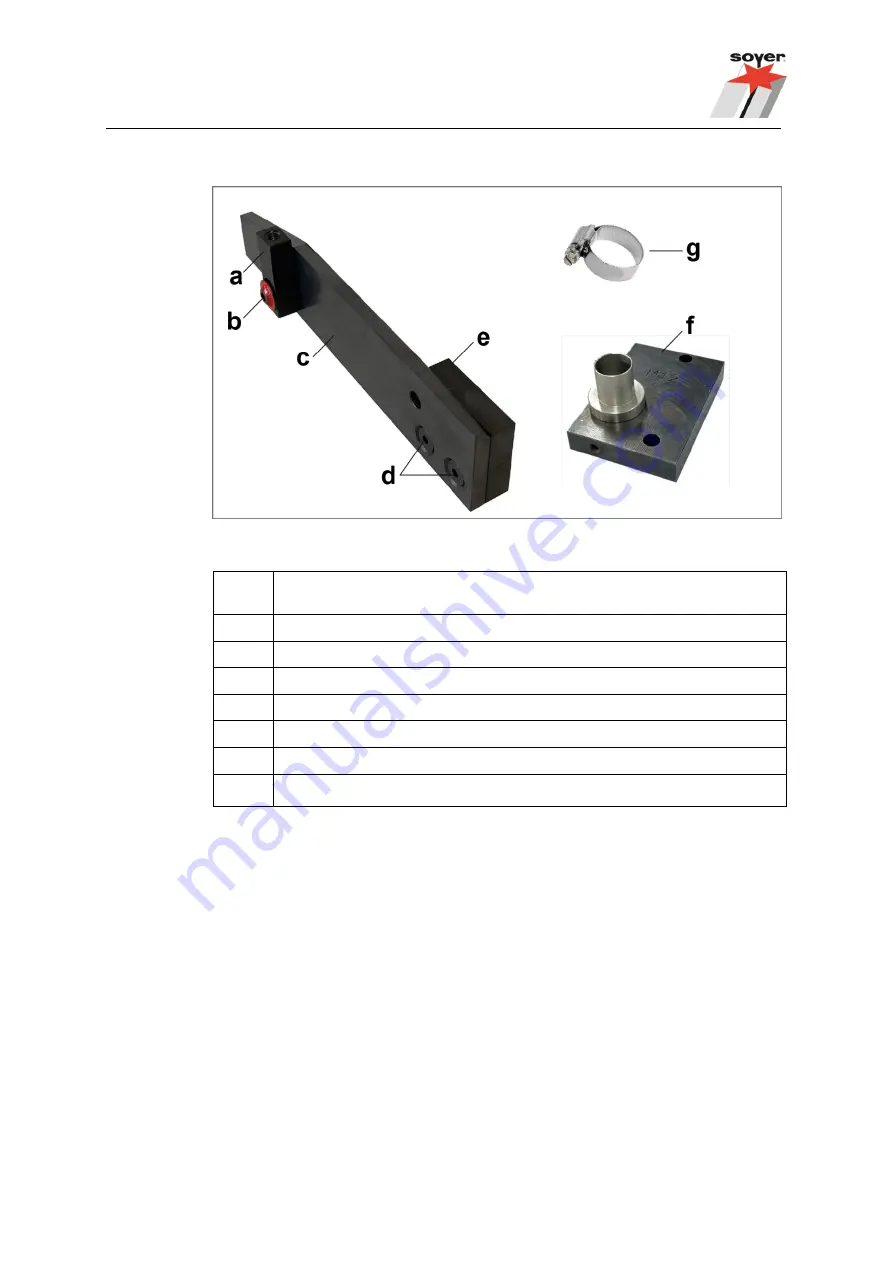
Operating instructions UVR-300/UVR-400 | Heinz Soyer Bolzenschweißtechnik
35
7.1.2
Conversion set for UVR-400 (M10, M12 and Ø 10.8)
Figure 9: Conversion set with replaceable parts for UVR-400
Item
Designation
a
Limit stop for fixing bracket
b
Lens flange screw
c
Guide rail
d
Countersunk Allen screw
e
Distance piece
f
Hose connection
g
Hose locking device
All conversion set parts can be ordered separately. Please refer to chapter
Individual parts for the UVR-400 conversion set (M10, M12 and Ø 10.8)