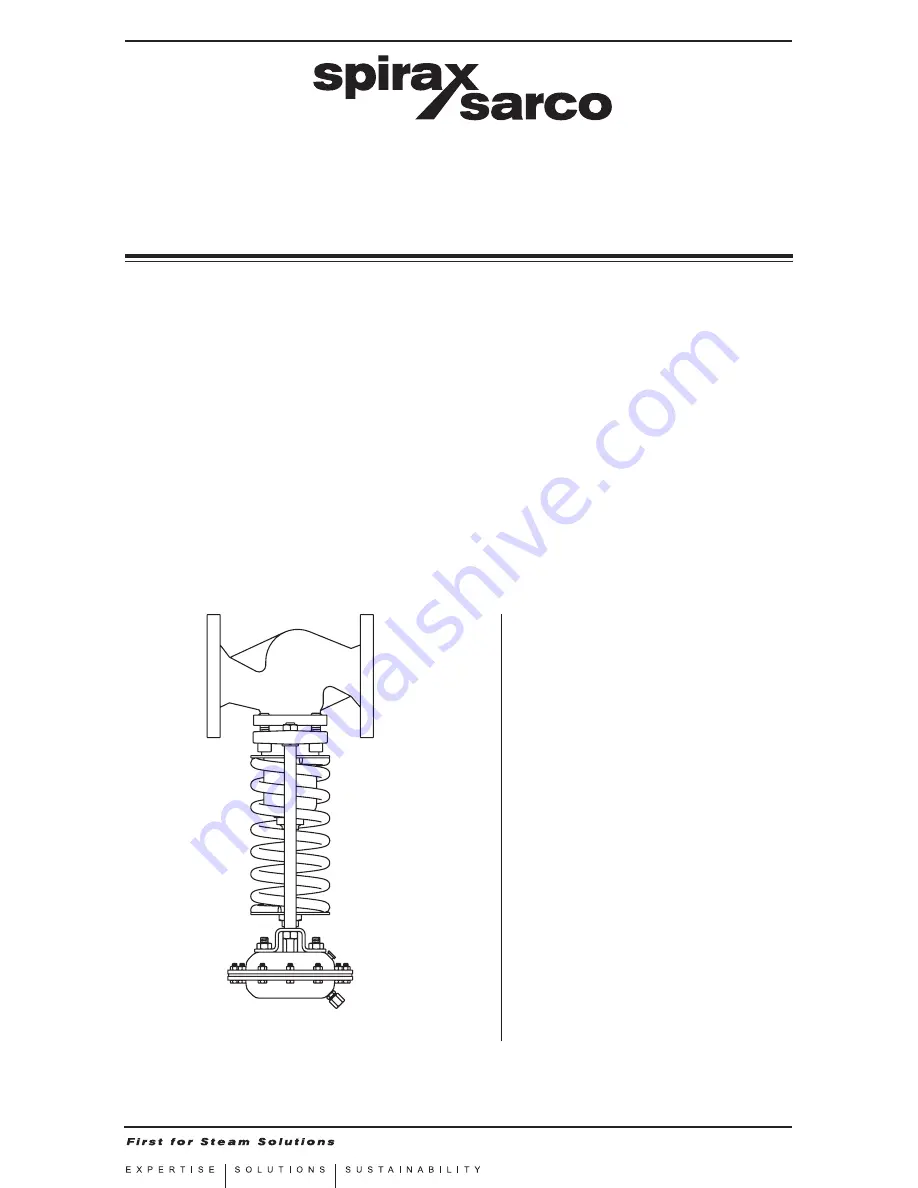
IM-P204-03
CH Issue 8
1
1. Safety information
2. General product
information
3. Installation
4. Maintenance -
DN15 to DN32 valves
5. Maintenance -
DN40 to DN100 valves
6. Spare parts
© Copyright 2016
Printed in GB
IM-P204-03
CH Issue 8
2046050/8
DLV7 SG Iron
Pressure Reducing Valve
Installation and Maintenance Instructions
Summary of Contents for DLV7
Page 40: ...IM P204 03 CH Issue 8 40...