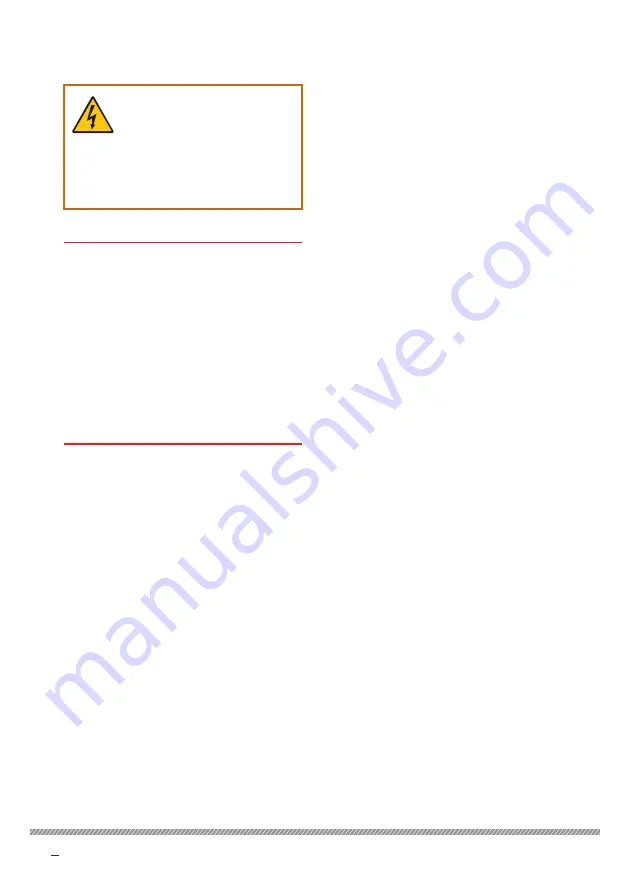
5
Installation
6
6 Installation
Installation
WARNING!
ELECTRIC SHOCK HAZARD
Disconnect the mains supply
before working on the unit. DO
NOT TOUCH PRESETS, SWITCHES
AND JUMPERS! Always use the
correct insulated adjustment
tools.
6.1 Motor installation
• Foot-mounted motors must be level and
secure.
• Ensure accurate alignment of the motor
shaft and couplings.
• Do not hammer pulleys or couplings
onto the motor shaft.
• Protect the motor from ingress of
foreign matter during installation.
Earthing:
Connect the motor to the system
enclosure earth.
6.2 Drive installation
Requirements during installation and
operation:
• Avoid vibration.
• Protect the drive from pollutants.
• Ambient operating temperature must be
within -10ºC and +40ºC. To comply with
UL requirements, the temperature of the
surrounding air must not exceed 50ºC.
POWER CABLING
: Use correctly rated
cable: minimum 600 Vac, 2 x armature
current, enclosed in metal conduit or
trunking, or screened. The screen must be
earthed at the motor and drive - refer to "5
Requirements for EMC compliance" on page
FUSING
: The drives MUST BE FUSED
EXTERNALLY with semiconductor fuses. The
fuses must be semiconductor types with
a maximum amps squared seconds rating
according to the Rating table, page 28).
The fuse current rating must be at least
1. 75 times the armature current. The
voltage rating must be suitable for the
AC supply. Failure to use the correct
semiconductor fuse ratings will invalidate
any warranty. Special consideration must
be given to installations in member states
of the EU. Refer to "5 Requirements for EMC
CONTROL SIGNALS
: Avoid running signal
cables close to power cables. Earth the
screens at the drive end only.
SUPPRESSION
: The drives have excellent
noise immunity. However, installations
involving electrical welding or RF induction
heating may require further filters on the
line and armature terminals. Contactor coils
and sparking contacts may also require
suppression. A 100 Ω resistor in series with
a 0.1 µF capacitor is usually adequate in
these situations.
MECHANICAL:
Optimise heatsink airflow.
Avoid vibration and ambient temperature
outside -10 to +45°C. Protect the drive from
pollutants.
MOTOR:
Ensure the motor is correctly
wired and that the motor and load are
free and safe to rotate. The motor must
ideally have a minimum armature time
constant of approximately 10 ms (T = L/R).
For motors with lower time constants e.g.
servo-motors, use an armature choke in
series with the motor (refer to the motor
supplier for choke data). Failure to do this
may cause damage.