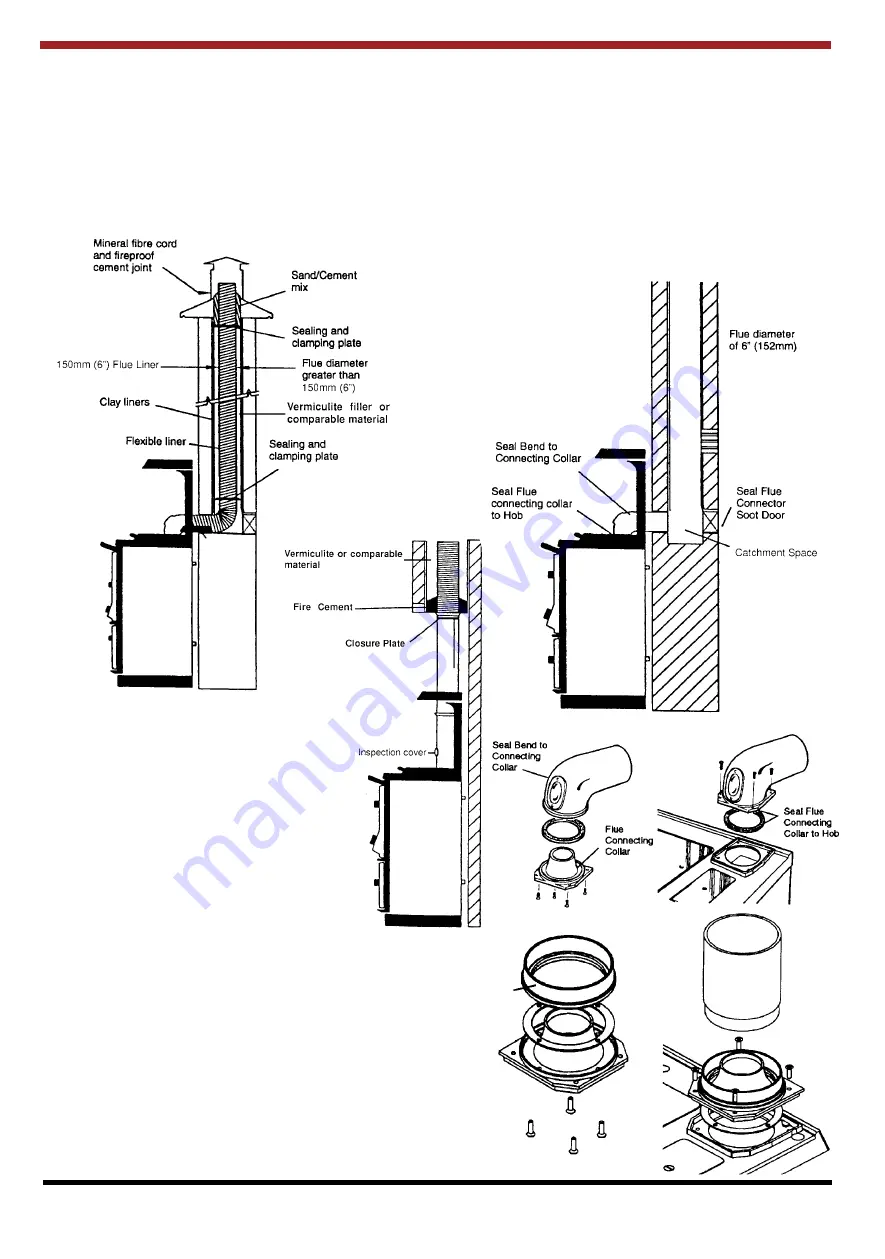
HEARTH CONSTRUCTION
When a non-combustible floor surface is not available then we recommend that the cooker be placed on a slab
of pre-cast concrete 40mm (1
1/2
”) deep or a slab of other insulating material. This hearth must extend (150mm)
6” to either side of the appliance and (225mm) 9” to the front. The cooker must stand on a flat surface.
INSTALLATION
Flue Liner greater than (150mm) 6” Diameter
150mm (6”) Salt Glazed Earthenware Flue &
Purposely Made Pre-cast Sealed Concrete
Chimney’s
CHIMNEYS
Generally the most effective chimney for gas is one
that is straight, avoid offsets and terminate an
approved low resistance flue terminal.
Fig.2
Fig.3
Fig.5
Fig.6
SEALING
This cooker and flue system operate under a
positive pressure, it is essential that all flue joints
are tightly sealed against flue gas leakage and
tested accordingly (see figs. above).
PRE-INSTALLATION CHECK
Before installing your appliance, check
that the chimney is clean and clear of
obstructions. Cracked brick-work and
leaking joints should be made good.
IT IS RECOMMENDED TO CONNECT
TO A FLUE OF 150mm (6”).
Note: Fill voids and area around liner
with vermiculite or a comparable
approved material. (See figs. above).
7
Fig.4
Fig.6a
Fig.6b
Vertical Flue
Adaptor (not
included)