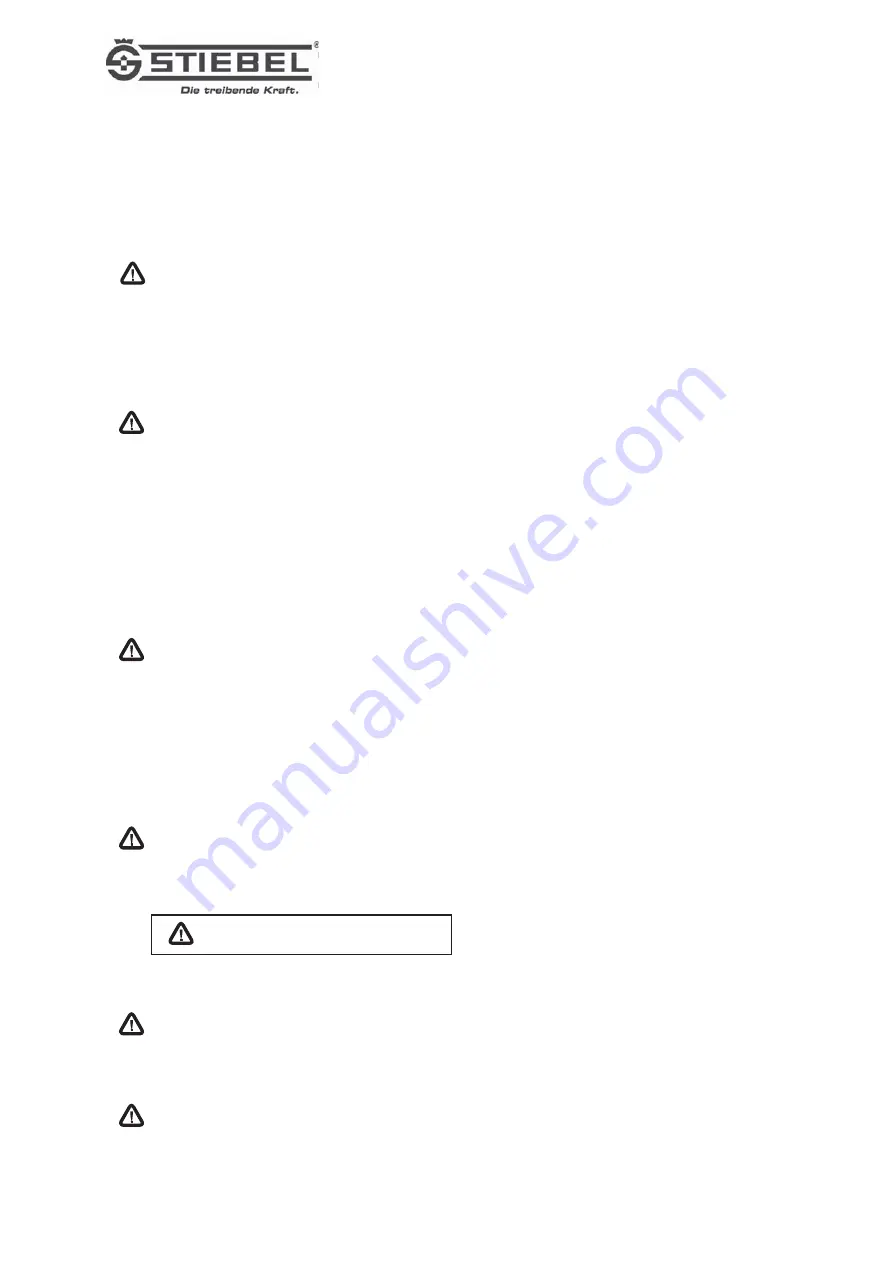
5. Set-up and putting into operation
Assembly and commissioning may only be
carried out by properly qualified personnel.
Before commissioning, including the test
run, it must be ensured that no danger can
arise from moving and rotating parts (e.g.
shafts, clutches etc.). This means that the
necessary
protection
against
accidental
contact must be present or that it is
impossible to approach the danger zone.
For attached electrically-driven devices and
additional equipment, e.g. electric motors,
brakes, remote adjustments, frequency and
smooth-startup controls, regulating pinions,
the accompanying and attached separate
operating instructions must be followed.
Particular attention must be paid to the safety
information for electrical installations. Work
on electrical equipment may only be carried
out by a specialist electrician in accordance
with the electro-technical regulations.
Before
work
on
the
gear
or
attached
equipment is carried out, the power supply
must
be
disconnected.
Precautionary
measures must be taken to prevent them
being switched on unintentionally. Where
necessary,
mechanical
means
(special
equipment, supports etc.) must be used to
ensure that the machine cannot move or
rotate.
Before commissioning, it must ensured that
the prescribed amount of lubricant has been
filled. Units ordered without oil are marked
with a tag:
See the nameplate or operating instructions
for the correct amount and quality of oil.
Never operate without ventilating filters,
otherwise the excess pressure resulting in
the gear from the build-up of heat will cause
an oil leak.
After long periods of operation, the lubricant
and the surface of gearboxes can reach
temperatures which can burn the skin.
Machines in which these gears have been
installed
can
produce
loud
noises
which
damage hearing over longer periods. In this
case, operating personnel should be provided
with hearing protection. To reduce noise, all
technical means possible should be used with
consideration to the statutory regulations.
Technical Information
Housing:
torsion-rigid divided housing made
from grey cast iron or aluminium
Toothing:
helical toothed spur wheels
Lubrication: oil-bath splash lubrication
Attachment and Assembly of Gearboxes
Shaft mounted reducers are mounted with the
hollow shaft directly onto the drive shaft of a unit
and secured against becoming detached. The
reaction moment is supported by an integrated
torque arm see fig. 5, page 21.
To ensure smooth assembly, it is essential that
all prescribed tolerances are observed.
Hollow shaft keyway:
keyways in accordance with DIN 6885, sheet 1
Shaft end
:Ø
£
50 ISO k6
:Ø > 50 ISO m6
Hollow shaft shrinking disk: shaft end h7
Total height:
shaft end Rt = max 16
m
m
Before assembly, check the surfaces and edges
of the shaft end and key for damage and repair
any damage. Key, Keyway coat the shaft end
with white solid lubricant paste (e.g. Optimol
White T). The paste makes it easier to mount the
gears and prevents corrosion which would
make
later
disassembly
significantly
more
difficult. Shrinking disk connections must be
clean and free of grease.
Fitting must not be carried out by hitting as this
can damage or destroy the housing and
bearings. Screw a threaded spindle into the
centre hole of the drive shaft and fit the gears
using a disk and hexagon cap nut; see fig. 1 page
21. It must be ensured that the shaft and hollow
shaft do not tilt and so become damaged.
10
Do not operate without oil filling !