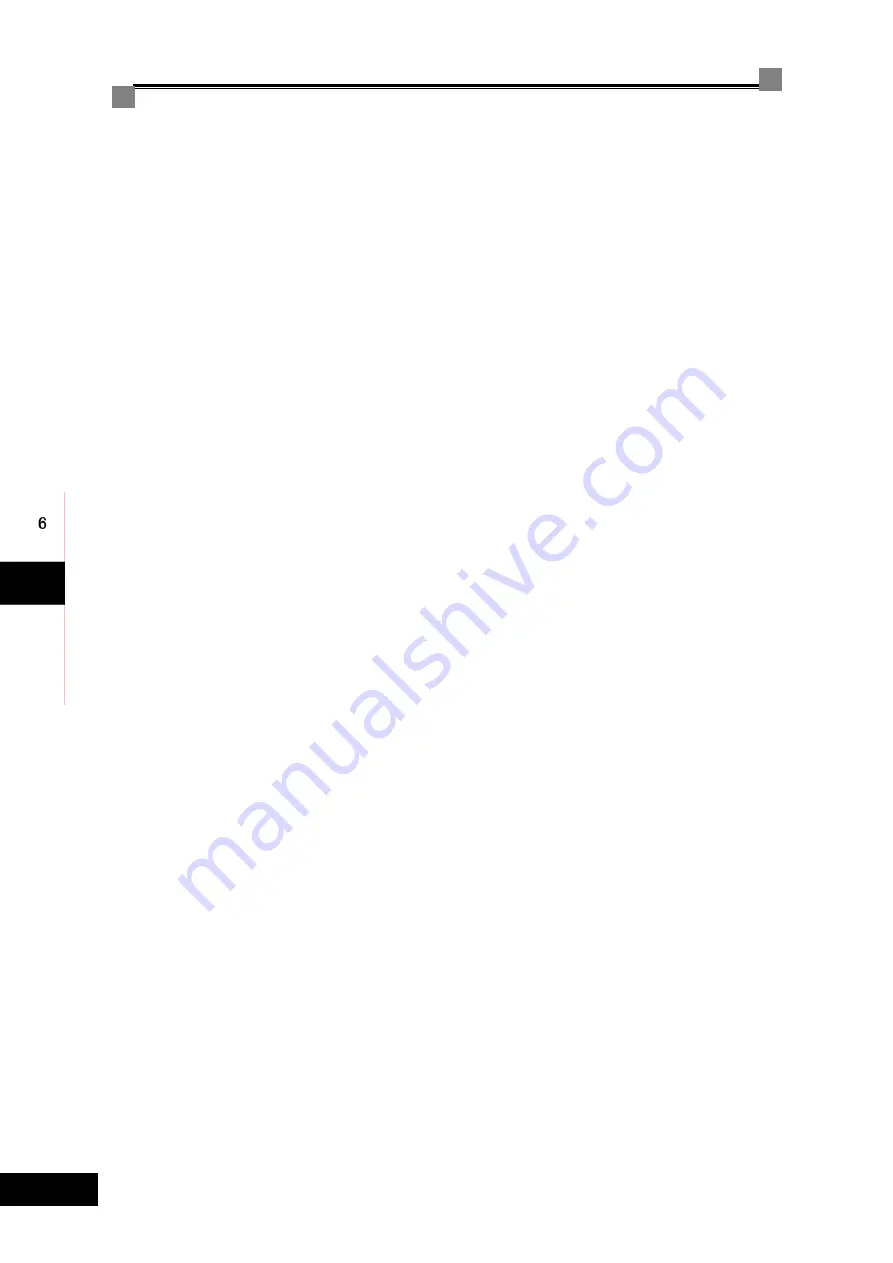
Shanghai STEP Electric corporation
6-
10
Function Parameter List
Note 5: AI1 analog limit B12
When the speed is given through analog voltage inputs, B12 defines the voltage input (in
mV) from the corresponding analog input port AI1 at the highest speed. When it is set to
“10000”, if AI1 input is 10V, the given speed is the highest level; if AI1 input is 1V, the given
speed is 1/10 of the highest. When it is set to “9000”, if AI1 input is 9V, the given speed is
the highest; if AI1 input is 1V, the given speed is 1/9 of the highest. When the input voltage
exceeds 9V, the speed remains at the highest level. Generally, this parameter needs no
modification. However, slight adjustment may reduce elevator vibration at the highest
speed. For example, the maximum analog voltage to set the speed given by the elevator
controller is 9.8V, meaning that the speed will be its highest level when the input voltage is
9.8V. If the input voltage at the analog port fluctuates between (9.8 – a) V and (9.8 + a) V
at the highest speed due to certain reasons, the actual given speed of the Inverter will
fluctuate accordingly. When a reaches a certain level, the elevator will vibrate. In such
situations, set B12 to (9.8
-
a) × 1000 (since the parameter is represented in mV), the
given speed will reach its highest level when the input voltage is (9.8 – a) V. Due to the
limiting function, when the input voltage fluctuates between (9.8 – a) V and (9.8 + a) V, the
speed received by the Inverter will remain at its highest level, thus preventing the
above-said vibration.
Note 6: adjusting mode B13
For asynchronous motors, B13 shall be set to 1 and may not be changed. For
synchronous motors, when elevator speed >= 2m/s, it shall be set to 0; when the speed <
2m/s, it shall be set to 1. This parameter generally needs no modification. When the motor
shows significant noises, however, it may be set to 2, 3 or 4 gradually until the noise is
reduced as required. It is worthwhile to mention that a higher value of this parameter may
lead to jitter of the motor.
Note 7: brake confirmation time B14
B14 is valid only when the Inverter is to detect the brake (or brake contactor) contact and
one of F01 to F12 is set to 2 (i.e., the corresponding port DI is defined as input of brake (or
brake contactor) contact detection. In this situation, the time set by B14 is the delay from
the closing command of the brake contactor to the confirmation of the validation of brake
(or brake contactor) detection signal. This parameter is used to detect brake contactor
faults. If the detection signal is still invalid (i.e., the contacts are not yet closed) after B14
delay, Fault 22 (brake or brake contactor fault) signal will be sent.
If none of F01 to F12 is set to 2 (i.e., no DI port is defined as the input of brake (or brake
contactor) contact detection), B14 is invalid, and the Inverter will not send the above fault
alarm under any circumstance.
Note 8: brake opening delay B15
B15 needs configuration only when the Inverter is to directly control the brake contactor.
B15 defines the delay from the starting of Inverter power output and motor excitation to
the sending of brake contactor closing command to open the brake when start.