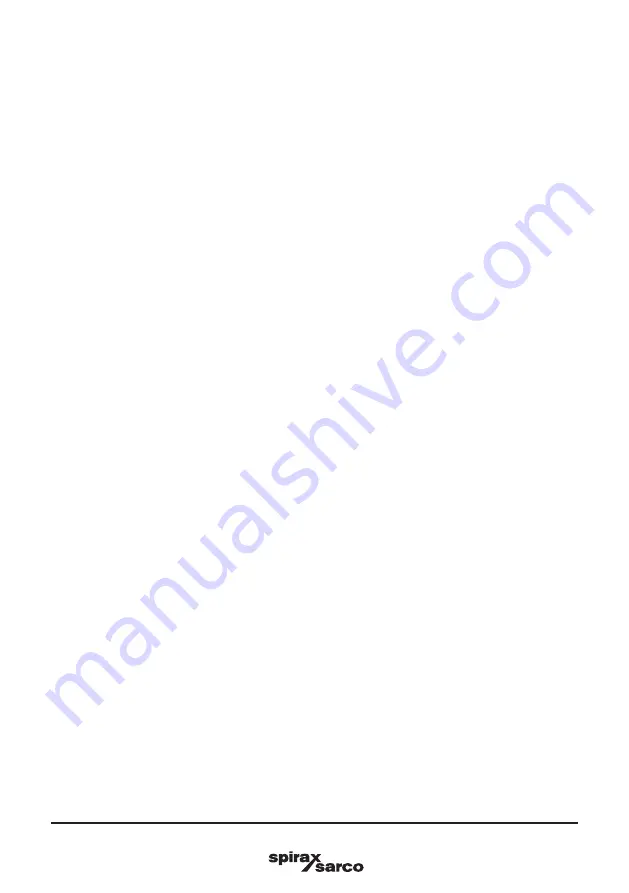
IM-P537-01
EMM Issue 1
34
Pressurised Thermophysical deaerator with operator manual for the control unit
5.2.2 Auxiliary circuit protection
The auxiliary circuit is protected against overloads by a circuit breaker. Each solenoid valve or actuated valve
is also protected by a fuse on corresponding terminals panel.
5.2.3 Protection interlocks
The electromechanical protections with partial/total system interlocks are the following:
-
High pressure → closes primary steam control valves for pressure (YY1), temperature (YY2) and Shut
Off Steam (YY05) (optional) (requires manual reset if set in PLC);
-
Low level→ closes primary steam control valves for pressure (YY1), temperature (YY2) and Shut Off
Steam (YY05) (optional) (requires manual reset if set in PLC);
-
High level → closes the water control valve (YY3), blocking the feed and controls the OVERFLOW valve
(YY04) (timed control);
-
External alarm or consent denied (if used) → closes all control valves, shutting off or stopping heating/
pressurising and water supply.
In addition, the system is protected against the following events:
-
Blackout (or sudden panel shut-down/emergency shut-down pressed) → the control valves (primary
steam and feedwater), both pneumatically and electrically actuated, are fail-safe (N.C.). Therefore,
in the event of a power failure, they return to the safety position (closed), shutting off the supply of
technological steam and feedwater. After a blackout, the system is prepared to be restarted manually.
This functionality can be changed (automatic restart), via the PLC
-
Pneumatic air supply shut off (or low pressure) → where pneumatically actuated control valves are
provided, the pneumatic supply shut off or insufficient pressure, closes or limits the opening of the
control valves, shutting off or limiting the supply of primary steam and feedwater. Insufficient pneumatic
air pressure, even temporarily, could cause control instability or may set off alarms
5.2.3 Digital I/Os
For a possible basic interfacing with the external automation, the following digital I/Os are commonly supplied
(all versions):
-
DI: Start system remotely (with mode selector set to REM): stable contact (closed = start) -
-
DI: consent/external block: stable contact (closed = OK, open = block) -
-
DI: possible external pump in motion
-
DO: System feedback in operation: SPDT contact -
-
DO: voltage presence feedback: SPDT contact -
-
DO: cumulative alarm feedback: SPDT contact
-
DO possible external pump control
5.2.4 Communication interface (serial bus)
Units equipped with PLC logic control can be prepared for interfacing with external monitoring/control
system via serial bus. The available communication protocols are listed in the technical specification of the
product. Refer to the additional documentation provided with the unit for the supplied protocol specifications,
interfacing instructions and address register.