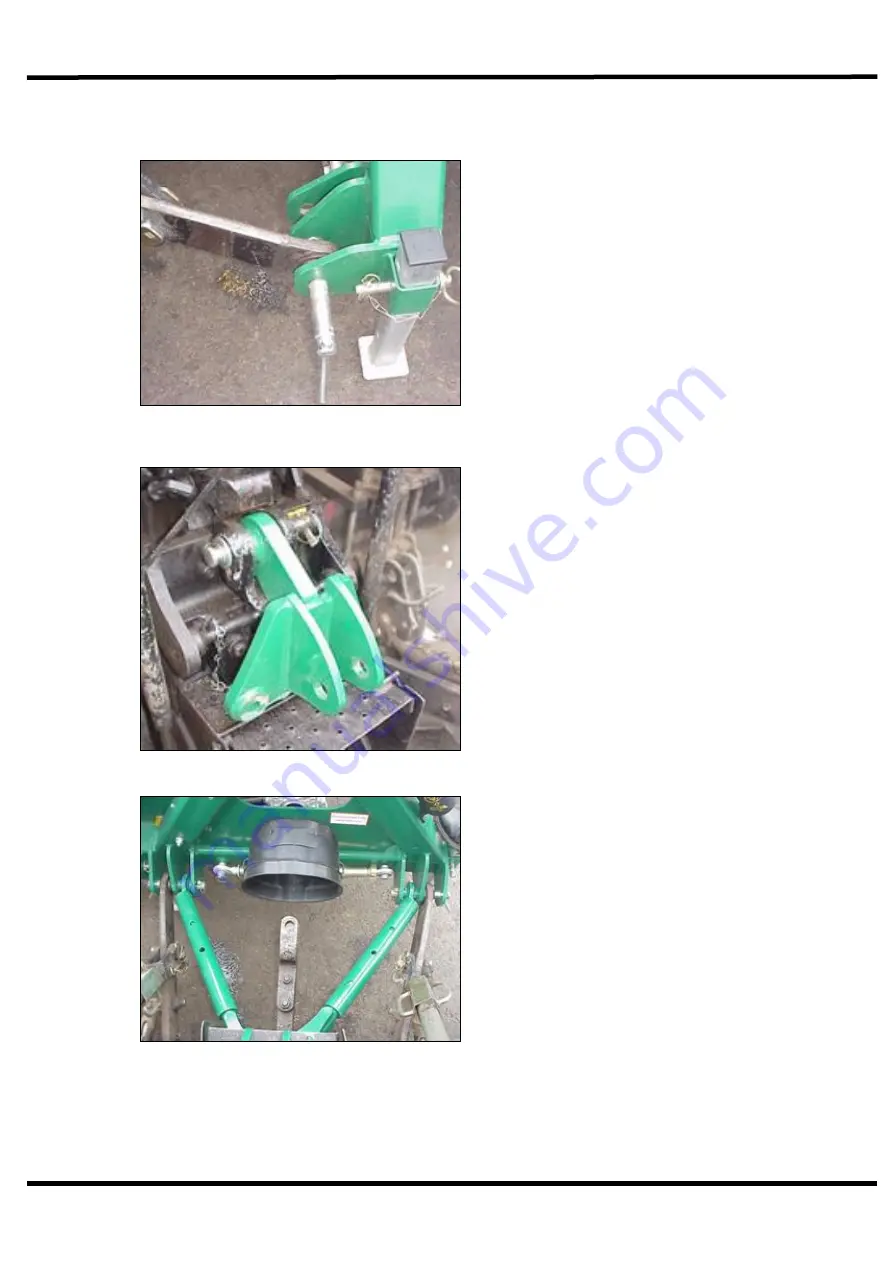
TWIGA CLASSIC S50
13
Attaching Machine to Tractor
–
3 Point Linkage
1. Reverse tractor to machine and
attach lower links. You will also need
to attach the lower stabiliser tubes as
they share the same pin.
2. Fit stabiliser bracket into top link
clevis and fit top link. The standard
link comes with a Cat III hole plus a
Cat III to Cat II reducing bush, a
28mm bracket is available on request.
3. Fit stabiliser tubes between A frame
and stabiliser bracket. Ensure the
tubes are free to slide, do fit locking
pins.