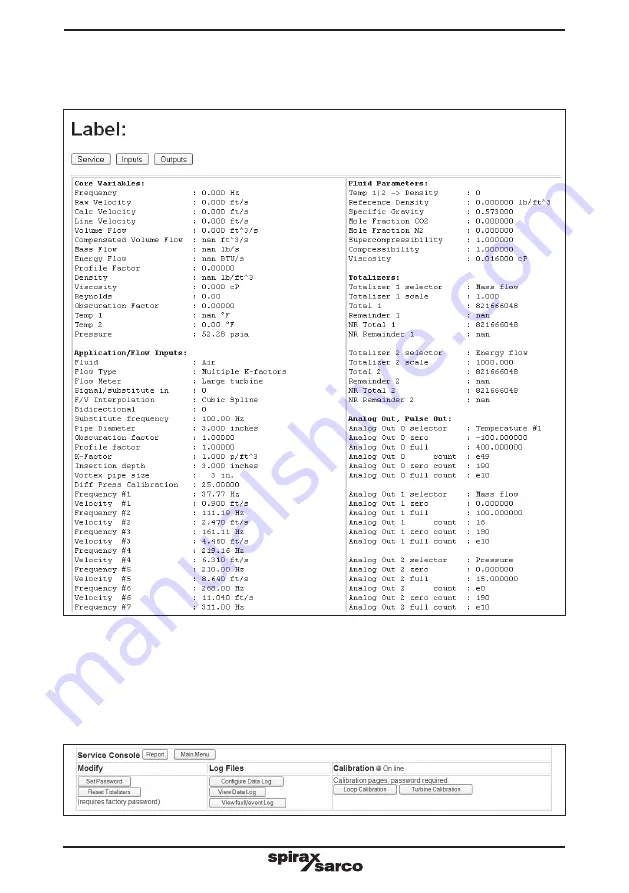
IM-P198-02
MI Issue 5
80
5.
The Data Log page shows a list of selected flow parameters that are saved to flash
memory at selected intervals. The data log will wrap after 'x' lines.
To view faults and history, return to the service console by clicking the Service button.
At the Service Console, click either the View History data or View fault/event log buttons.
4.
The report page is a condensed text display of all internal settings. To view an output
or input report, click on the Report button in the Operations line.
Fig. 91
Fig. 92