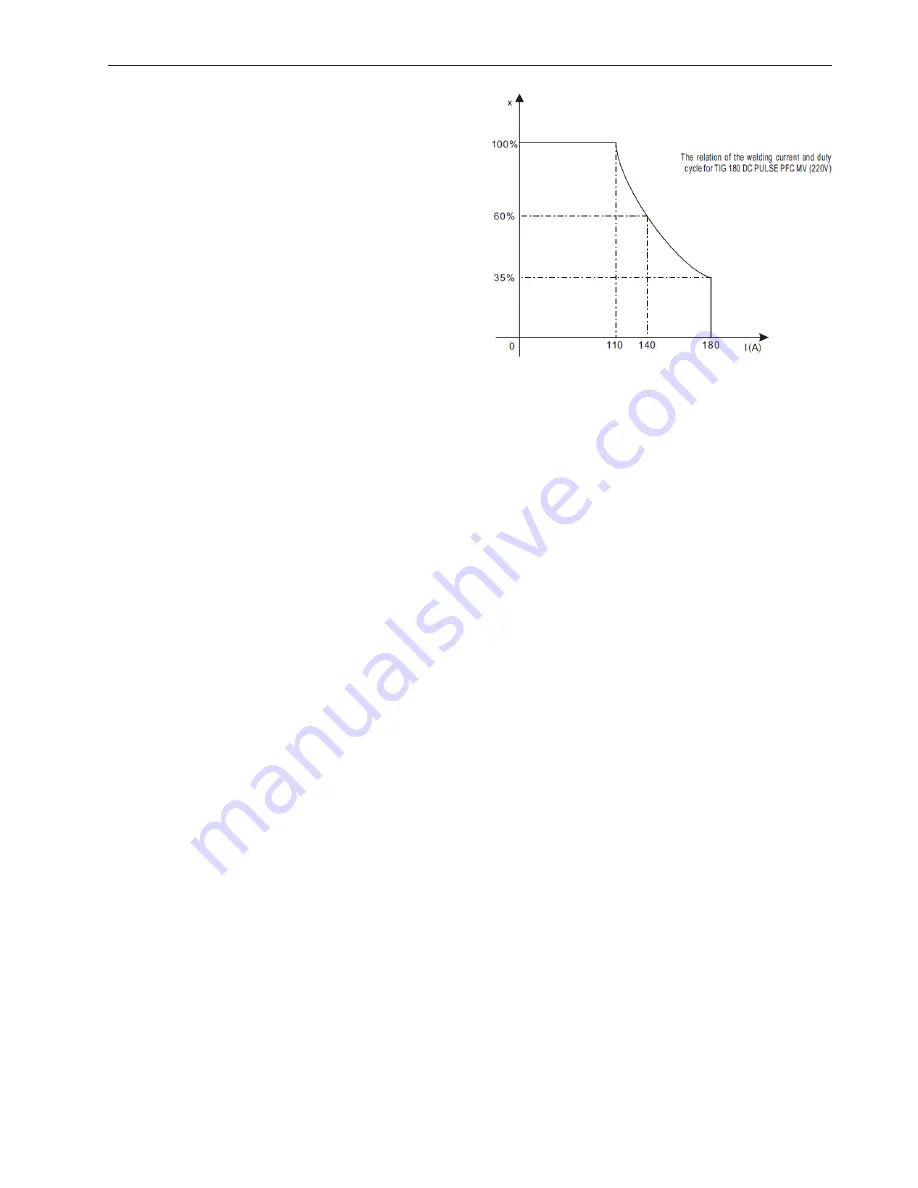
STEALTH DIGI-TIG 180 DC PULSE PFC MV
3.2 Duty Cycle and Over-heating
The letter ‘X’ stands for duty cycle,
which is defined as the proportion
of the time that a machine can work
continuously within a certain time (10
minutes). The rated duty cycle means
the proportion of the time that a
machine can work continuously within
10 minutes when it outputs the rated
welding current.
The relation between the duty cycle ‘X’
and the output welding current ‘I’ is
shown as the figure on the right.
If the welder is over-heating, the IGBT over-heating protection unit inside will send a
message to cut output welding current and illuminate the pilot lamp on the front
panel.
At this point, the machine should be turned off for 15 minutes to cool the fan. When
operating the machine again, the welding output current or the duty cycle should be
reduced.
3.3 Movement and Placement
Please take care when moving it the machine and keep it level.
It also can be moved by the handle on the top. Place the machine securely when in
the right location. When moving using a forklift, ensure the arm lengths are long
enough to reach outside the machine to safely lift.
The movement may result in the potential danger or substantive hazard, so please
make sure that the machine is in a safe position before using it.
3.4 Power Supply Input Connection
TIG DC PULSE PFC MV welding machine’s power supply connects to 110/220V.
When the power supply voltage is over the safe working voltage, there are over-voltage
and under-voltage protection inside the welder. The alarm light will illuminate and, at
the same time, the current output will be cut off.
If the power supply voltage continually goes beyond the safe work voltage range, it will
shorten the machine’s life-span. The below measures can be used:
• Change the power supply input net (connect the welder with the stable power supply
voltage of distributor).
• Switch on the machines using power supply at the same time.
• Set the voltage stabilisation device in the front of power cable input.
INSTALLATION AND ADJUSTMENT
10
§3.2 Duty cycle & Over heat
The letter “X” stands for duty
cycle, which is defined as the proportion
of the time that a machine can work
continuously within a certain time (10
minutes). The rated duty cycle means
the proportion of the time that a
machine can work continuously within
10 minutes when it outputs the rated
welding current.
The relation between the duty cycle “X” and the output welding current “I” is shown as the
right figure.
If the welder is over-heat, the IGBT over-heat protection unit inside it will output an
instruction to cut output welding current, and brighten the over-heat pilot lamp on the front panel.
At this time, the machine should be relaxed for 15 minutes to cool the fan. When operating the
machine again, the welding output current or the duty cycle should be reduced.
§3.3 Movement and placement
Please take care for the welder when moving it, and do not make it sloped.
It also can be moved by the handle on the top of the welder. Place the welder well when
moving it to the right position. When the machine gets to the destination, it needs to be fixed up to
avoid gliding.
When using forklift, its arm length must be long enough to reach the outside so as to ensure
lifting safely.
The movement may result in the potential danger or substantive hazard, so please make sure
that the machine is on the safe position before using it.
§3.4 Power supply input connection
TIG DC PULSE PFC MV welding machines’ power supply connects to 110/220V.
When the power supply voltage is over the safe work voltage, there are over voltage and
12