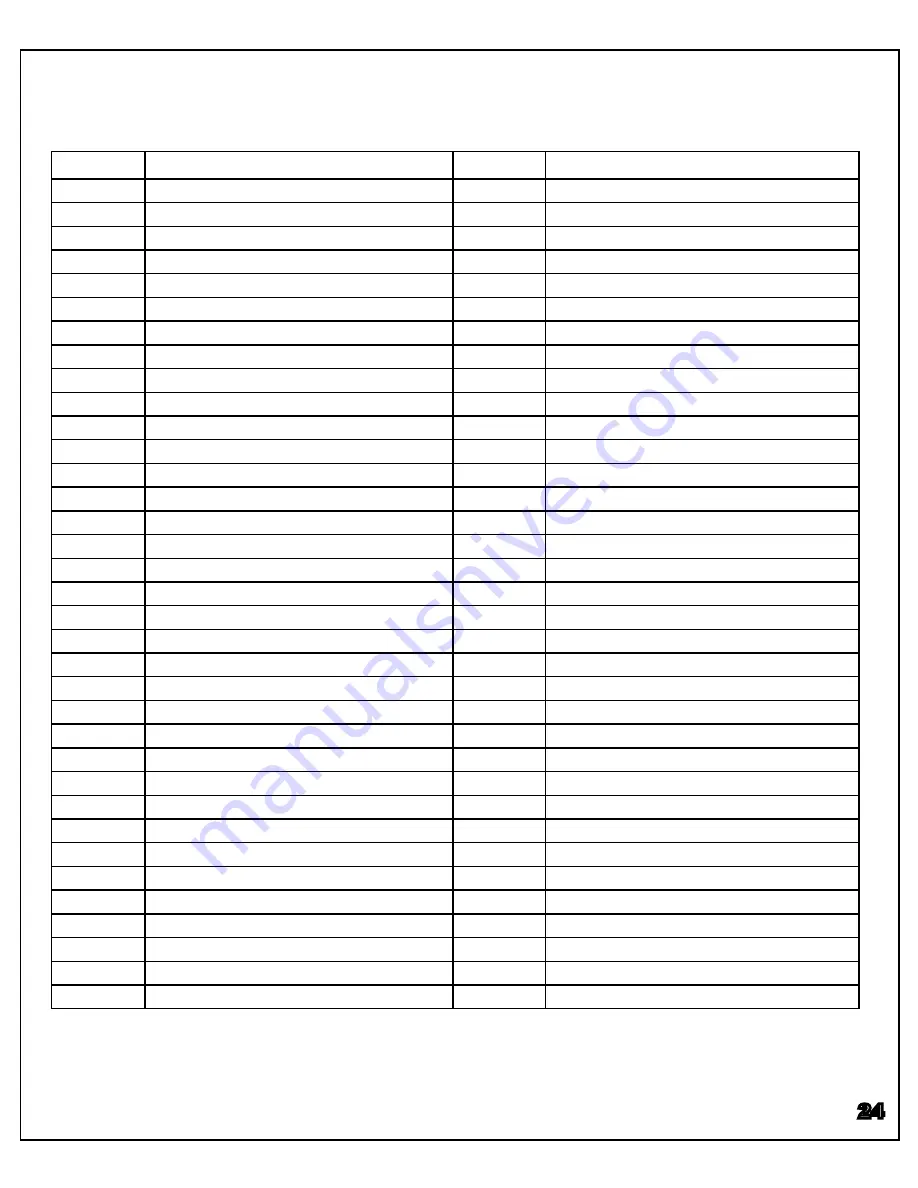
Ref.
Description
Ref.
Description
101
Hex bolt 5/16-18P*1”
135
Bearing 6004ZZ
102
Washer 5/16-16 8*16
136
Key 5*5*35MM
103
Spring 1.2*8.5*4*13
137
Lower Shaft
104
Bracket
138
Lower Wheel- Cast Iron
105
Bar Setting Plate
139
Hex Nut 3/4-16P(L.H.)
106
Flat Washer 5/16-20*2.0mm
140
Lower Wheel Guard
107
Special Washer
141
Hex Bolt 3/8*3
108
Body
142
Hex Nut 3/8-16P
109
Special Nut 3/8*4*40
143
Hex Bolt 5/16-18P*3/4”
110
Spring 3.8mm*76*18
144
Lock Washer 5/16”
111
Quick Handle Bar
145
Pin 6*16mm
112
Bearing Cover
146
Guard Locking Knob
114
Hex Bolt 8mm*118,1.25P
147
Phillips Head Screw 1/4*3/4
115
Lock Nut M8-P1.25
148
Strain Relief
116
Upper Wheel Base
149
Knob Bolt 5/16*1”
117
Upper Wheel Base
150
Power Cord
118
Upper Wheel- Cast Iron
151
LED Light Straight-Water Resistant AC
119
C-Ring R35
152
Motor Cord
120
Bearing 6202ZZ2
153
Washer 3/16”
121
Flat Washer 1/4-16*1.2mm
154
Hex Nut 3/16”
122
Tire
155
Hex Bolt 5/16-18P*1 “
123
Blade
156
Adjusting Screw
124
Lock Washer 1/4”
157
Nut 5/8”
125
Upper Wheel Guard
158
Bearing Housing
126
Pin
160
Set Screw 1/4-20P*1/4”
127
Switch w/ Large Stop
161
Wheel Pulley
128
Screw 3/16*3/8
162
Hex Bolt 1/4-20P*3/4”
128A
Screw 3/16*3/4
163
Hex Nut 1/4-20P”
129
Knob 5/16*2 “
201
Motor Pulley
130
Hex Nut 5/16-18P
202
Set Screw
131
Hex Nut 1/2-20P
203
1/4” Nut
132
Lock Washer 1/2”
204
3/8” Washer
133
V-Belt M28
205
3/8” *1-1/4” Screw
134
Cap Screw 1/4-20P*3/8”
206
Handle 3/8”
134A
Hex Bolt 1/4-20*3/8”
207
Motor
24
Parts List
Summary of Contents for CWI-B1412
Page 21: ...Bandsaw Assembly 21...
Page 22: ...22 Work Table Assembly...
Page 23: ...23 Rip Fence Assembly...