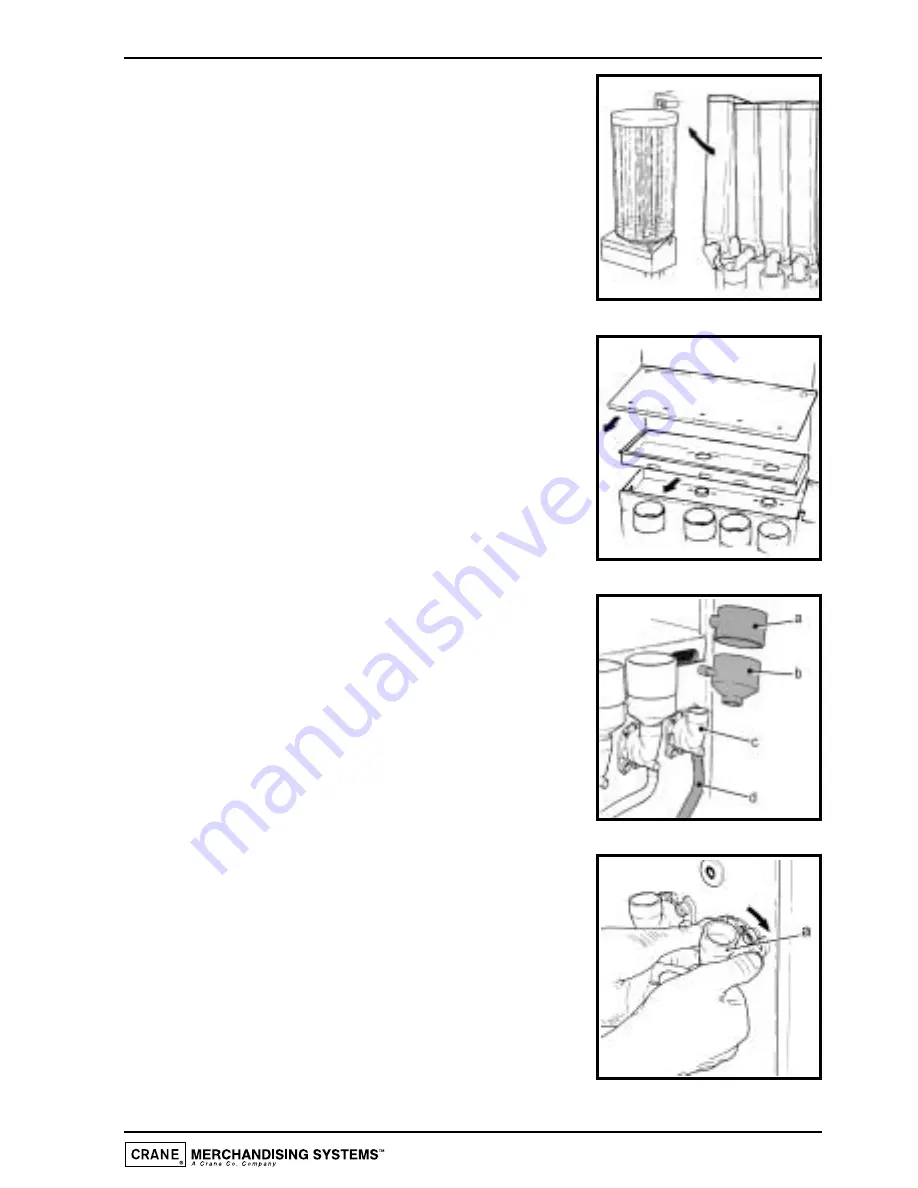
13
Operator’s Manual
1.
On arrival at the machine, open the door. Fill a
cleaning bucket with hot water and dilute the
bactericidal cleaner in accordance with the
instructions on the product packaging.
Swing the cup turret assembly out of the machine
in order to gain access to the ingredient canisters.
Remove the ingredient canisters. DO NOT PLACE
THEM ON THE FLOOR.
2.
Remove the canister shelf and extract tray.
Using a dry brush, clean the area under the extract
tray.
Wipe the upper interior of the machine. Clean the
extract tray and refit into machine.
3.
Remove steam hoods (a) and mixing bowls (b) from
whipper bases (c).
Remove the dispense pipes (d) from the whipper
bases (c) and the plastic dispense block.
Remove the plastic thumb-screw securing the
plastic
dispense
block
to the dispense head
assembly. Remove the dispense block and clean
thoroughly with the mixing system components.
4.
Remove the complete whipper unit (a), including the
whipper base as shown.
Split the whipper unit into separate parts - whipper
base, mixing chamber and impeller.
Clean all of the mixing parts, including the steam
hoods and mixing bowls thoroughly in the diluted
bactericidal cleaner solution.
Rinse all components with clean water and dry
thoroughly before refitting to machine.
Summary of Contents for Contour
Page 2: ......
Page 36: ...Notes 34 Operator s Manual ...
Page 37: ...Notes 35 Operator s Manual ...
Page 38: ...Notes 36 Operator s Manual ...
Page 39: ......