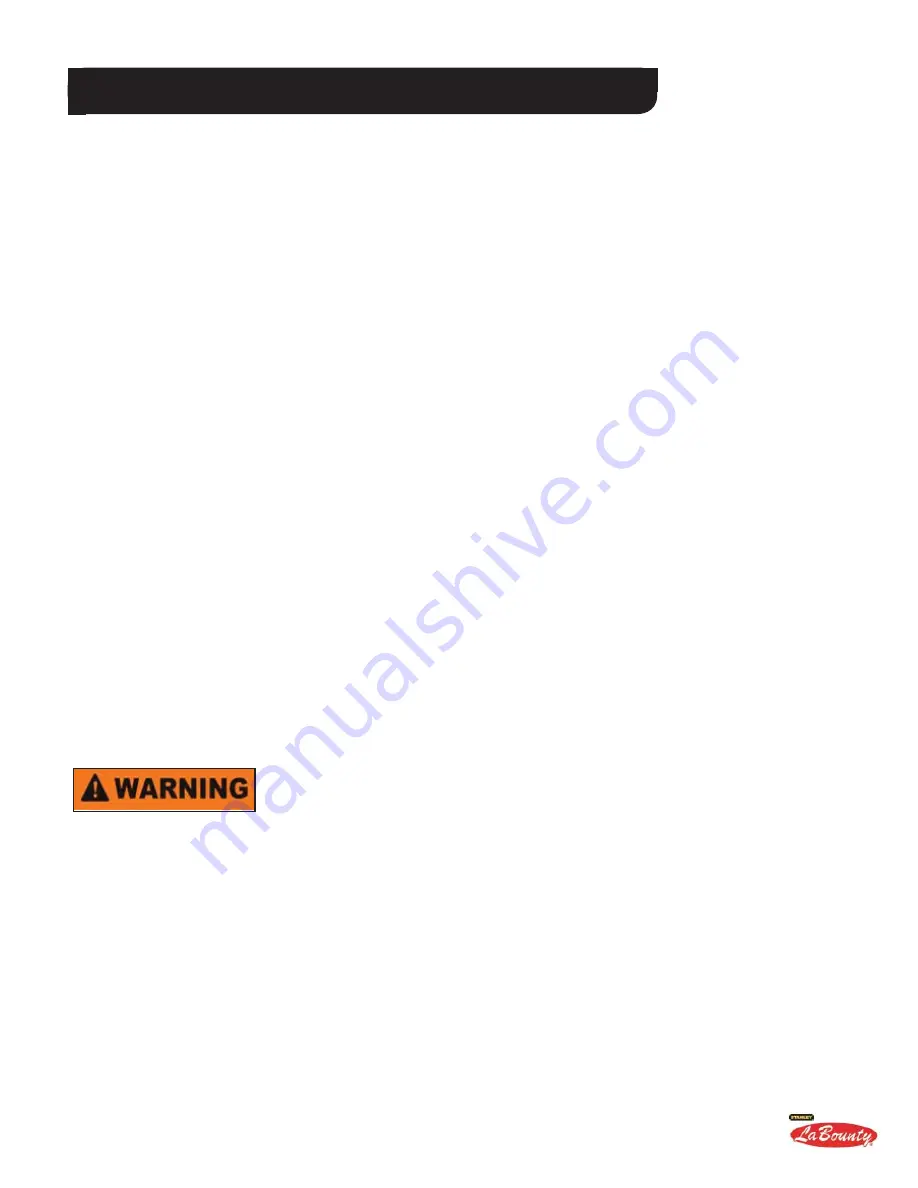
Page 34 Section 5
Maintenance
MSD SABER SERIES SHEARS
LOWER WEAR PLATE REPLACEMENT
continued
5.
Position the new top wear plate so it is also centered across the width of the cross plate. This wear plate
should overhang the front edge of the cross plate to be fl ush with the face of the front wear plate. Clamp the
wear plate into position, bring the preheat back up to 400°F (200°C) and tack weld in place.
6.
Use the recommended build-up weld rod to fi ll the area between the wear plates. Then weld an approxi-
mate 3/8" (10 mm) fi llet on all remaining sides around the wear plates. Also weld a fi llet around the inside of
the holes on the front. Stress relieve each pass by peening. Grind welds smooth.
7.
If the temperature within 6" (150 mm) of the weld area has dropped below 400°F (200°C) during the weld
process, post-heat this area to 400°F (200°C).
8.
Wrap with a heat blanket and allow the welded area to cool slowly to the ambient temperature. The shear
should not be put back into service until it has cooled completely.
LOWER SHEAR BUILD UP AND HARDSURFACING
For maximum performance and long life, all edges on the lower shear should be kept square and fl ush with
the blades. Check the lower shear every 80 hours and maintain it when necessary. All blade maintenance
must be done before building up and hardsurfacing the lower shear. It is recommended that this mainte-
nance be done at the end of the working day to allow adequate cooling time before putting the shear back
into service.
1.
Remove all existing hardsurfacing by grinding down to the base metal. Do not weld on top of the existing
hardsurfacing.
2.
Clean all dirt and grease from area to be maintained.
3.
Use a straight edge to determine how much build-up is required on the cross plate. If the lower wear
plates on the nose plate are worn, these should be replaced at this time (see previous page for instructions).
4.
Use the straight edge across the top of the blades to fi nd the build-up requirements on the top side of the
lower shear. All edges should be square.
5.
Preheat the area surrounding the tip to about 200°F (100°C) to remove moisture. Preheat the area within 6"
(150 mm) of the weld location to a minimum of 400°F (200°C) and a maximum of 450° (230°C). Maintain this
temperature range throughout the process.
The lower shear must be grounded when weld-
ing on the lower shear to prevent the possibility
of electric shock and arcing through the cylinder
or main pivot components.