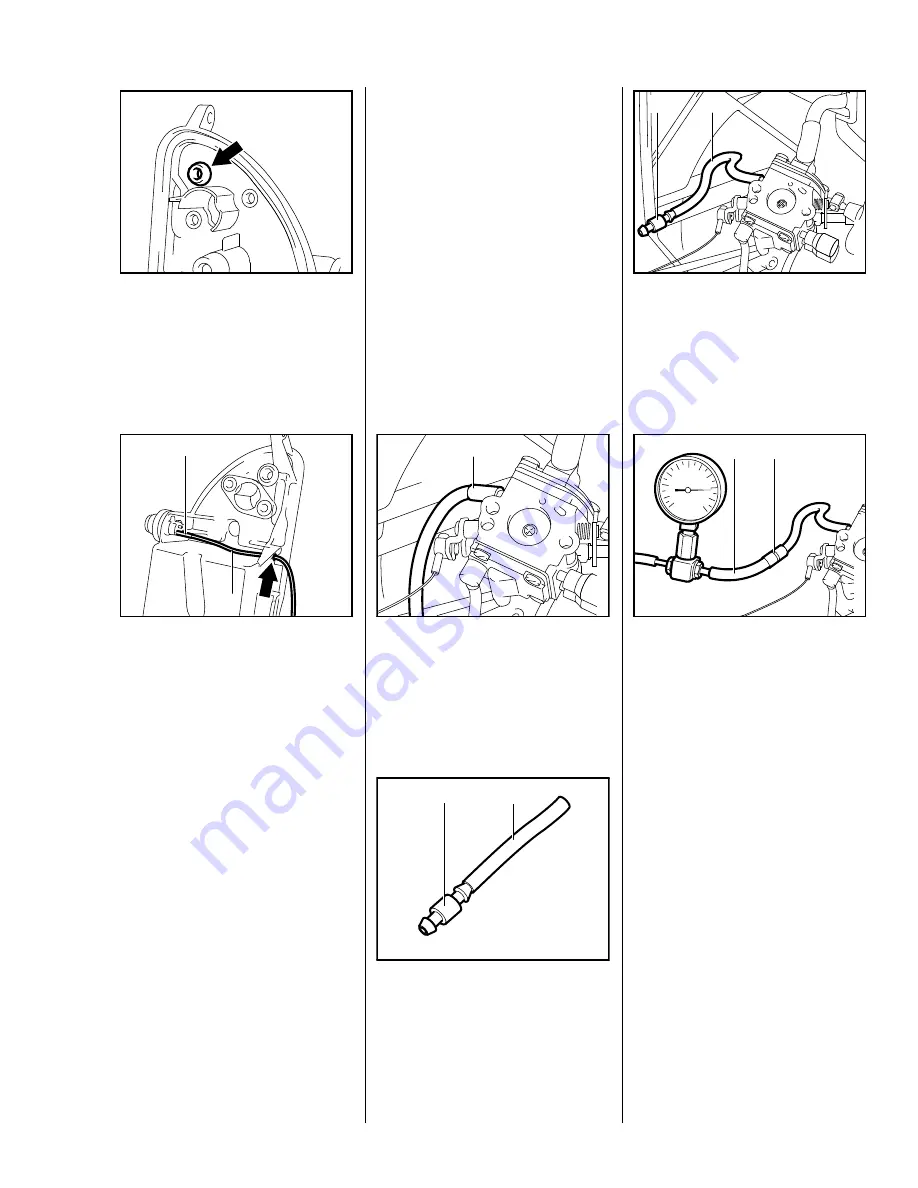
19
BR 500, BR 550, BR 600
Use a new grommet.
:
Push the grommet into the filter
housing from the rear until its
groove (arrow) engages the
housing.
452RA051
VA
:
Clip the fuel pump in place so that
the longer stub (1) is at the
bottom.
:
Pass the hose (2) that comes
from the tank through the housing
bore (arrow) and push it onto the
long stub (1).
452RA036
1
VA
2
Install all other parts in the reverse
sequence.
– Check tension of throttle cable,
adjust if necessary,
b
9.3.2
– Troubleshooting,
b
4.3
In the event of trouble with the
carburetor or fuel supply system,
always check, clean or replace the
tank vent,
b
6.5
The carburetor can be tested for
leaks with the carburetor and
crankcase tester 1106 850 2905.
– Remove the air filter,
b
6.1
– Open the tank filler cap to relieve
pressure.
– Close the tank filler cap.
:
Disconnect the fuel hose (1) from
the carburetor.
452RA037
VA
1
:
Push the hose (1) 1110 141 8600
onto the nipple (2)
0000 855 9200.
VA
143RA172
2
1
:
Push the hose (2) with nipple (1)
onto the carburetor’s elbow
connector.
452RA038
VA
2
1
:
Connect hose (1) of tester
1106 850 2905 to the nipple (2).
452RA162
VA
2
1
6.2
Carburetor
6.2.1
Leakage Test
RA_452_00_01_02.book Seite 19 Donnerstag, 16. Februar 2012 11:52 11