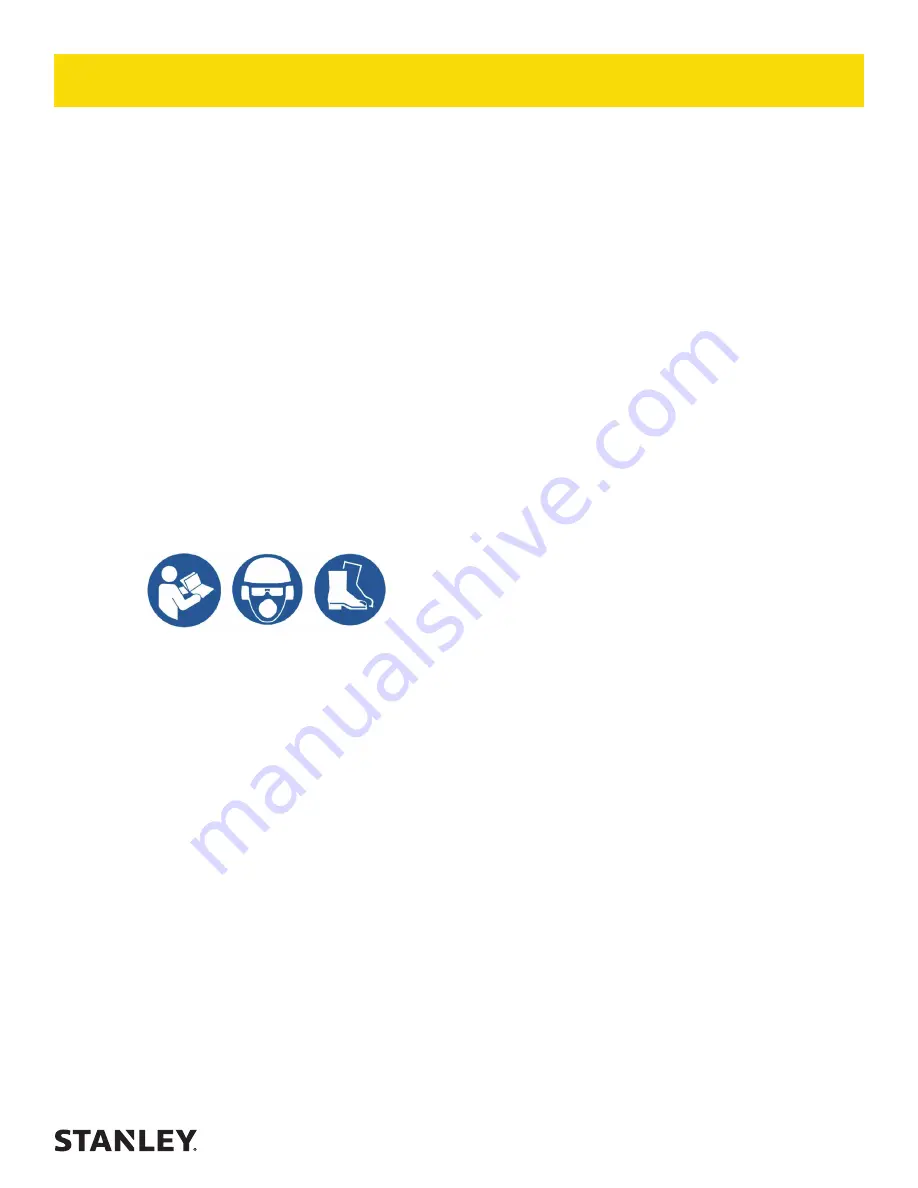
HP12 User
Manual ◄ 5
SAFETY PRECAUTIONS
Tool operators and maintenance personnel must always
comply with the safety precautions given in this manual
and on the stickers and tags attached to the equipment.
These safety precautions are given for your safety.
Review them carefully before operating the tool and
before performing general maintenance or repairs.
Supervising personnel should develop additional
precautions relating to the specific work area and local
safety regulations. If so, place the added precautions in
the space provided on page 4.
In addition to this manual, read and understand safety
and operating instructions in the engine “Operation &
Maintenance Instructions” manual furnished with the
HP12 power unit.
The HP12 will provide safe and dependable service if
operated in accordance with the instructions given in
this manual. Read and understand this manual and any
stickers and tags attached to the unit. Failure to do so
could result in personal injury or equipment damage.
•
Operator must start in a work area without
bystanders. The operator must be familiar with all
prohibited work areas such as excessive slopes
and dangerous terrain conditions.
•
Establish a training program for all operators to
ensure safe operation.
•
Do not operate the power unit unless thoroughly
trained or under the supervision of an instructor.
•
Always wear safety equipment such as goggles,
ear protection, head protection and safety shoes at
all times when operating the power unit.
•
Do not inspect or clean the power unit while it is
running. Accidental engagement of the unit can
cause serious injury.
•
Always use hoses and fittings rated at 2500 psi/172
bar with a 4-to-1 safety factor. Be sure all hose
connections are tight.
•
Be sure all hoses are connected for correct flow
direction to and from the tool being used.
•
Do not inspect hoses and fittings for leaks by using
bare hands. “Pin-hole” leaks can penetrate the
skin.
•
NEVER OPERATE THE POWER UNIT IN A
CLOSED SPACE.
Inhalation of engine exhaust can
be fatal.
•
Do not operate a damaged or improperly adjusted
power unit.
•
Never wear loose clothing that can become
entangled in the working parts of the power unit.
•
Keep all parts of your body away from the working
parts of the power unit.
•
Keep clear of hot engine exhaust.
•
Do not add fuel to the power unit while it is running
or is still hot.
•
Do not operate the power unit if gasoline odor is
present.
•
Do not use flammable solvents around the power
unit engine.
•
Do not operate the power unit within 3.3 ft/1 m of
buildings, obstructions or flammable objects.
•
Do not reverse tool rotation direction by changing
fluid flow direction.
•
Allow power unit engine to cool before storing in an
enclosed space.
•
Always keep critical tool markings, such as labels
and warning stickers, legible.
•
To avoid personal injury or equipment damage,
all tool repair, maintenance and service must only
be performed by authorized and properly trained
personnel.