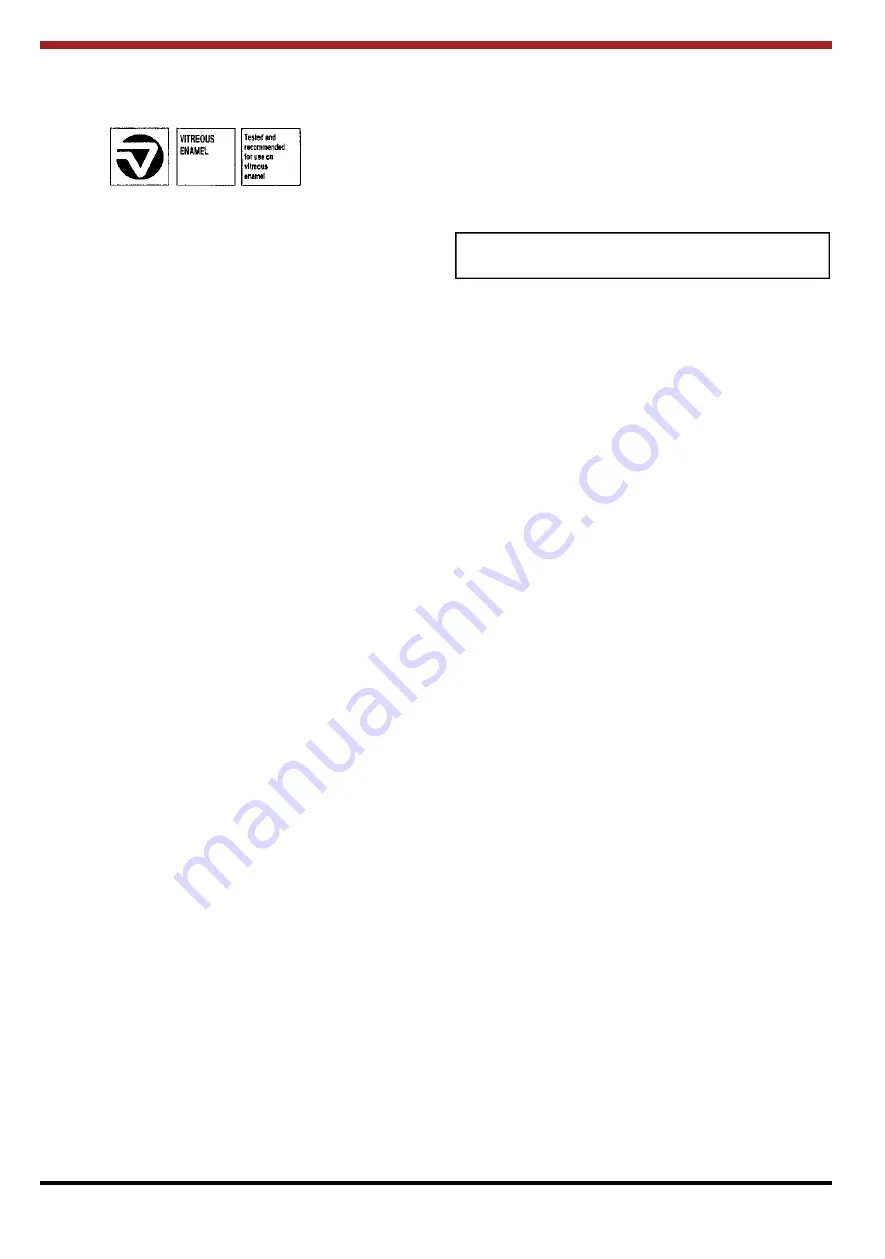
21
HOTPLATE
The hot plate may be cleaned by using a small
amount of paraffin oil or fine steel wool to remove
rust or cooking stains, dry off with a lint-free cloth
and apply a light coat of cooking oil to preserve the
finish.
WARNING: THIS APPLIANCE MUST NOT BE
INCORRECTLY USED.
SERVICING AND CLEANING OF THE
APPLIANCE
It is recommended that this appliance is serviced
annually. (see fig. 32 & 33)
1.
Ensure all electrical and fuel supplies are
isolated.
2.
Ensure that a dust sheet is placed in front of the
cooker.
3.
Remove pipe bend cleaning plate.
4.
Check the chimney and flue liner for damage or
leaks.
5.
Remove the retaining screws from the hot plate
and also the simmer cleaning plate screws.
6.
Lift off hot plate and cleaning panels.
7.
Cover the blast tube within the firebox.
8.
Carefully brush through the cleaning pipe.
9.
All deposits to be brushed down the left or right
side of the oven.
10. Deposits on the oven to be brushed downwards.
11. To remove the deposits, thoroughly clean out
the residue from the side flues and base plate,
through the oven passage cleaning door located
at the top of the warming oven.
12. Remove cover over blast tube in fire box.
13. Vacuum out the fire box area.
14. When cleaning this appliance be careful not to
damage ceramic baffles.
15. Re-assemble the cooker and carry out each
commissioning check as specified.
16. When replacing the cleaning and hot plates,
check soundness of gaskets and replace if
necessary.
5.
Use only products recommended by the
Vitreous Enamel Association, these products
carry the Vitramel label.
6.
In the oven, spills and fat splashes are
carbonised at high temperatures: occasionally
brush out with a stiff brush. The shelves can be
soaked and cleaned with a cream cleanser.
7.
Both insulating covers should be raised and
allowed to cool before cleaning the enamel with
a soapy damp cloth. Use a wire brush to keep
the cast iron hotplate clean.
DO NOT USE ABRASIVE PADS OR OVEN
CLEANERS CONTAINING CITRIC ACID ON
ENAMELLED SURFACES. ENSURE THAT THE
CLEANSER MANUFACTURERS INSTRUCTIONS
ARE ADHERED TO.
MILD STEEL
The steel side panels and splash back must not be
cleaned with steel wool. Use only washing-up liquid
in hot water with a lint free cloth. Dry off and apply
a coat of good quality furniture polish.
EXTERNAL AUTOMATIC TIMESWITCH
We recommend that this appliance be connected to
an external automatic timeswitch (not supplied)
which will control the light-up and shut-down
operation period.
CONDENSATION
If this appliance is run for extended periods on the
low settings the unit can cool down to an extent that
vapour in the flue gases may condense. This will
make the inside of the flueways damp, creating a
sooty deposit which will reduce the efficiency of the
appliance.
It is best to run this appliance occasionally at the
higher setting in order to prevent the formation of
condensation.
OVENS
Grease spillages will burn off from the oven interior
when the oven is hot and any other loose materials
can be wiped out with a cloth. When cold, stubborn
stains in the oven and on the shelves can be
cleaned off with a paste of bread soda and water.
IMPORTANT: WE DO NOT RECOMMEND DEEP
FAT FRYING ON THIS APPLIANCE.
ASSOCIATION