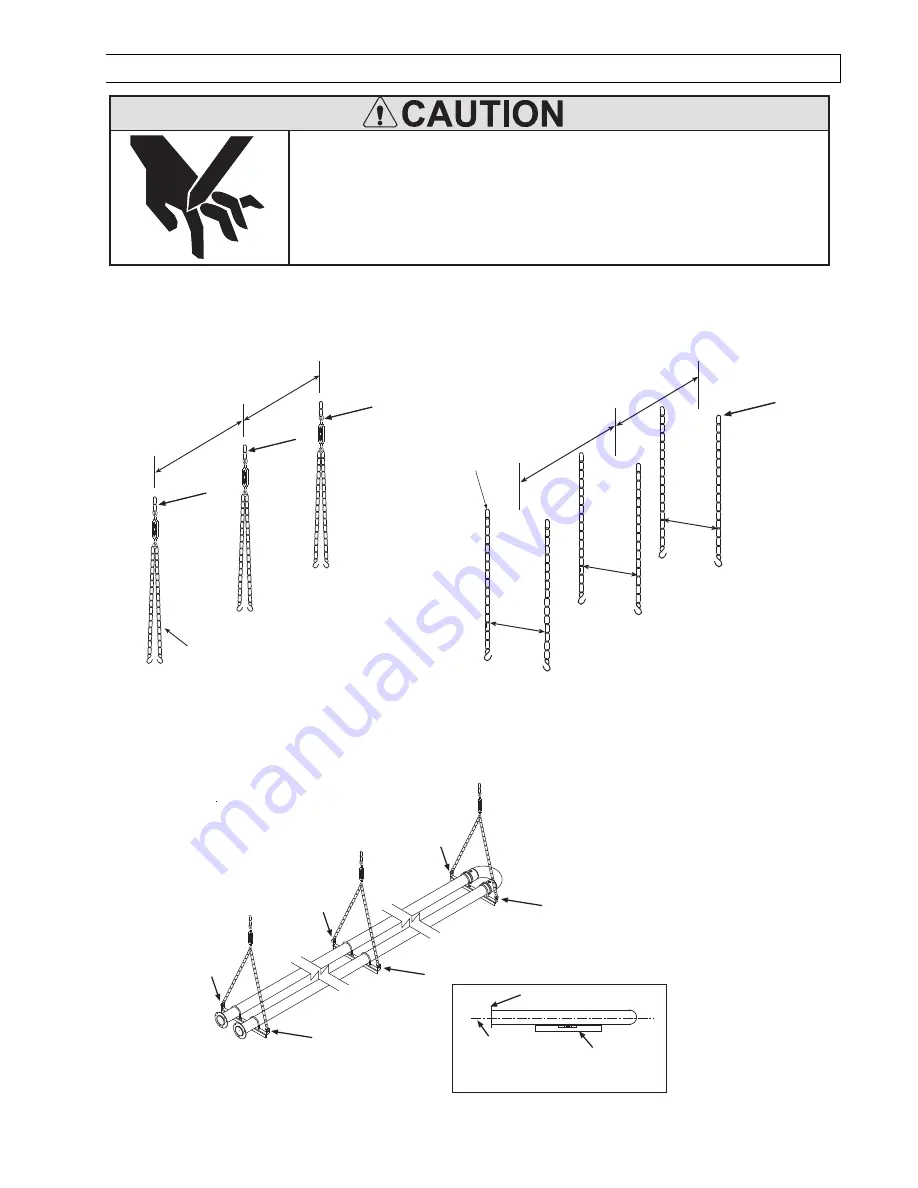
Form #42710000
May 2013
-9-
10.1
HEATER ASSEMBLY
Sheet metal parts, particularly reflectors and vent have sharp
edges. Always use gloves when handling.
Failure to do so may result in death, serious injury or property
damage.
CUT HAZARD
During field assembly of the heater, the recommended procedure is as follows:
1.
Put the suspension in place (according to Section 7.0) using proper suspension method (see Section 9.0).
1
1
1
88
82
chains for suspension
on the control box end
88
82
Suspension
Chain
18-1/2
18-1/2
18-1/2
1
Trapeze Method
Trapeze Method
Trapeze Method
Trapeze Method
Individual Suspension Method
Individual Suspension Method
Individual Suspension Method
Individual Suspension Method
2.
Lift the tube section and suspend it into place. When lifting, caution should be used to avoid damaging the
assembly. Make sure that the long axis of heater is level.
3.
Assembly the reflectors onto the tube section. Leave 3” space between the tube flange and the first reflector
for later mounting of control box and draft inducer.
2
2
2
2
2
2
Tube Flange
Level indicator
The long axis of heater
Side View