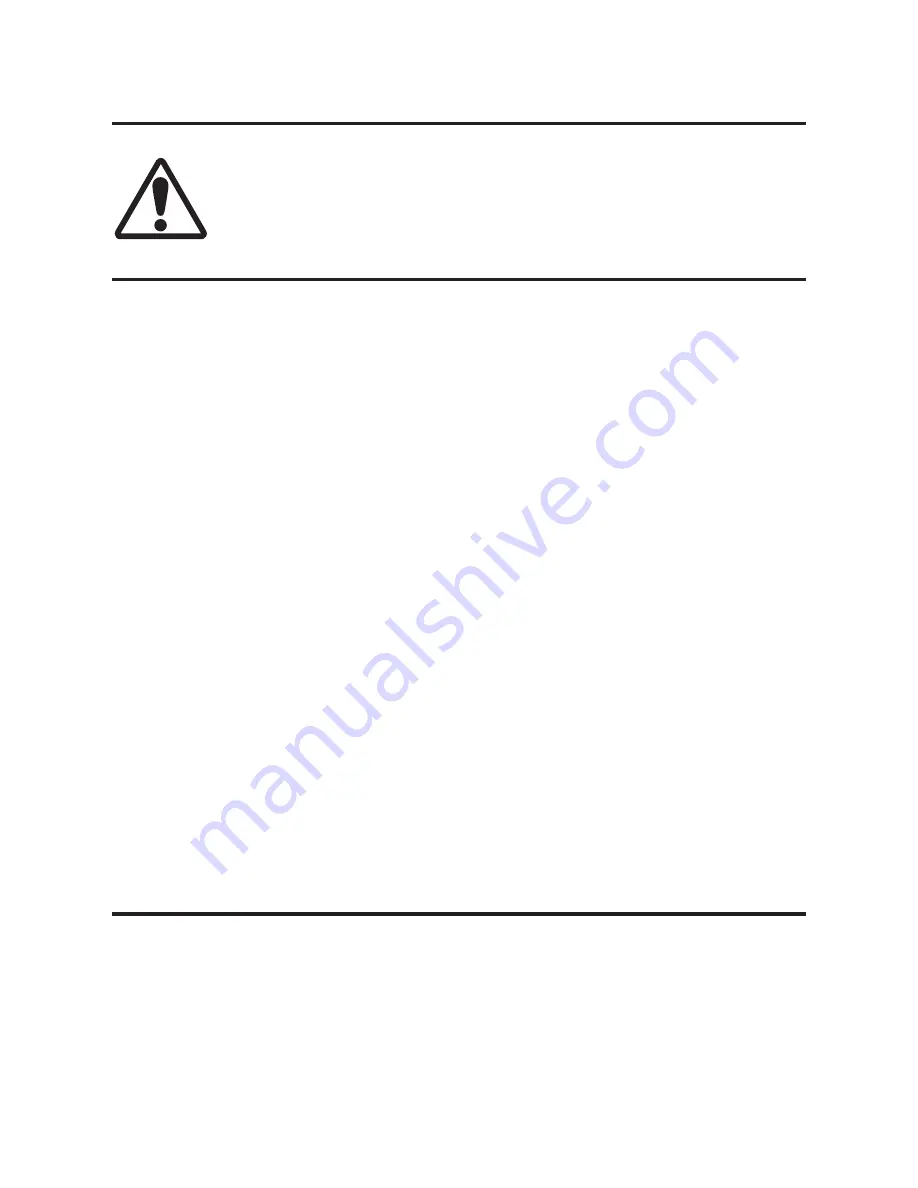
To avoid dangerous or fatal electrical shock hazard, turn OFF
power to motor and remove plug from power outlet before
working on pump or motor.
Routine Maintenance requires regular checking of the pump to ensure no water is
leaking from joints whilst pump is operating and inspection/cleaning of trap basket.
Debris or trash that collects in basket will choke off water fl ow through the pump.
Do not operate pump with trap basket missing or damaged.
Follow instructions below to clean trap:
1. Switch off power to pump, close valves in suction and discharge, and release all
pressure from system before proceeding.
2. Remove trap cover (turn clockwise). If necessary, tap handles gently with a rubber
mallet or use a board as a lever.
3. Remove strainer basket and clean. Ensure all holes in basket are clear, fl ush basket
with water and replace in trap with large opening at pipe connection port (between
ribs provided). If basket is replaced backwards, the cover will not fi t on trap body.
To clean tranparent cover, use water and neutral soap only. Do not use solvents.
4. Clean and inspect lid o-ring; reinstall on trap.
5. Clean O’ring groove on trap body and replace cover. To help keep cover from
sticking, tighten hand tight only.
6. Prime pump (refer priming instructions).
Pump Service
Pump should only be serviced by qualifi ed personel. For best results, use only
genuine Onga service parts. Be sure to prime pump before starting.
Before removing clamp or trap cover:
1. SWITCH OFF POWER to pump before proceeding.
2. CLOSE SHUT-OFF VALVES in suction and discharge pipes.
3. RELEASE ALL PRESSURE from pump and piping system.
4. NEVER tighten or loosen covers, valves, nuts or bolts while pump is
operating!
11
Service & Maintenance
Summary of Contents for SilentFlo SF1100100
Page 16: ...15 Notes...
Page 17: ...16 Notes...