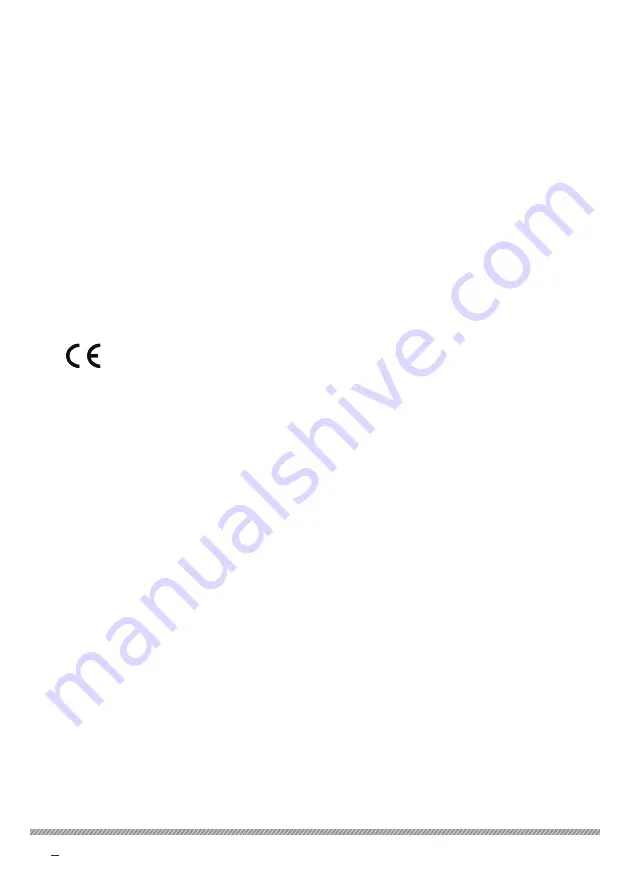
1
Introduction
1
1 Introduction
Introduction
The 3600XRi DC Drive is an isolated, 4 Quadrant speed controller for brushed shunt wound
or permanent magnet DC motors. This Class 1 product has basic insulation and protective
earth. Its control signals are isolated from the mains AC supply, and their connection to
other isolated instruments is permitted.
Electrically isolated control circuits allow interfacing to external sources.
It has both speed and current control modes and can motor or regenerate in both forward
or reverse directions of rotation. The drive incorporates a fully controlled thyristor bridge
with a current loop to protect the drive and motor. It uses an accurate current control loop
to protect itself and the motor.
This component is hazardous. Please obtain expert help if you are not qualified to
install this equipment. Make safety a priority.
Read about the general risks and warnings at the front of this manual.
This apparatus complies with the protection requirements of the relevant EU
Directives. UL file: E168302.
• All models are of open chassis construction only for use in a suitable enclosure with a
fused supply. For suitable fuses refer to "10 Specifications" on page 26.
• The unit uses closed-loop control of both armature current and feedback voltage for
precise control of motor torque and speed.
• A stall timer protects the motor and drive and automatically removes power after 30
seconds if the required speed is not achievable. Durng this period, the unit can provide
up to 150% of the preset maximum current for up to 30 seconds allowing for high, short-
term torques during acceleration etc.
• Electrically isolated control circuits allow interfacing to external sources.
• Independent control of either the current or speed loops by external inputs allows for
torque or speed control applications with overspeed or overcurrent protection.
• Derive the speed demand signal from either a potentiometer, 0-10 V signal or 4-20 mA
current loop. A bipolar speed demand is only possible with a voltage input.
•
Speed feedback signal selection: ARMATURE VOLTAGE, or shaft-mounted TACHOMETER.
• On-board function switches select the SPEED and CURRENT ranges.
• Independent adjustment presets provide FORWARD UP RAMP, FORWARD DOWN RAMP,
REVERSE UP RAMP, REVERSE DOWN RAMP.
• The positive and negative current limits are independently adjustable.
• Motor braking can be fast or ramped, and provision is made to adjust the motoring and
braking torque independent of rotation direction. The unit returns braking energy to the
supply.
• Control the shaft direction using linear voltage signals or pushbuttons.
• The unit can directly connect to a PLC logic controller.
• The unit has a comprehensive range of extra inputs and outputs.