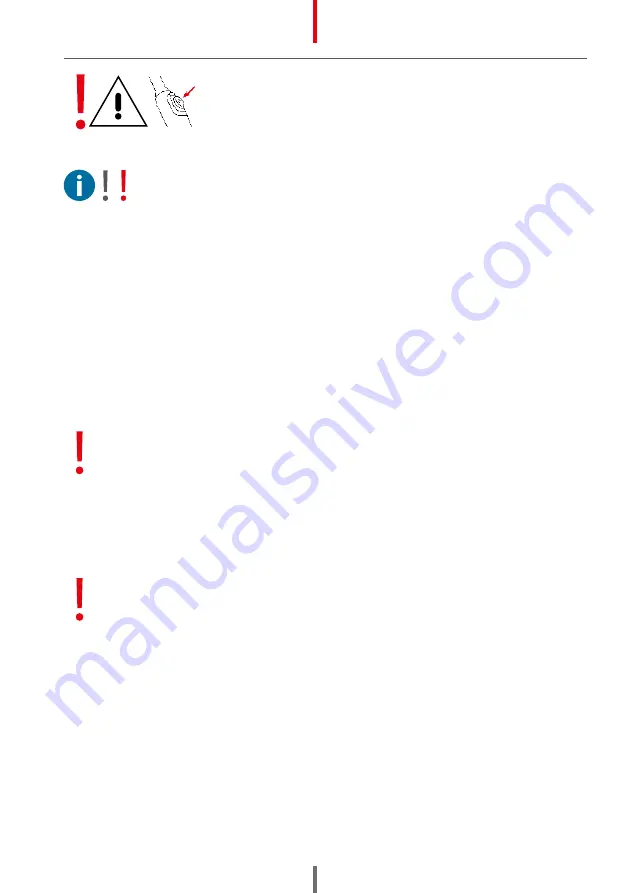
USER’S MANUAL
EN
7
WARNING
!
The maximum voltage of 15kV. Accidental pressing of the microswitch
results in unintentional arc ignition. Never bring a bare hand close to the
electrode, when the device is connected to a power source.
1.9 SYMBOLS USED IN INSTRUCTIONS
We use this symbol to pay your attention about important information.
2. ELECTROMAGNETIC FIELDS (EMF)
Electric current flowing through any conductor causes localized electric and magnetic fields
(EMF). All welders should use the following procedures in order to minimize the risk associated
with exposure to EMF from the welding circuit:
• Route the welding cables together – secure them with tape when possible.
• Place your torso and head as far away as possible from the welding circuit
• Never coil welding cables around your body.
• Do not place your body between welding cables. Keep both welding cables on the same
side of your body.
• Connect the return cable to the workpiece as close as possible to the area being welded.
• It is forbidden to sit or lean on power source while working.
• Do not weld whilst carrying the welding power source or wire feeder.
WARNING!
The electromagnetic field (EMF) generated during welding (and allied processes) may interfere
with the operation of implanted medical devices for example: cardiac pacemakers. Persons with
implanted medical devices such as cardiac pacemakers are obliged to consult a doctor before
starting to weld/plasma cutting and to exercise special caution during work. It is forbidden for
such persons to be present in the vicinity of the place where welding/plasma cutting processes
are realized without previous consultation of a doctor.
3. ELECTROMAGNETIC COMPATIBILITY (EMC)
WARNING!
This Class A equipment is not intended for use in residential locations where the electrical
power is provided by the public low-voltage supply system. There can be potential difficulties
in ensuring electromagnetic compatibility in those locations due to conducted as well radiated
radio-frequency disturbances.
3.1 GENERAL INFORMATIONS
The user is responsible for installing and using the arc welding equipment according to the
manufacturer’s instructions. If electromagnetic disturbances are detected, then it shall be the
responsibility of the user of the arc welding equipment to resolve the situation with the tech-
nical assistance of the manufacturer. In some cases this remedial action may be as simple as
earthing the welding circuit. In other cases, it could involve constructing an electromagnetic
screen enclosing the welding power source and the work complete with associated input fil-
ters. In all cases electromagnetic disturbances shall be reduced to the point where they are no
longer troublesome.